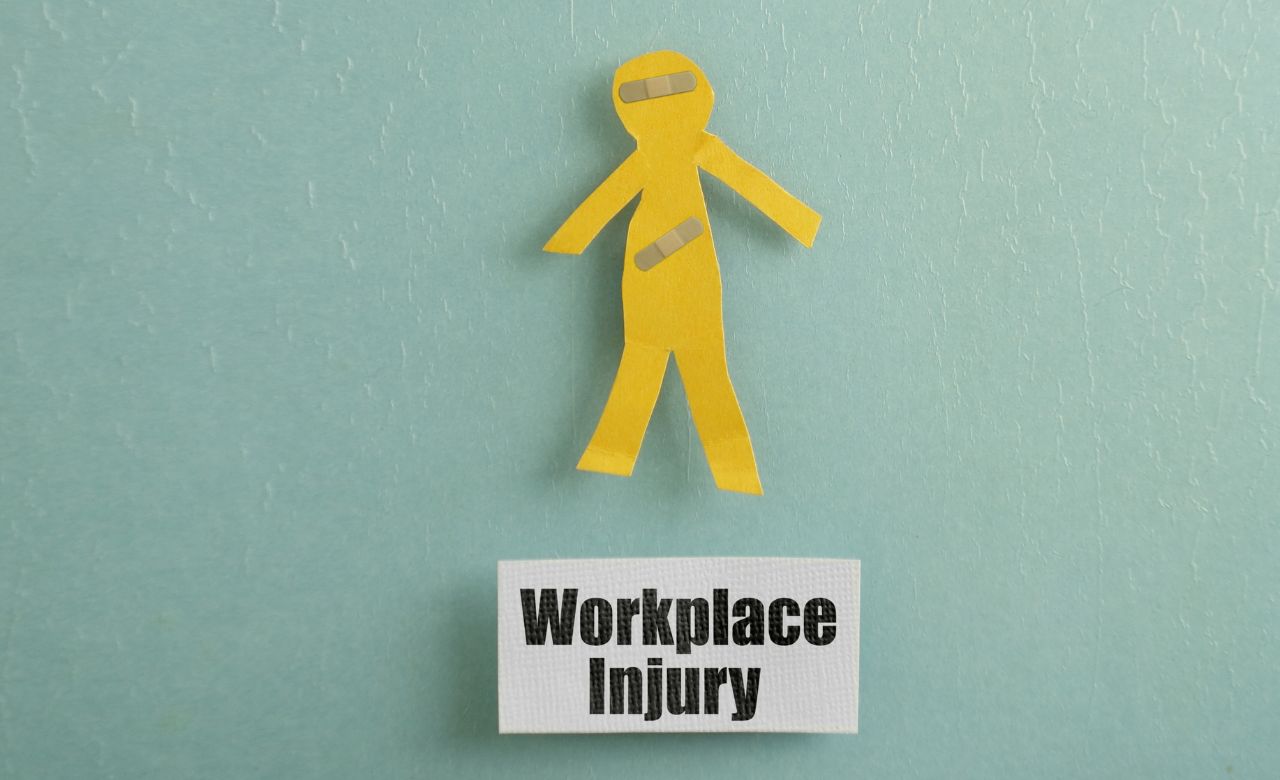
Understanding what is the biggest cause of workplace injury can help prevent accidents at work and ensure legal compliance.
Workplace injuries are a significant concern, impacting employees, contractors, and the public. Despite robust health and safety regulations, thousands of injuries at work still occur annually.
According to the Health and Safety Executive (HSE), 604,000 workers sustained a non-fatal injury in the workplace in 2023/24. In 2023/24, 138 workers and 87 members of the public were killed in work-related accidents.
The human and financial cost, which runs to billions of pounds every year, underscores the importance of employers taking proactive steps to mitigate risks, protect employees, and comply with legal obligations.
What are an employerโs legal obligations for health and safety?
By law, employers must identify hazards in the workplace, assess the potential risks and take measures to remove, prevent or control them.
Health and safety trainingย is a vital control measure to raise awareness of the risks, and training is a legal requirement under many health and safety regulations such as the Provision and Use of Work Equipment Regulations 1998 (PUWER) and the Manual Handling Operations Regulations 1992
Key legislation such as the Health and Safety at Work etc. Act 1974, the Management of Health and Safety at Work Regulations 1999, and industry-specific regulations like the Control of Substances Hazardous to Health (COSHH) Regulations 2002 mandate an employerโs responsibilities.
Health and safety training raises awareness and provides employees with the knowledge to manage risks effectively.
What is the biggest cause of workplace injuries?
Here are the 10 most common workplace injuries:
1. Exposure to hazardous material
Every year there are an estimated 12,000 deaths from lung disease linked to past exposures at work, of which 20% are caused by asbestos.
Hazardous substances are the biggest cause of fatalities at work, posing a serious risk to employees. Exposure to liquids, dust, gases and fumes can lead to respiratory problems, burns, scalds and eye injuries. It can also lead to serious conditions such as asthma, skin disease and lung cancer.
Theย Control of Substances Hazardous to Health (COSHH)ย law places legal duties on employers to prevent, reduce or control exposure among employees and visitors.
Employeesย handling hazardous substancesย must use appropriate controls and systems of work developed following a risk assessment which might include the use of personal protective equipment. Substances must be properly stored with flammable materials kept in closed containers inside fire resistant cabinets or bins designed to retain spillages.
Hazardous substances must also be appropriately labelled with details about the substance and what to do in the event of accidental or acute exposures.
At Praxis42 we offer COSH Training for all employees who handle or who may handle hazardous materials at work. We also provide Asbestos Awareness Training for employees who may be at risk of exposure.
2.ย ย ย ย Slips and trips
In 2022/23, slips and trips on the same level accounted for 19,406 non-fatal injuries to employeesย reported underย RIDDOR legislation.
Most injuries from slips and trips are caused by obstructions, contamination of walkways and uneven or unsuitable surfaces.
The measures you need to take to prevent such injuries are generally straightforward. They include making sure:
- Walkways are free of obstructions such as trailing cables, personal belongings and stored items.
- Surfaces are suitable for the environment, cleaned, fitted correctly and properly maintained.
- Lighting is sufficient so employees can see and avoid any hazards.
- Slippery surfaces are assessed and treated with suitable cleaning regimes in place.
- Rugs and mats are fitted securely.
The Health and Safety Executive has published a usefulย slips and trips: hazards spotting checklist.
Our Praxis42 IOSH Approvedย Slips, Trips and Falls Training helps raise employee awareness of the common causes of these accidents and how to prevent them.
3.ย ย ย ย Manual handling injuries
Manual handling accounted for 17% of workplace injuries in Great Britain in 2022/23. Injuries include musculoskeletal disorders (MSDs) such as pain and injuries to the back, shoulders arms, legs and other joints.
Theย Manual Handling Operations Regulations 1992ย define manual handling as โany transporting or supporting of a load (including the lifting, putting down, pushing, pulling, carrying or moving thereof) by hand or bodily forceโ.
Manual handling should be avoided where possible. If not, employers must assess the risk of workplace injury by considering theย task,ย individual capability,ย load andย environment where the work is undertaken โ often referred to asย TILE.
At Praxis42 we offer a Manual Handling Course which supports your organisation to be fully compliant with the Manual Handling Operations Regulations by ensuring employees are aware of the risks and how to control them. We also offer a specialised course for office workers: Office Manual Handling.
4.ย ย ย ย Upper limb disorders (ULDs)
Of the more than 10,000 people who suffer from work-related musculoskeletal disorders every year, 45% have repetitive strain injury (RSI) and upper limb disorders (ULDs). This includes chronic or acute pain and aches, inflammation of joints, tendons and ligaments, tingling, numbness, cramp, burning, redness and swelling.
RSI and ULDs can result from:
- Prolonged repetitive work, particularly using the same hand or arm action.
- Uncomfortable or awkward working postures.
- Tasks being carried out for a long time without breaks.
- Working with hand-held power tools for long periods of time.
Theย Display Screen Equipment (DSE) Regulations 1992ย aim to protect employees who use equipment such as laptops and mobile devices such as tablets daily for more than one hour at a time.
By law, employers must:
- Carry out aย workstation assessment.
- Reduce risks, including ensuring DSE users take regular breaks or do something different.
- Arrange an eye test for an employee who asks for one and provide glasses if an employee needs them only for DSE use.
- Provideย Display Screen Equipment Trainingย for employees even if working away from the office.
5. Injuries from fires
Of the 13,295 non-dwelling fires in 2023/24, 18 people were killed, and 857 people suffered non-fatal injuries.
To prevent and detect fires, workplaces must undertake aย fire risk assessment, have appropriate fire detection systems in place, and means of evacuating the premises safely in the event of an emergency. Suitable fire-fighting equipment andย extinguishersย must also be in place to aid escape.
Employers must have a plan that tells employees what they must do if they discover a fire. It must also outline what warning systems are in place, the evacuation procedures and routes, and the fire assembly point.
Our Online Fire Safety Training, which has been developed by qualified, experienced health and safety professionals, helps employees to understand how to prevent fires and what to do if there is a fire in the workplace. We also offer Fire Marshal Training for those who are responsible for ensuring safe evacuation in the event of a fire.
6. Being struck by objects
Being struck by a moving object caused 606 injuries at work in 2022/23. It is one of the most common causes of non-fatal injuries at work, followed by being hit by a moving vehicle.
Employees and pedestrians in the workplace should be segregated from moving objects and vehicles and should wear suitable personal protective equipment where a risk assessment shows they are required, such as hi-visibility clothing or head protection to reduce injuries from falling objects.
Tools and other equipment should be kept in suitable storage areas, while walkways may require physical barriers where internal transport operate or be clearly marked where hazards are present. Exclusion zones or overhead protection should be used in areas at particularly high risk of falling objects.
Our IOSH approvedย IOSH Working Safely Certificate covers all the essentials of health and safety in the workplace, so employees are aware of the risks and the importance of following an employerโs safe systems of work.
5. Falls from height
Out of the 138 fatal workplace injuries that occurred in Great Britain in 2023/24, 50 people died after a fall from height.
Employees using equipment such as stepladders, ladders, scaffolds and mobile elevating work platforms can suffer an injury at work due to falls from height. Fragile surfaces such as roof lights, corroded metal sheets, glass and corrugated asbestos sheet materials can lead to falls if stepped or lent on.
The Work at Height Regulations 2005 specify that someone competent must assess the risk when planning and undertaking work at height. The risk assessment should include:
- Assessing whether work at height can be avoided, for example by using drone technology for inspections.
- Taking account of weather conditions that could cause safety hazards, such as high winds and lightning.
- Assessing and visually checking the place where work at height is taking place is safe.
- Stopping objects falling from work at height or taking measures to ensure no one is injured, such as using exclusion zones and mesh on scaffolding.
- Planning for emergencies and rescue.
Providing employees with Working at Height Training supports compliance with regulations by ensuring they understand hazards and how to mitigate the risks.
6. Injuries from workplace violence
Violence and aggression in the workplace accounted for 8% of non-fatal injuries to employees in 2022/23. Injuries can result from disagreements between employees, but most incidents occur when employees are interacting with customers, the general public, or in a social care or support context.
There wereย 649,000 incidents of violence at work in 2022/23 and 41% of these incidents resulted in injuries.
Employers are required to risk assess the potential for violence and aggression and Conflict Resolution Trainingย can help employees manage challenging situations. Training can also help team leaders to manage conflict among employees.
Where incidents of violence and harassment by third parties are more likely, such as in the transport, retail, health, hospitality and leisure sectors, CCTV for monitoring incidents should be in place.
7. Exposure to noise and vibration
Exposure to noise or vibration at work can lead to hearing loss and damage to hands and arms. Exposed workers can also suffer from tinnitus which is ringing, whistling, buzzing or humming in the ears.
Harmful noise and vibration can be caused by activities such as the use of power tools and machinery or processes.
Employers should identify and assess where there are risks from noise and vibration at work and take steps to prevent or manage them, such as replacing tools, reducing exposure or using personal protection.
Our Noise Awareness Training ensures employees understand how to protect themselves from the effects of excessive noise and supports employers to comply with the Control of Noise at Work Regulations 2005.
8. Cuts and lacerations
Accidents with sharp objects such as scissors, knives and needles can lead to skin wounds. Lacerations and open woods accounted for 80 self-reported work-related injuries in 2022/23.
Employees should be trained in the correct use of such equipment, such as avoiding cutting towards themselves, storing knives in designated areas, not picking up glass with bare hands and collecting needles safely and storing in a sharps bin.
Suitable personal protective equipment, such as gloves should also be provided to avoid workplace injuries.
Final thoughts on workplace safety
Understanding what is the biggest cause of workplace injury and identifying hazards can help your organisation take preventative measures to minimise risks.
By prioritising employee safety, businesses can reduce accidents in work, improve morale, and comply with health and safety regulations.
For more information on reducing workplace accidents and improving safety standards, explore our IOSH-approved training courses tailored to a variety of industries and risks.
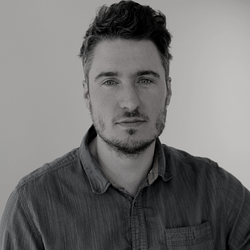
Adam Clarke
Managing Director (Consulting)