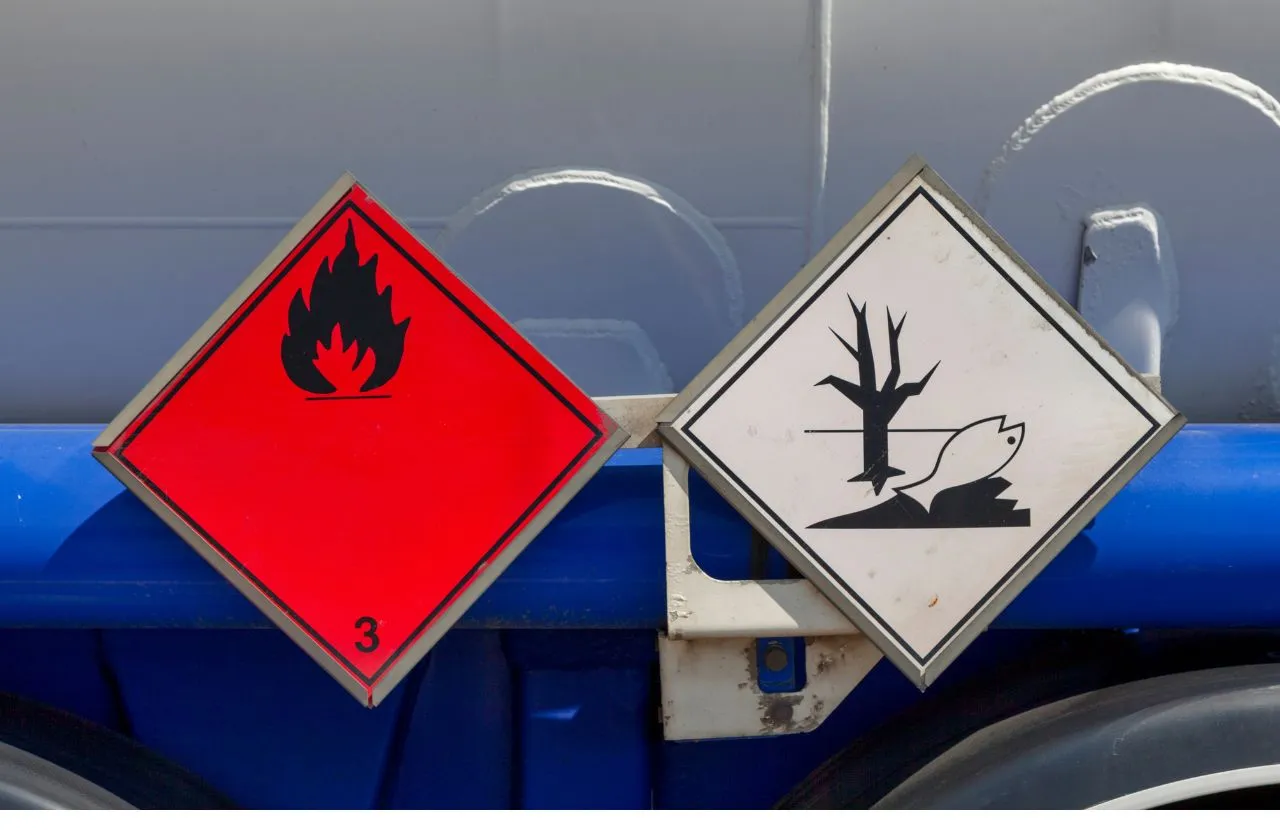
A COSHH (Control of Substances Hazardous to Health) risk assessment is required for any workplace or work site where employees are exposed to hazardous substances. A COSHH risk assessment is crucial for ensuring that hazardous substances are managed safely to protect employees and others.
In this guide we share what a COSHH risk assessment should include. However, it is important to note that every organisation is unique so there is no one-size-fits-all approach.
Identification of hazardous substances
A COSHH risk assessment should list the substances used, handled, or produced in your workplace that could be hazardous. This includes chemicals, biological agents, and any other materials posing health risks.
Inventory of substances
Start by compiling a comprehensive list of all substances that are used, handled, stored, or produced in the workplace. This should include:
- Raw materials
- Intermediate products
- Finished products
- By-products and waste materials
Remember to identify any substances that are produced as part of a process, including by-products and waste materials.
Record both the chemical names and any trade names to ensure identification is clear.
Data collection
Obtain and review Safety Data Sheets for each substance listed. These documents provide detailed information about the properties, hazards, and handling procedures for a substance.
Check the labels on containers, which can provide important hazard information, and use technical specifications and product data from manufacturers or suppliers.
Categorisation
List substances under categories:
- Chemicals – solvents, acids, alkalis, adhesives, cleaning agents, and any other chemical products.
- Biological agents – biological hazards such as bacteria, viruses, fungi, and other microorganisms.
- Dusts and fibres – hazardous dusts, such as silica dust, wood dust, and asbestos fibres.
- Gases and vapours – any potentially harmful gases and vapours that could be released during processes or from stored materials.
Processes and tasks
Identify where each substance is used, thinking about specific processes and tasks.
Note where substances are stored and how they are handled, including transport within the workplace.
Quantities and form
Record the amounts of each substance used or produced as this can affect the level of risk.
Note the physical form of each substance (solid, liquid or gas) as this impacts the type of exposure risk (inhalation, skin contact, ingestion or injection).
Potential for exposure
Assess how often and for how long employees might be exposed to each substance and identify the possible routes of entry into the body, such as inhalation, skin absorption, ingestion, or injection.
Special considerations
Consider any hazardous properties of mixtures and compounds, which might differ from their individual components.
Take into account any special conditions that might affect the hazard, such as high temperatures, pressures, or reactions with other substances.
Who might be exposed
The COSHH risk assessment should detail who may be exposed to hazardous substances in your workplace.
As well as the employees who directly handle hazardous substances, it is important to consider those working nearby who could be affected by substances. For example, office employees might be exposed to hazardous substances used in an adjacent workshop.
Also consider contractors, visitors, members of the public and all individuals who could potentially be affected.
Special attention should be given to vulnerable groups, such as pregnant women, young workers, or those with pre-existing health conditions, as they may be at higher risk from exposure and may need specific control measures for them.
To accurately identify all individuals at risk, it is advisable to talk to employees and other relevant stakeholders. Conducting surveys, interviews, and walkarounds can provide insights into how work is performed and highlight exposure points that might not be immediately obvious.
Assessment of health risks
The COSHH risk assessment should include an evaluation of the potential health risks associated with each substance.
Hazard identification
To understand the hazardous properties of each substance, refer to Safety Data Sheets (SDS) and other relevant documentation.
Key properties to consider include:
- Toxicity
- Corrosiveness
- Flammability
- Reactivity
- Carcinogenicity
Routes of exposure
Identify how a substance can enter the body, such as through:
- Inhalation: breathing in gases, vapours, dust, mist, or fumes.
- Skin contact: direct contact with the skin, which can cause irritation, burns, or absorption into the bloodstream.
- Ingestion: swallowing the substance, which might happen accidentally through contaminated hands or food.
- Injection: penetration through the skin, typically through a cut or puncture.
Handling and use
Evaluate the amount of substance used and its concentration. Higher quantities and concentrations generally increase the risk.
Consider how often and for how long people are exposed to the substance. Continuous or frequent exposure poses a greater risk than occasional exposure.
Examine the processes involving the substance to understand how it is handled, processed, or used.
Key questions include:
- Are substances used in open or closed systems?
- Are there any processes that generate dust, fumes, or vapours?
- Are there tasks that involve manual handling or direct contact with the substance?
Health effects
Evaluate the following:
- Acute effects. Consider immediate health effects from short-term exposure, such as burns, irritation, dizziness, or respiratory problems.
- Chronic effects. Assess long-term health effects from prolonged exposure, including diseases such as asthma, dermatitis, cancer, or organ damage.
- Sensitivity and vulnerability. Consider if certain individuals might be more susceptible to harm, such as those with pre-existing health conditions, allergies, or pregnancy.

Exposure scenarios
Consider exposure risks during routine operations and typical conditions, but also consider risks during non-routine activities such as maintenance, cleaning, or emergency situations.
Risk rating
Rate the likelihood of exposure occurring based on how substances are used and the control measures in place. Then rate the severity of potential health effects if exposure occurs.
Use a risk matrix to combine likelihood and severity ratings to determine the overall risk level (for example, low, medium or high). This helps prioritise which substances and activities need more stringent controls.
To find out how to calculate risks, please read our article, How to write a risk assessment.
Control measures
Review the current control measures in place to determine if they are adequate and effective in reducing exposure to safe levels.
Identify any additional controls or improvements needed to further reduce risks. This might include engineering controls (like ventilation systems), administrative controls (like safe work procedures), personal protective equipment (PPE), and safe storage practices. We discuss these controls in more detail further down.
Hierarchy of controls
The risks associated with a substance should be eliminated altogether if possible. If elimination is not possible then the next step is substitution, followed by engineering controls, working down the hierarchy of control measures as needed.
This is the hierarchy of control measures:
- Elimination: completely remove the hazardous substance from the process.
- Substitution: replace the hazardous substance with a less hazardous one.
- Engineering controls: implement physical changes to the workplace to reduce exposure.
- Administrative controls: change the way people work to reduce exposure.
- Personal protective equipment (PPE): use protective clothing and equipment as the last line of defence. It is important to specify exactly what PPE is required, for example, ‘chemical resistant gloves’ rather than ‘gloves’.
Engineering controls
This part of the risk assessment explains how a hazardous substance will be contained and prevented from escaping.
Engineering controls include:
- Ventilation to dilute airborne contaminants.
- LEV systems to capture contaminants at the source to prevent them from spreading.
- Closed systems for processes involving hazardous substances to prevent release into the workplace.
- Physical barriers or enclosures around hazardous processes or equipment.
- Automating processes to reduce the need for manual handling of hazardous substances.
It is a legal requirement under COSHH Regulation 9 to regularly maintain safety equipment and control systems to ensure they are functioning effectively.
Safe storage practices
The COSHH risk assessment should document how hazardous substances are stored in appropriate conditions, considering factors such as temperature, humidity, and ventilation. Incompatible substances must be stored separately to prevent dangerous reactions.
The risk assessment should be clear that:
- All containers are clearly labelled.
- An inventory of hazardous substances is kept up to date.
- There are spill containment measures in place, such as bunding and drip trays to contain spills and leaks and employees are aware of emergency procedures.
Administrative controls
Administrative controls aim to ensure that all employees are aware of the risks of hazardous substances and the importance of following best practices to mitigate these risks.
Your organisation’s COSHH risk assessment should detail the following administrative controls:
- Safe work procedures
- Training and information
- Personal protective equipment (PPE)
- Monitoring and supervision.
Let’s look at these areas in more detail:
Safe work procedures
Employers must ensure there are safe working procedures in place by developing and implementing standard operating procedures (SOPs) for handling, using and disposing of hazardous substances.
Tasks should be rotated to limit the time that someone is exposed to a hazardous substance.
Training and information
COSHH training for employees helps to ensure they understand the risks associated with hazardous substances, how to mitigate risks, their personal responsibilities and their employer’s responsibilities to keep them safe, and what to do in an emergency.
Employees must be made aware of the hazardous substances specific to their workplace. There must be clear labels and signs to identify hazardous substances and areas where they are used.
Personal protective equipment (PPE)
Appropriate PPE must be provided for employees based on the type of hazard and the level of exposure. This may include respiratory protection (masks, respirators and breathing apparatus), skin protection (gloves, aprons and full-body suits), eye protection (safety goggles and face shields) and hearing protection (earplugs or earmuffs for noise hazards).
Train employees on the correct use (this is especially important with respiratory protection), maintenance, and limitations of PPE and ensure that PPE is regularly inspected, maintained and replaced to ensure its effectiveness.
Employers have a responsibility under the Personal Protective Equipment (PPE) at Work Regulations 2002 to ensure employees have sufficient information, instruction and training on the use of PPE.
At Praxis42, we offer PPE Awareness training to ensure employees are aware of the function of different types of PPE equipment and their personal health and safety responsibilities.
Monitoring and supervision
Regularly monitor the levels of hazardous substances in the workplace, and conduct health surveillance for employees exposed to certain hazardous substances.
Review your COSHH risk assessment
Regular reviews of COSHH risk assessments help to ensure control measures remain continuously effective in mitigating risks.
A review involves assessing the current control measures, identifying any changes in the work environment or processes, and determining if the measures continue to provide adequate protection.
Reviews should be scheduled periodically and also triggered by significant changes in operations, incidents, or new information regarding the substances in use.
COSHH risk assessment template
The Health and Safety Executive (HSE) has compiled example COSHH assessment examples for different industries. These sample risk assessments are useful for small businesses with few employees.
On the HSE website you can also find COSHH risk assessment templates to help you identify the actions you need to take to control risks associated with hazardous substances.
Do you need a COSHH risk assessment?
Our health and safety consultants have extensive experience carrying out and reviewing COSHH risk assessments for organisations of all sizes across every sector.
We produce a comprehensive COSHH risk assessment for you which is a clear, structured record of our findings. It includes the identified hazards, overall risk factors and the recommended control measures.
By partnering with us you are not just meeting your legal obligations, you are investing in the safety and wellbeing of your workforce and the sustainability of your organisation.
Find out more about our COSHH risk assessment service by visiting our website. Alternatively, contact our friendly team to discuss your requirements on 0203 011 4242 or info@praxis42.com