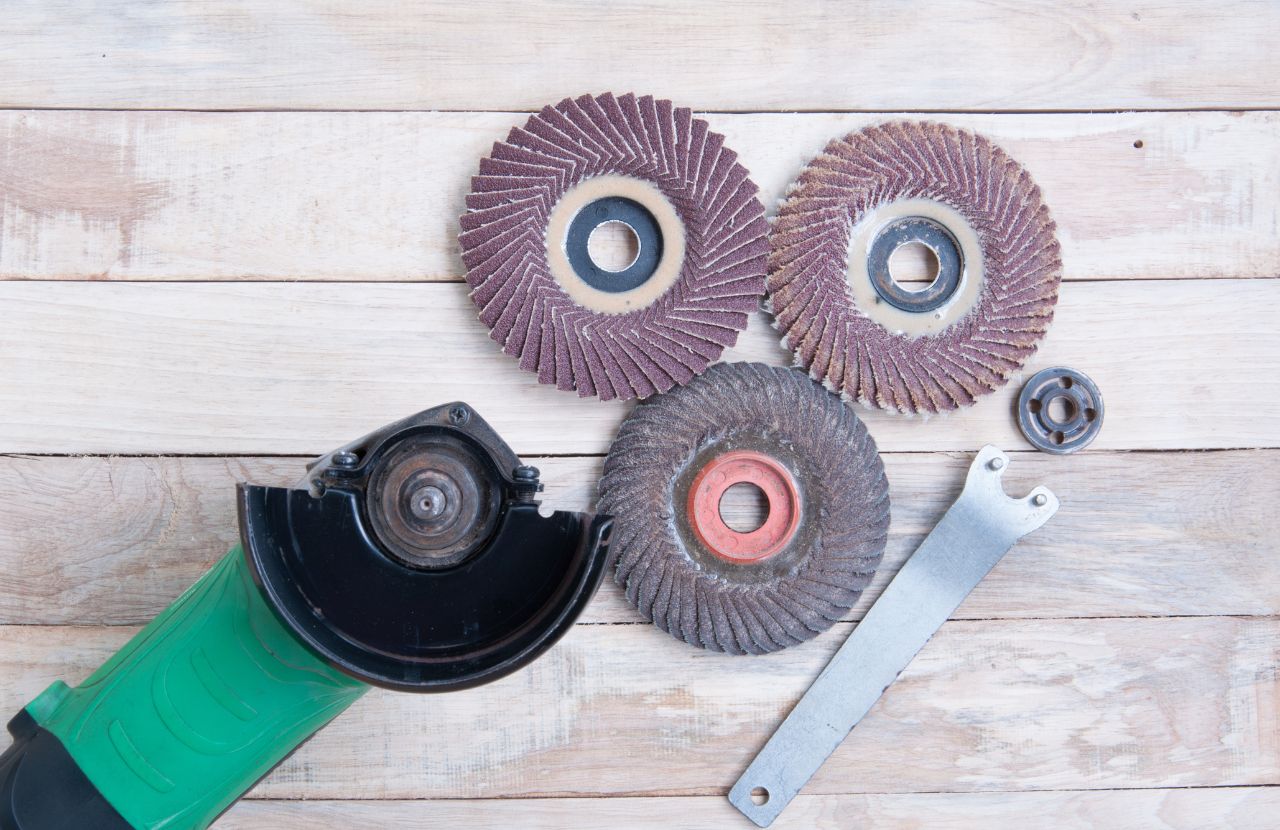
Serious injuries including eyesight loss, amputations, friction burns, lacerations, trapped fingers and entangled limbs can happen when someone is using abrasive wheels. In this guide to abrasive wheels safety, we talk about legal responsibilities, the hazards associated with abrasive wheels, how to mitigate risks and best practices to follow.
What is an abrasive wheel?
The HSE defines an abrasive wheel as ‘a wheel consisting of abrasive particles bonded together with various substances.’
Abrasive wheels are used across a broad range of industries including agriculture, automotive repair and maintenance, building, construction, glass production and manufacturing. They are used for cutting, grinding, polishing, finishing, shaping, and repairing materials.
Examples of abrasive wheels include angle grinders, belt sanders, bench grinders and grinding machines. Each machine is tailored to specific tasks and materials.
What is the most common cause of abrasive wheels accidents?
Most accidents involving abrasive wheels are caused by operator error or unsafe systems of work.
Abrasive wheels hazards include:
Explosions
Damaged, incorrectly mounted or clogged abrasive wheels can explode. Explosions can also be caused by running a wheel too fast or improper use.
Regularly inspect abrasive wheels for damage or clogging and replace them when necessary, if competent and authorised to do so. Ensure they are mounted correctly, following the manufacturer’s instructions and the training provided. Control the wheel speed within safe limits to prevent overheating.
Flying debris
When materials are cut or ground, abrasive materials and sparks can cause injuries and fires.
Provide appropriate barriers or screens to contain flying debris during cutting or grinding operations and away from flammable materials. Make sure operators wear suitable eye and face protection, such as safety goggles and face shields to protect against debris and sparks.
Missing or damaged guards
Cracked, bent and worn guards offer ineffective protection from a rotating wheel.
Conduct daily inspections to make sure guards are intact. Replace damaged guards immediately to maintain effective protection.
Incorrect use
When abrasive wheels are used for an activity that was not intended by the manufacturer or the safe system of work injuries can occur. Operators must be trained and competent, so they understand the importance of only using equipment for its intended purpose.
Fire
If the environment around an abrasive wheel is not clear of flammable materials, sparks from abrasive wheels can cause materials to ignite. Therefore abrasive wheels should be subject to a risk assessment before use.
Maintain a clear area around the work activity and identify the risks. Where the risk assessment identifies the requirement, ensure there is an appropriate fire extinguisher readily available, employees are trained to use firefighting equipment and that they have undergone fire safety training.
Vibration
If a wheel is the incorrect weight or size, or bearings are loose, this can cause vibrations that may lead to hand-arm vibration syndrome (HAVS).
Regularly inspect abrasive wheels to address imbalances or loose bearings that can cause excessive vibrations. Provide anti-vibration tools and equipment, where appropriate, to reduce the risk of HAVS.
Dust and fumes
Depending on the materials used, inhalation of dust and fumes can lead to respiratory illnesses and lung diseases.
Implement dust and fume extraction systems where necessary to control the inhalation of hazardous particles and fumes. Provide operators with appropriate respiratory protective equipment (RPE).
Noise
Extreme noise levels from abrasive wheels can cause damage to the ears and hearing loss.
Implement noise control measures based on a risk assessment, which could include noise barriers and hearing protection. Provide employees with regular hearing assessments to ensure that controls are effective.
Improper lifting techniques
Lifting awkward or heavy equipment without using proper techniques can lead to musculoskeletal disorders.
Provide employees manual handling training to prevent musculoskeletal disorders (MSDs). Provide lifting aids and equipment such as cranes or hoists for heavy or awkward loads.
Does PUWER cover abrasive wheels?
The Provision of Work Equipment Regulations (PUWER) covers all equipment used in the workplace, including abrasive wheels.
PUWER regulations apply to every workplace, irrespective of size or industry. The purpose of the regulations is to safeguard workers and anyone else who may be affected by work equipment and machinery.
Compliance with PUWER is essential to create a safe workplace, preventing accidents related to abrasive wheels and other machinery.
What are an employer’s responsibilities under PUWER?
These are an employer’s key responsibilities under PUWER:
Regular inspection and maintenance
Employers are obligated to make sure all work equipment is regularly inspected and maintained to keep it in safe working condition. This involves a rigorous maintenance and inspection schedule and addressing hazards promptly. Employees should be encouraged to report any signs of wear and tear immediately.
Training and competence
Employers must ensure that people who operate work equipment are adequately trained and competent to use the equipment safely.
It is vital that employees are provided with clear and accessible information and instruction regarding the safe use of work equipment. This includes user manuals, safety guidelines, training materials and supervision when necessary.
Intended use
Work equipment must be used only for the purposes intended by the manufacturer. Employers should emphasise the importance of using equipment in accordance with the manufacturer’s instructions and specifications.
Safe environment
Employers are responsible for creating and maintaining a safe and organised work environment. This means ensuring appropriate health and safety measures are in place, such as safety guards, personal protective equipment (PPE), and clear warning signage.
Adequate ventilation, lighting and workplace design should be considered to minimise risks.
Risk assessments
Conducting machinery risk assessments is crucial. Employers must identify and assess potential risks associated with the use of work equipment and implement measures to control and mitigate those risks.
Employers must maintain records of equipment inspections, maintenance, and training. These documents are a tools for ensuring safety procedures are followed and inspections are carried out routinely. Documents also help demonstrate compliance with PUWER.
Emergency procedures
Employees must be aware of and trained in emergency procedures related to work equipment, including how to respond if there is an accident or equipment malfunctions.
Review and improvement
It is vital that employers regularly review and assess the effectiveness of safety measures, accident and near miss reports and investigations and make improvements as needed to enhance workplace safety.
What are an employee’s health and safety responsibilities?
Employees bear no responsibility under PUWER regulations. However, they do have health and safety responsibilities under the Health and Safety at Work Act 1974.
Employees are responsible for:
- Taking reasonable care of their own health and safety at work. This includes being cautious and responsible in their actions to prevent harm to themselves and others who may be affected by their work activities.
- Cooperating with the health and safety procedures and practices put in place by their employer. This involves following safety guidelines, using provided personal protective equipment (PPE), and adhering to safety protocols and rules.
- Reporting any hazards, unsafe conditions, or potential risks they notice. Employees have a duty to report issues to their employer or supervisor promptly.
- Actively engaging in any health and safety training provided by their employer and make every effort to understand and follow safety instructions and guidance.
- Using safety equipment and protective measures provided by their employer correctly and consistently. This includes wearing appropriate PPE and using safety devices on machinery or equipment, as required.
- Refusing to carry out unsafe work. If an employee believes a task or work condition is unsafe and could pose a serious risk to their health and safety, they have the right to refuse to perform that work until the issue is resolved.
What else can employers do to mitigate risks associated with abrasive wheels?
To further reduce the risks of abrasive wheels, employers should ensure:
- Installation of abrasive wheels is only carried out by personnel that are competent and provided with the correct training and expertise. Incorrect installation increases the risk of injuries.
- Equipment is stored correctly and in accordance with the manufacturer’s instructions. Temperature fluctuations should be considered as extreme temperatures or humid conditions may damage equipment, making it unsafe to use.
- Wheel labels and markings are readable and accurate. It is important that the manufacturer’s instructions are always legible and expiry dates are adhered to.
- Abrasive wheels are used in the right environmental conditions. Extreme temperatures or humidity may impact the integrity of an abrasive wheel.
The HSE’s Safety in the use of abrasive wheels is guidance on abrasive wheels safety which advises on the precautions to take to prevent injury and illness.
What should an operator do before using an abrasive wheel tool?
Before using abrasive wheels, equipment operators should follow essential steps, such as:
- Carrying out a visual inspection of the abrasive wheel to make sure there is no visible damage, such as cracks, chips or signs of wear or any loose or damaged parts. If any damage is detected this must be reported to the employer or supervisor immediately, and the wheel should not be used until it is repaired or replaced.
- Wearing the appropriate personal protective equipment (PPE). This may be goggles, a face shield, RPE, hearing protection or gloves.
- Making sure safety guards are in place and securely attached to the equipment. These guards are designed to protect operators from potential contact with the rotating wheel and should never be removed during operation.
- Clearing the work area of any unnecessary objects, materials or obstructions that could interfere with the operation or cause accidents.
- Carrying out a wheel test run. Before starting a job, run the abrasive wheel for a minute without any load. This test helps ensure the wheel is running smoothly and correctly. Be aware the wheel may become hot during the test.
- Ensuring the workpiece is securely clamped or held in place to prevent movement or slippage during the operation. This helps maintain stability and accuracy while using the abrasive wheel.
When machinery is in use, employees must adhere to abrasive wheels safety practices, including maintaining a proper stance, keeping hands and clothing away from the wheel and avoiding distractions while operating the equipment.
Can abrasive wheels safety training be done online?
Developed by experienced health and safety consultants, our Abrasive Wheels Awareness – online training provides operators and supervisors with the awareness required to use abrasive wheels safely.
Practical training is also essential, so operators and supervisors thoroughly understand how to set up and use abrasive wheels in their specific work environment.
Combining online learning with hands-on training helps embed essential knowledge and skills, ensuring employees can operate abrasive wheels safely and effectively and the employer to ensure competence.
How often do you need to do abrasive wheel training?
Abrasive wheels safety awareness is essential to prevent serious accidents, ill health and injuries in the workplace.
We recommend that employees retake our Abrasive Wheels Awareness course annually to ensure knowledge is retained and safe working practices are consistently maintained.
Abrasive wheels training is a vital investment in the safety culture of a workplace, and the most effective means of preventing serious accidents and injuries.