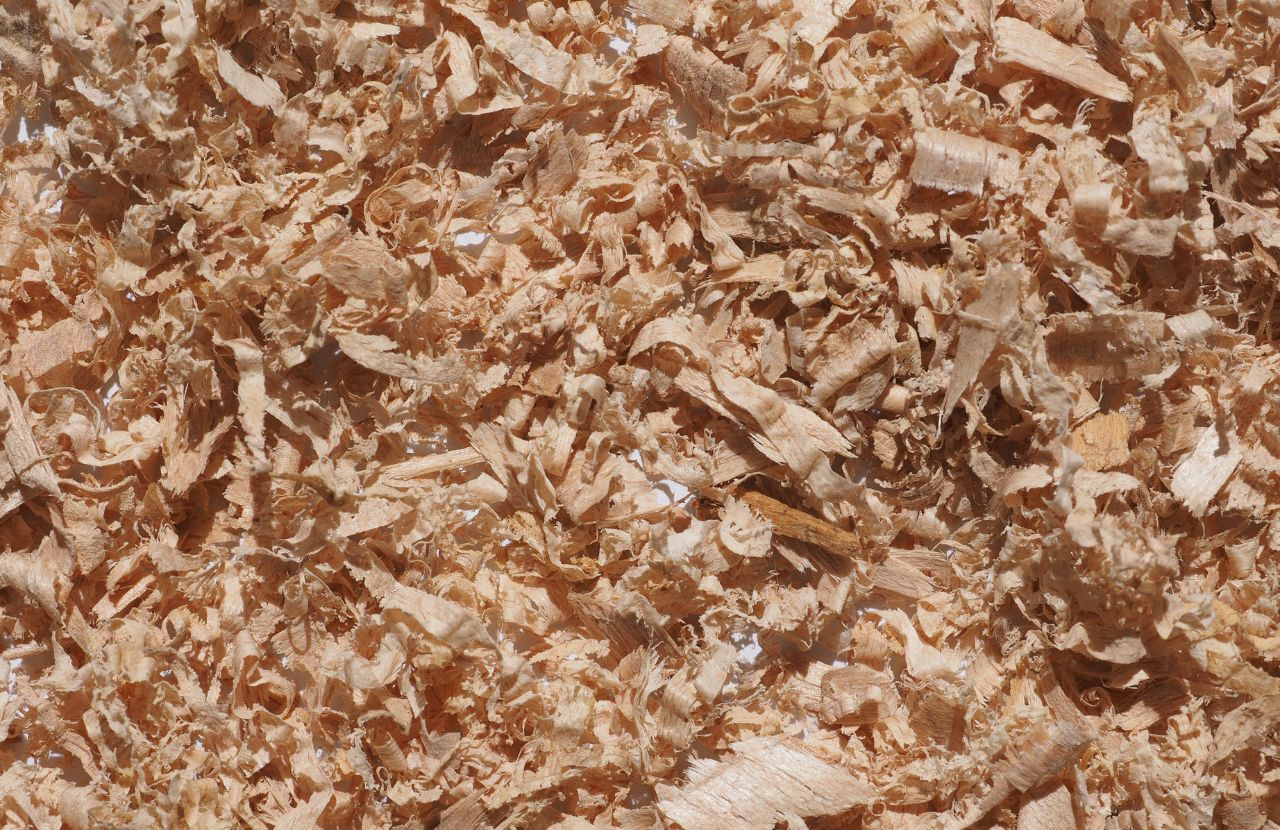
In February 2024, Turners and Moore in Norwich were fined ยฃ40,000, and the company director received a four-month suspended sentence due to employees’ exposure to harmful levels of wood dust. This highlights the importance of understanding how much exposure to wood dust is dangerous, an employer’s legal responsibilities, and practical safety measures to protect employees and organisations.
What are the health risks of wood dust?
Cancer
Exposure to wood dust over a long period of time has been linked to an increased risk of nasal and sinus cancer.
Respiratory illnesses
Carpenters and joiners are four times more likely to develop asthma than those in other professions.
Wood dust exposure can also cause allergic reactions such as rhinitis and dermatitis. Long-term exposure increases the risk of developing chronic obstructive pulmonary disease (COPD) and, although rare, can lead to pulmonary fibrosis (scarring of lung tissue), impairing lung function.
Skin and eye irritation
Wood dust can cause skin irritation and dermatitis. It can also irritate the eyes, sometimes causing conjunctivitis.
Activities with high wood dust exposure
- Sanding, sawing, and planing wood.
- Using wood routers.
- Carving, turning, shaping, or milling wood.
- Drilling and cutting wood.
- Cleaning up wood dust.
- Industrial wood processing.
- Home improvement or hobby projects.
Employerโs legal responsibilities and COSHH regulations
Under the Control of Substances Hazardous to Health (COSHH) Regulations 2002 employers have a legal duty to ensure that their employees are not exposed to dangerous levels of wood dust.
Workplace exposure limits (WELs)
The WEL for hardwood dust is 3mg/mยณ over an 8-hour period, and for softwood dust, it is 5mg/mยณ over the same period. Hardwood dust is more hazardous, hence the stricter limit.
See the Health and Safety Executiveโs webpage on wood dust for more information on wood dust exposure limits.
Local exhaust ventilation (LEV) systems
LEV systems must be installed at woodworking machines to capture dust at its source. These systems must be maintained by a competent person at least every 14 months.
Health surveillance
Employers must provide health surveillance to detect early signs of health issues and ensure the effectiveness of protection measures.
Monitoring and reducing wood dust
Monitoring wood dust
- Personal monitoring: involves measuring individual employees’ wood dust exposure using personal sampling pumps.
- Area monitoring: measures dust concentration in specific areas or throughout the workplace using stationary devices.
Reducing wood dust in the air
Here are some ways to reduce the amount of wood dust in the air:
- Substitution: Use materials that generate less dust, such as pre-cut wood.
- Wet methods: Dampening wood before cutting or sanding reduces airborne dust.
- Work techniques: Use sharp blades and hand tools to ensure less dust is produced.
- Wood dust extraction and air filtration systems: Wood dust extractors are essential for removing wood dust from the air and LEV systems are a legal requirement (see above).
- Enclosures and barriers: Contain wood dust to prevent its spread.
- Work area design: Design work areas to minimise dust accumulation and facilitate easier cleaning. For example, keep work areas uncluttered and ensure workbenches and floors have smooth non-porous surfaces to make saw dust cleaning easier.
- Housekeeping: Clean regularly with vacuum cleaners equipped with HEPA filters.
Protecting employees
Health monitoring
It is a legal requirement under COSHH to monitor the health of employees who are exposed to wood dust (see above).
Safety training
Conduct training sessions on wood dust hazards, safe work practices, proper use of PPE, and emergency procedures. Ensure employees understand emergency and first aid procedures.
Ensure employees are trained to use woodworking machinery safely and those maintaining dust extraction systems have the necessary expertise.
Personal Protective Equipment (PPE)
Provide respirators, safety goggles, gloves and appropriate clothing to protect against wood dust exposure. Respirators must comply with safety standards like FFP2, FFP3, or N95.
Make sure employees protect their skin from wood dust exposure by wearing long sleeves and long trousers.
Communication and reporting
Establish easy reporting systems for employees to report issues with wood dust extraction systems, PPE, or dust accumulation. Implement feedback mechanisms for improving dust control measures.
Final thoughts
The severe consequences of failing to protect employees from wood dust exposure, as seen in the case of Turners and Moore, underscores the importance of understanding how much exposure to wood dust is dangerous and how to minimise it.
By adhering to COSHH regulations and implementing effective control measures, employers can create a safer working environment and comply with regulatory standards.