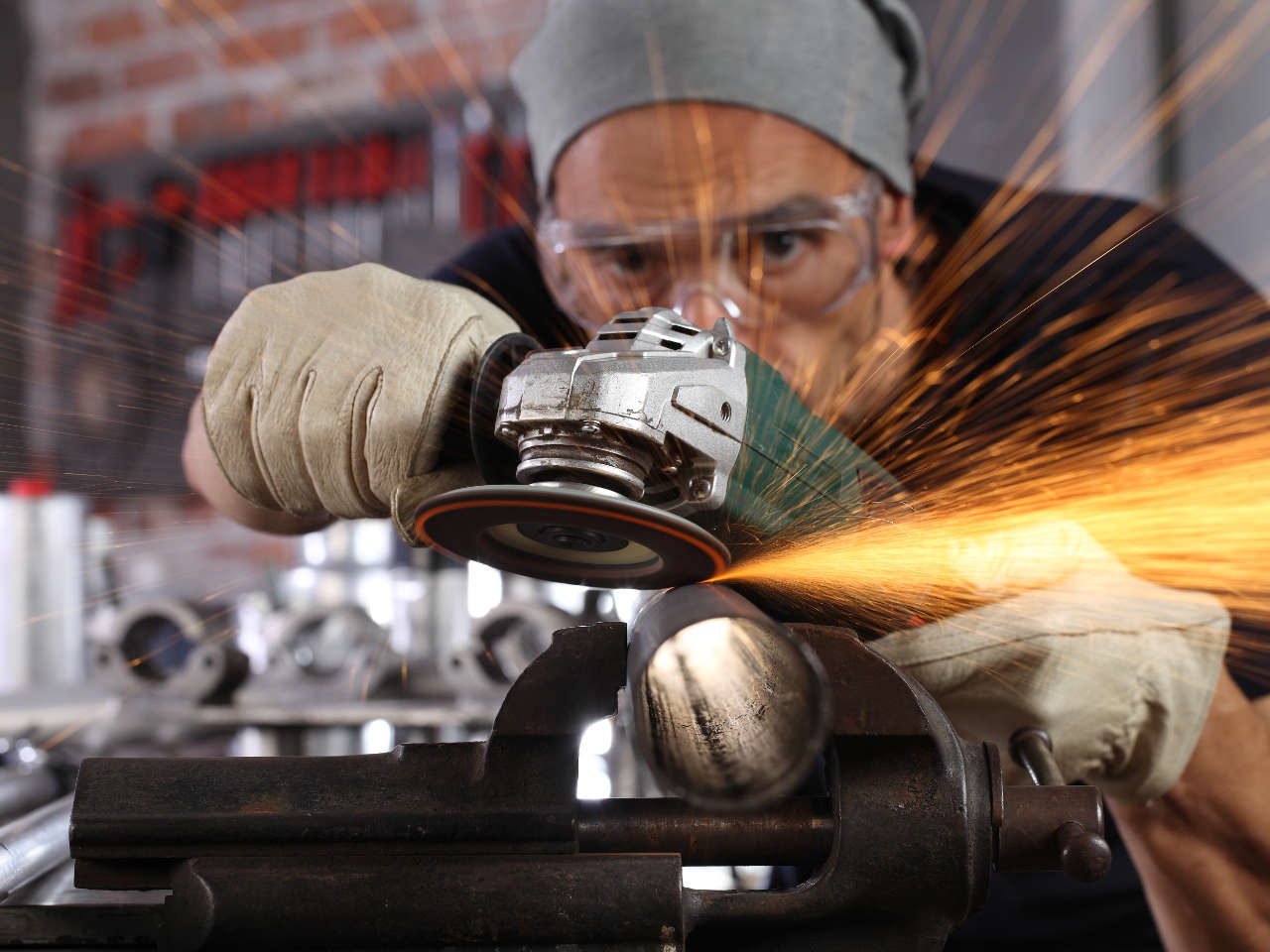
The safety of equipment and machinery at work is regulated in the UK by the Provision and Use of Work Equipment Regulations (PUWER) 1998.
In 2022/23, 138 people were killed and 561,000 suffered a non-fatal injury at work. Of the fatalities, 8% were due to contact with moving machinery. These figures highlight the vital importance of ensuring equipment and machinery is safe and that safety procedures are followed to minimise any health risks.
This guide explains what PUWER is, the obligations it places on employers, and the steps organisations must take to comply with these regulations.
What does PUWER stand for?
PUWER stands for the Provision and Use of Work Equipment Regulations. It sets out the responsibilities for those who own, operate, or control equipment and machinery in the workplace to ensure they are safe for use.
Originally introduced in 1992, the regulations were updated in 1998 and are a key part of health and safety legislation in the UK.
What are the PUWER regulations?
PUWER regulations exist to safeguard anyone who comes into contact with workplace machinery and equipment. This includes employees, self-employed individuals, and anyone else who might be affected by the equipment.
All workplace settings in Great Britain where equipment is used are covered by the regulations. PUWER also extends to specified offshore areas and activities.
As well as offices, factories and shops, workplaces covered include schools, colleges, universities, hospitals, entertainment venues, hotels and offshore oil and gas installations.
All employees must follow health and safety regulations, including reporting safety issues to their employer and using equipment in accordance with any PUWER training and instructions they have received.
Key points of the PUWER regulations include:
- Suitability. Equipment must be suitable for its intended purpose and conditions.
- Maintenance. Equipment must be maintained in a safe condition to prevent risks to health and safety.
- Inspections. Regular inspections are required to ensure equipment remains safe for use. Inspections must be conducted by a competent person with the necessary skills and experience.
- Training. Only individuals who have received adequate instruction and training, such as electrical safety training, should operate equipment.
What is covered by PUWER?
PUWER applies to all workplace equipment, including machinery, appliances, tools, and installations. It covers a range of industries and environments, such as:
- Manufacturing and industrial sites
- Construction and building sites
- Retail and hospitality venues
- Educational institutions
- Healthcare facilities
- Offshore oil and gas installations.
If employees are required to use equipment at home for work purposes, PUWER regulations apply.
The PUWER regulations do not apply to equipment used by the public such as compressed air equipment in petrol stations. Those circumstances are covered by the Health and Safety at Work Act 1974.
For a list of equipment covered by PUWER, please see our article, What equipment is covered by PUWER regulations?
As well as PUWER, other regulations apply to some equipment. For example, LOLER (see below). Personal protective equipment is covered by Personal Protective Equipment at Work Regulations 1992.
What is a PUWER inspection?
A PUWER inspection involves a thorough assessment of work equipment to ensure it is safe to use and complies with the regulations.
Depending on the type of equipment and the frequency of its use, a PUWER inspection could be a basic visual examination or a detailed inspection that involves dismantling the equipment according to the manufacturer’s instructions. Simple hand tools should be repaired or replaced if needed.
Inspections should cover:
- Condition and maintenance of equipment
- Appropriate safety measures such as emergency stop systems and safety guards
- Proper functioning of warning devices
- The use of personal protective equipment (PPE)
- Ensuring electrical installations are safe
A record of all inspections must be kept, and depending on the type and use of equipment, these may need to be conducted daily, weekly, or at other regular intervals.
How to comply with PUWER
To comply with PUWER, organisations must:
- Ensure equipment is suitable. Equipment should be appropriate for the tasks it is used for and the environment in which it is operated.
- Conduct regular inspections. Implement a routine inspection schedule conducted by competent individuals.
- Maintain safe working conditions. Regularly service and repair equipment to keep it in a safe operating condition.
- Provide adequate training. Ensure all personnel operating equipment are adequately trained and aware of safety procedures.
Appropriate health and safety measures must be followed when machinery is being used. This might include emergency stop systems, warning devices, personal protective equipment, visible safety markings and isolation from sources of electricity that could harm the user. A suitable and sufficient risk assessment should be undertaken to determine these measures.
The regulations have specific requirements for mobile work equipment and power presses.
For mobile work equipment used for carrying people, such as fork-lift trucks and dumper trucks, checks must be made to ensure that it is suitable for this purpose. Measures should be taken to reduce risks such as preventing it from rolling over.
Power presses and associated guards or protection devices should be examined in detail at regular intervals and inspected daily by a competent person.
PUWER and other regulations: what is the difference between PUWER and LOLER?
While PUWER covers general workplace equipment safety, the Lifting Operations and Lifting Equipment Regulations (LOLER) 1998 specifically address the safety of lifting equipment.
Both sets of regulations may apply in workplaces where lifting equipment, such as cranes or forklifts, is used.
How is PUWER enforced?
If a health and safety inspector believes a workplace is not following PUWER regulations, they can issue an improvement or prohibition notice on the equipment.
An improvement notice is given if equipment or machinery is deemed to be poorly maintained or damaged, or it has not received adequate inspections and risk assessments. The owner or controller of the equipment will be given a minimum 21 days to comply with the notice.
If the improvement notice is not dealt with, a prohibition notice could be issued. This means that the equipment cannot be used until the concerns of the inspector have been dealt with. Such an action could lead to increased costs for businesses because key equipment is out of action, or worse if the organisation is prosecuted.
PUWER training
Ensuring work equipment is used and maintained safely is essential for protecting employees and maintaining smooth business operations. Understanding what PUWER is and how the regulations apply to your workplace helps create a safer and more compliant working environment.
Our IOSH Approved, CPD Certified PUWER training is designed for those responsible for selecting, using, or maintaining work equipment. It is suitable for managers, supervisors, and employees across a broad range of industries.
Find out more about PUWER training on our website, or contact our friendly team today on 0203 011 4242/info@praxis42.com
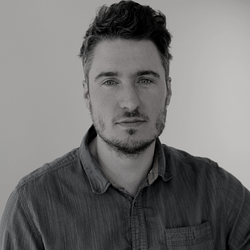
Adam Clarke
Managing Director (Consulting)