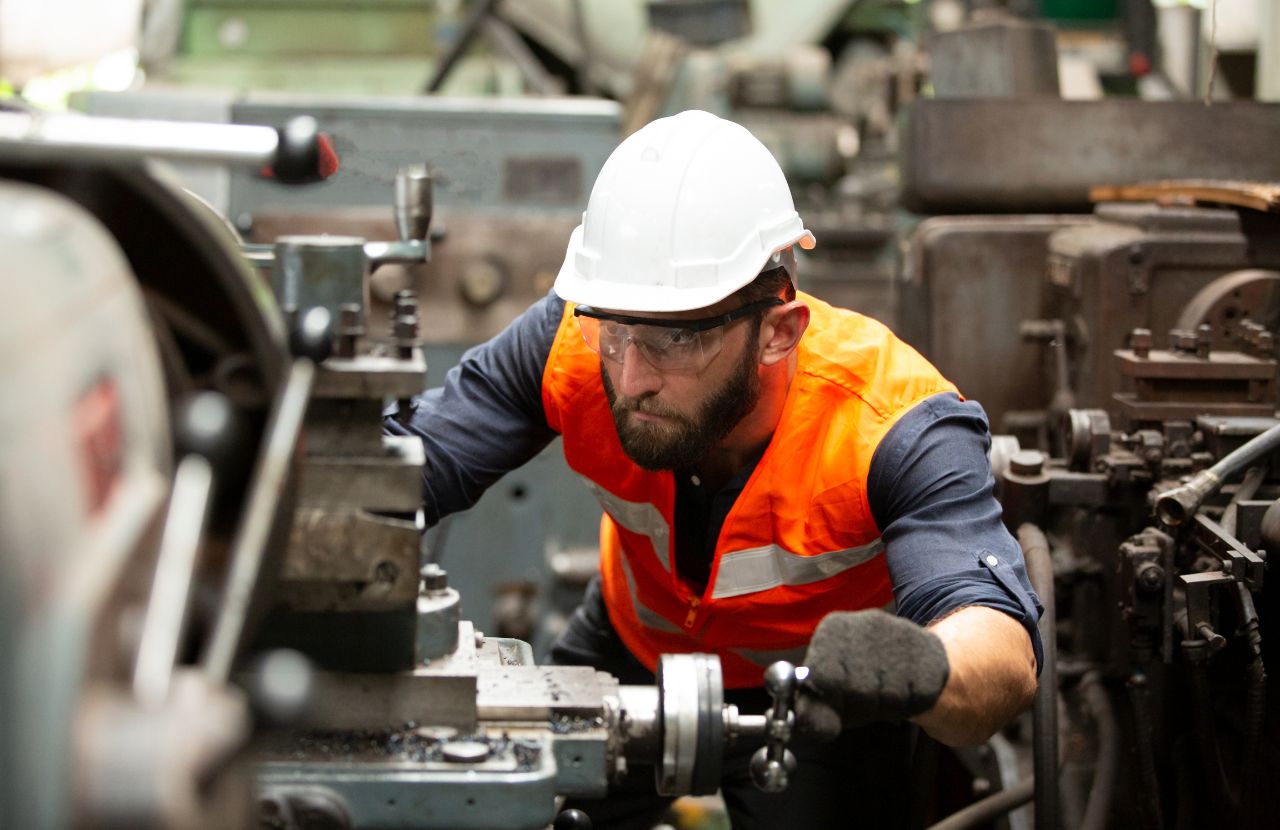
Machinery risk assessments help employers to protect workers and comply with legislation. Employers are responsible for reducing or eliminating the health and safety risks associated with equipment in the workplace.
In this guide we delve into what the law and guidance requires and means for you, what a machinery risk assessment involves and the principles behind it.
What machinery safety laws apply to employers?
The Provision and Use of Work Equipment Regulations (PUWER) sets out the legal requirements for the safe use of work equipment. It mandates that work equipment must be suitable for its intended purpose, maintained in a safe condition and only used by trained and authorised personnel.
PUWER also requires employers to conduct a risk assessment of machinery and provide information, instruction, and training to those using equipment.
Lifting Operations and Lifting Equipment (LOLER) is legislation that focuses on the safe use of lifting equipment including cranes, hoists and lifting accessories. It requires that lifting equipment is maintained, assessed, inspected and tested by competent persons at regular intervals. Employers are responsible for promptly rectifying defects and making sure operatives are competent and fully trained.
While the Supply of Machinery (Safety) Regulations 2008 are still in place it is important for employers to stay up to date with the law as regulations are subject to change. From January 2025, it will be a legal requirement that new machines are UKCA or CE marked and come with a Declaration of Conformity Instructions written in English.
What heavy machines require risk assessments?
A wide range of heavy plant and equipment requires a risk assessment:
- Agricultural machinery.
- Conveyor systems.
- Cranes.
- Excavators and earthmoving equipment.
- Forklift trucks.
- Industrial presses.
- Metalworking machinery.
- Mining equipment.
- Power tools.
- Woodworking machinery.
Depending on the machine, a risk assessment might cover safe working loads (SWL), load stability, operator training, layout of the workspace, stability of the ground, machine guarding of dangerous parts, emergency stop mechanisms, use of PPE, entanglement hazards, vehicle maintenance and much more.
What equipment is covered by PUWER?
Puwer regulations don’t just cover machinery, but all work equipment. This includes air conditioning units, computers, hand tools, ladders and lifts.
In short, any equipment used at work that could be a risk to people’s health and safety is covered in the regulations and should be subject to a risk assessment by someone competent.
Who is responsible under PUWER?
Under PUWER regulations, the following people are responsible for ensuring machinery safety:
Employers
An employer’s duty includes:
- Providing suitable work equipment that is safe for its intended use.
- Ensuring work equipment is properly maintained, inspected and tested to reduce or eliminate risks.
- Providing information, training and supervision to employees to ensure safety on machinery.
- Conducting machinery risk assessments and taking measures to reduce or eliminate risks associated with work equipment.
Self-employed people
Self-employed people are also subject to PUWER regulations.
People in charge of equipment
This category may include managers, supervisors, or individuals responsible for overseeing the use of equipment in the workplace.
Their duties are:
- Ensuring employees use work equipment safely and in accordance with established procedures and training.
- Coordinating regular inspections and maintaining equipment.
- Taking corrective actions to address identified risks and hazards.
- Providing information, guidance and training to the workers under their supervision.
What are common work equipment hazards?
The main hazards associated with work equipment are:
- Entanglement. This occurs when a person or their clothing becomes caught in moving parts of a machine. It can lead to severe injuries such as limb amputations or strangulation.
- Impact. Impact hazards are when someone is struck by moving parts, falling objects or equipment. This can result in injuries ranging from bruises and major injuries like fractures to more severe trauma.
- Contact. Contact hazards involve physical contact between a person and a moving part, sharp edge, or hot surface of a machine. It can lead to cuts, burns and other injuries.
- Entrapment. Entrapment hazards happen when a person becomes trapped or confined by a piece of machinery. This may occur when safety guards are not in place or if someone is inappropriately positioned when machinery is in operation.
- Ejection. Ejection hazards refer to the risk of materials, tools or objects being forcefully ejected from machines, potentially striking people nearby.
Examples of mechanical hazards
Mechanical hazards are the parts of a machine that can harm a worker, for example:
- Rotating parts.
- In running nips.
- Sliding parts.
- Areas where a machine cuts, shapes, or bores into something.
- Pinch and shear points where someone can be caught between a stationary and moving part.
There may be non-mechanical hazards when a machine is running, such as dust, sparks, chips or sprays flying from the machine.
How can you reduce or eliminate machinery hazards?
- Substitute the machine with safer equipment, if feasible.
- Relocate the machine to an area where people will not be exposed to the hazard.
- Enclose dangerous parts of the machine to make them inaccessible.
- Install guards to prevent people getting too close to machine parts.
- Use barriers to restrict access to hazardous areas.
- Ensure equipment is only used for its intended purpose.
- Maintain a safe environment around the machine (no spillages, clutter etc.)
- Provide operators and maintenance personnel with thorough instruction and training.
- Enforce safety rules, such as not wearing jewellery or loose clothing near equipment.
- Require the use of personal protective equipment (PPE).
- Establish a regular maintenance schedule.
- Conduct regular worker and equipment inspections and tests.
What are the stages of a machinery risk assessment?
The Health and Safety Executive (HSE) recommends following a systematic approach to machinery risk assessments:
1. Identify potential hazards
Start by identifying all potential hazards associated with the machine. This includes examining the machine’s components, operations and any substances used.
Consider all aspects of the machine’s lifecycle, including installation, operation, maintenance, and decommissioning, and follow the manufacturer’s instructions and safety information.
2. Identify who might be harmed and how
Determine who could be exposed to the identified hazards, for instance workers, maintenance personnel, and any anyone else in the vicinity of the machine. Think about physical injuries, exposure to hazardous substances, or ergonomic issues.
3. Evaluate the risks and decide on precautions
Assess the likelihood and severity of the identified risks. This involves considering the probability of an incident occurring and the potential consequences. Prioritise tasks by focussing on the most severe and likely risks first.
Decide appropriate precautions and control measures to eliminate or reduce the risks. The process may involve engineering controls, administrative controls, training, extra supervision or the use of personal protective equipment (PPE).
4. Record your findings and implement control measures
Document the results of your risk assessment, including the identified hazards, the individuals at risk, the level of risk and control measures.
Provide training and information based on the findings and control measures to relevant personnel such as employees, contractors and supervisors, and ensure recommended precautions are effectively implemented and maintained over time though supervision, inspections and audit.
5. Review and update your machinery risk assessment
Regularly review and monitor the effectiveness of control measures in place. Update the risk assessment as needed (see below), especially when there are changes in equipment or work processes or if new hazards emerge or findings from accident investigations, inspections and audits highlights the need.
Keep records of ongoing reviews and changes made to the risk assessment. Also record that relevant personnel are informed and trained.
When is a machinery risk assessment necessary?
A machinery risk assessment is necessary in the following circumstances:
1. Introduction of new machinery
Whenever new machinery is introduced into a workplace (even if the equipment is hired), a risk assessment must be conducted to ensure the equipment:
- Is safe for use in that particular environment.
- Will be used for the purpose intended by the manufacturer.
- Will be used by those who have received appropriate training.
2. Work environment changes
If there are changes to the work environment such as layout modifications, new structures or alterations that affect a machinery’s operation, a risk assessment should be updated to reflect these changes. Workers should be consulted about the changes.
3. Process or activity changes
When there are changes in work processes or activities involving machinery, a risk assessment must be adapted to account for any new risks or hazards and workers consulted with about the changes.
4. Modifications to the plant
Any modifications or upgrades made to existing machinery or plant equipment should trigger a reassessment of risks to ensure machinery remains safe to use.
5. Accidents or near misses
Incidents involving machinery, including accidents or near misses, should prompt a review of the risk assessment. This helps in identifying the root causes and taking corrective actions to prevent future occurrences.
6. Changes in legislation
Stay up to date with changes in legislation related to machinery safety. If there are changes in regulations or standards that affect machinery safety, it is essential to review and update the risk assessment to remain compliant.
7. New industry guidance or standards
When new industry guidance or standards are published that are relevant to the machinery in use, these must be incorporated into the risk assessment to ensure best practices are followed.
8. Scheduled reviews
Even for machinery classified as low risk, reviews of a risk assessment should be conducted periodically. For high-risk machinery, more frequent risk assessments will be required.
A machinery risk assessment is a dynamic document that must be regularly reviewed and updated to prevent accidents and injuries.
Do you need machinery risk assessment advice?
If your business uses machinery or supplies it to others, you are required to manage the potential dangers associated with it. Ensuring machinery safety is not only a legal obligation but also a crucial step in protecting your employees and others.
At Praxis42 our health and safety consultants specialise in helping organisations develop comprehensive machinery risk assessments. Our services are based on legal principles and tailored to your specific requirements. We understand every business is unique and our risk evaluation process reflects that.
Would you like to know more? Find out about our risk assessments services.