
Manual handling activities cause a third of accidents in British workplaces, so employers must manage and control the risks to employees. Employersโ responsibilities are covered in the Manual Handling Operations Regulations 1992 (MHOR). This guide answers common questions.
What are the Manual Handling Operations Regulations 1992?
The Manual Handling Operations Regulations 1992 (MHOR), as amended by the Health and Safety (Miscellaneous Amendments) Regulations 2002, cover the responsibilities of employers, managers, safety representatives and employees for controlling and reducing the risk of injury in the workplace due to manual handling operations.
Injuries caused by manual handling are part of a wider group known as musculoskeletal disorders (MSDs). These injuries and conditions can cause pain to the back, muscles, tendons and ligaments, joints, and limbs.
Employers should also be aware of their general responsibilities for health and safety, including manual handling, as outlined in the Health and Safety at Work etc Act 1974. Read our in-depth Health and Safety at Work etc Act 1974 guide to learn how it applies to you.
What is the definition of manual handling?
The Manual Handling Operations Regulations 1992 define manual handling as:
“Any transporting or supporting of a load (including the lifting, putting down, pushing, pulling, carrying or moving thereof) by hand or bodily force.”
This broad definition includes lifting objects like boxes, pushing or pulling trolleys, or even moving animals or people. It highlights the diversity of tasks covered under the regulations, making their implementation crucial across various industries, including retail, construction, healthcare, and office environments.
What do the Manual Handling Operations Regulations 1992 cover?
Under the Management of Health and Safety at Work Regulations 1992, employers must assess the risks to their employeesโ health and safety. If hazardous manual handling of loads is identified, you also need to comply with MOHR.
The Health and Safety Executive defines the responsibilities of employers under MOHR in three steps. They must:
- Avoid hazardous manual handling. Avoid hazardous manual handling operations โso far as reasonably practicableโ. Employers must eliminate manual handling tasks that pose significant risks to employees wherever reasonably practicable.
- Assess risks of manual handling. Assess the risk of injury to employees from unavoidable hazardous manual handling. If manual handling cannot be avoided, employers must conduct a manual handling risk assessment to evaluate the potential risks associated with the task.
- Reduce risks to the lowest level reasonably practicable. Employers must take measures to minimise risks, such as providing mechanical aids, altering the task, or improving working conditions.
Why are the Manual Handling Operations Regulations 1992 important?
The official statistics show why the Manual Handling Operations Regulations 1992 are needed.
Manual handling activities cause a third of accidents at work in Britain. Of the 61,663 non-fatal injuries reported in 2023/2024 under the Reporting of Injuries, Diseases and Dangerous Occurrences Regulations (RIDDOR), 17% were due to handling, lifting or carrying, while 10% were as a result of people being struck by a moving object.
Discover what RIDDOR is and why RIDDOR reporting is important in our expert guide.
Back pain is one of the most common manual handling injuries, and hundreds of thousands of employees suffer from it every year. Employees can experience extreme pain, which causes them to be temporarily unable to do their job. It can also lead to permanent chronic injuries.
Multiple causal factors can lead to the onset of pain from a single activity or an accumulative effect from repeated manual handling operations over time. An individual may experience chronic pain that restricts and impacts their daily life and can also affect the organisation they work for in terms of claims, enforcement fines, lost working hours, costs and reduced productivity.
What are employersโ responsibilities under the regulations?
Employers play a pivotal role in ensuring compliance with the Manual Handling Operations Regulations 1992. Their duties include:
Carry out risk assessments
Under the Manual Handling Operations Regulations 1992, employers must carry out risk assessments for manual handling tasks. They can carry out the risk assessment themselves or engage an external resource. In either case, the assessor must be โcompetentโ. The Health and Safety Executive has example assessment checklists you can download.
A risk assessment should identify hazardous manual handling tasks and develop measures to eliminate manual handling or implement controls to prevent injuries. It should look at the task being carried out, who is doing it, the type of load being handled, and the environment in which the task is taking place.
The Management of Health and Safety at Work Regulations 1999 also requires employers to carry out risk assessments and put in place measures for managing, controlling and reducing workplace risks. This includes manual handling and other related risks such as upper limb disorders (ULDs).
The risk factors employers should consider can be categorised as task, individual, load and environment, known by the acronym TILE. It is sometimes referred to as LITE, which stands for the same words but in a different order.
For more information about implementing this approach, please read our guide, TILE manual handling โ what are TILE and LITE?
Provide suitable training
Employers are legally obliged to provide employees with training, such as through a manual handling course, when risks of injury are identified. The training can be generic and should also relate to the findings from the risk assessment.
At Praxis42 we offer specialised Office Manual Handling Training, and also a Manual Handling Course for those who work in all settings from warehouses to retail.
Implement and review control measures
To minimise risks associated with manual handling tasks, employers should first seek to eliminate hazardous tasks where possible. This can be achieved through automation or mechanisation, such as using conveyor belts, hoists, or lifting aids. If manual handling cannot be avoided, tasks should be redesigned to reduce risk, such as separating loads into smaller, manageable parts.
Adjusting the work environment is another crucial step. Employers should ensure workspaces are ergonomically designed, with adequate space, proper lighting, and safe flooring to reduce risks. Providing appropriate handling aids, such as trolleys or pallet jacks, is also essential. Equipment should be well-maintained, inspected regularly, and selected with input from employees to ensure usability.
Control measures must be monitored and reviewed regularly to ensure their effectiveness. Feedback from employees, combined with reassessment of tasks, helps identify improvements. Investigating incidents or near misses can highlight additional controls needed, supporting a culture of continuous improvement and ensuring compliance with the Manual Handling Operations Regulations 1992.
What are employeesโ responsibilities under the Manual Handling Operations Regulations 1992?
While employers bear the primary responsibility, employees also have duties under MHOR regulation 5 and the Health and Safety at Work Act 1974. These include:
- Using equipment safely. Employees must correctly use tools and equipment provided to minimise risks.
- Following training and procedures. Employees should adhere to safe manual handling practices as instructed by their employer.
- Cooperating with employers. Employees must work collaboratively to ensure workplace safety systems are effective.
Do the regulations apply to the self-employed?
The Manual Handling Operations Regulations 1992 also apply to the self-employed.The regulations state that self-employed individuals are responsible for their own safety during manual handling activities. They should take the same steps to protect themselves and control the risks as employers are required to do for their employees.
Under certain circumstances, employers may be responsible for the health and safety of someone defined as self-employed for tax and National Insurance reasons but who works under the employersโ direction.
The Health and Safety Executive has more information on the health and safety responsibilities of the self-employed.
Is manual handling training a legal requirement?
Employers are legally required to provide health and safety training to employees. A risk assessment for manual handling is likely to highlight a need for training for employees who have to lift, lower, carry, push or pull loads or use equipment at work.
What manual handling training must employers provide?
Training should be relevant to the manual handling work being carried out. The Health and Safety Executive advises that it should cover:
- Manual handling risk factors and how injuries can happen.
- How to use mechanical aids.
- How to carry out safe manual handling, including good handling techniques.
- Systems of work relevant to the employeeโs tasks and environment.
- Practical work so the trainer can identify anything the trainee is not doing safely and correct it.
Manual handling training should be refreshed annually to ensure safe techniques are remembered and used effectively by employees.
How to ensure your organisation complies with MHOR
- Follow the HSEโs guidance to the MHOR.
- Make sure your manual handling risk assessment is up to date and appropriate to the tasks employees undertake.
- Ensure employees undertake manual handling training and refresher training.
Online manual handling training
Are your employees required to push, pull, lift, lower and carry heavy loads?
Our IOSH Approved online Manual Handling Course is built by our Chartered Practitioners and experienced health and safety experts. The course is designed for employees who may engage in manual handling at work across all sectors and supports compliance with the Manual Handling Operations Regulations 1992. We also offer Office Manual Handling Training which raises awareness of manual handling hazards in the office and what steps can be taken to prevent musculoskeletal disorders.
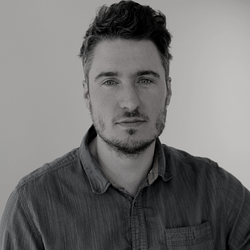
Adam Clarke
Managing Director (Consulting)