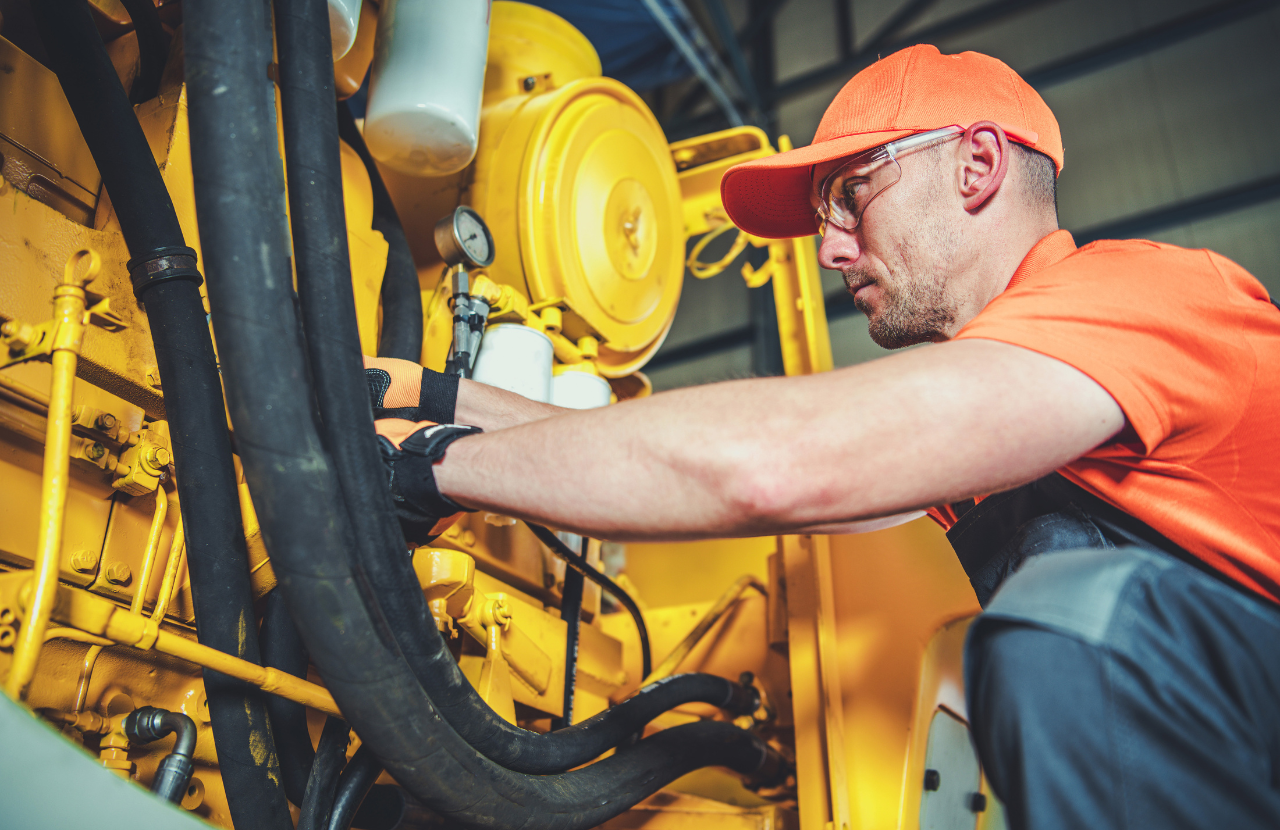
A PUWER risk assessment is vital for helping to ensure workplace equipment and machinery are safe to use and do not pose a risk to employees. PUWER stands for the Provision and Use of Work Equipment Regulations 1998, key legislation designed to make sure all work equipment is suitable, maintained in a safe condition, and used correctly by trained personnel.
Conducting regular risk assessments supports compliance with PUWER, reduces the likelihood of costly equipment failures, and creates a safer working environment for everyone.
What is a PUWER risk assessment?
A PUWER risk assessment is a systematic examination of equipment and machinery to identify potential hazards and ensure they are controlled to protect users from harm. The risk assessment should make sure equipment is:
- Suitable for its intended use. Work equipment must be appropriate for the task, considering the working environment, potential risks, and the capabilities of those using it.
- Maintained in a safe condition. Regular maintenance and inspections are required to keep equipment in good working order. See โWhen should you do a PUWER risk assessment?โ below. This helps to prevent malfunctions, breakdowns, and accidents caused by wear and tear. Maintenance records must be kept as evidence of compliance.
- Used only by those who are โcompetentโ. Employees operating or supervising the use of equipment must have received adequate information, instruction, and training to use it safely. Competence includes understanding how to operate, inspect, and maintain the equipment, as well as recognising any associated risks and control measures.
What is a PUWER assessor?
A PUWER assessor is a competent person with the necessary knowledge, skills, and experience to carry out a PUWER risk assessment. They are responsible for evaluating the risks associated with the use of work equipment and ensuring that the equipment complies with the PUWER regulations.
Our leading health and safety consultants at Praxis42 can carry out a PUWER risk assessment on your behalf, offering solutions tailored to your workplace and machinery. We support you to protect your employees, ensure your operations are efficient and that your organisation complies with health and safety legislation.
What are the risks covered by PUWER?
The Provision and Use of Work Equipment Regulations 1998 (PUWER) covers risks associated with the use of work equipment in the workplace.
Regulations 12 โ 19 cover specific risks such as:
- Excessive noise, vibration, heat, or cold. Exposure to high levels of noise or vibration can cause long-term health issues such as hearing loss or Hand-Arm Vibration Syndrome (HAVS). Extreme temperatures can also create hazards for operators.
- Risks from electrical equipment. Electrical faults, poor maintenance, or inadequate protection can lead to electric shocks, burns, fires, or explosions.
- Unintentional start-up or failure of stop mechanisms. Machinery must be fitted with reliable start, stop, and emergency controls to prevent accidental operation, which could lead to serious injuries.
- Risks from mechanical equipment, falling objects, or ejected particles. Moving parts, rotating blades, crushing hazards, and objects being ejected from machines can cause severe injuries if not properly guarded or controlled.
- Ergonomic risks such as manual handling injuries or posture-related issues. Poorly designed equipment can lead to repetitive strain injuries, musculoskeletal disorders, or manual handling injuries if users must adopt awkward postures or perform excessive lifting.
- Entrapment, entanglement, and shearing hazards. Workers can become trapped or entangled in machinery with exposed moving parts, leading to serious injuries such as cuts, amputations, or crushing incidents.
- Loss of stability and overturning risks. Mobile equipment, such as forklift trucks or lifting platforms, must be stable and properly secured to prevent tipping or collapsing.
- Hazards from chemical interactions. Equipment that handles hazardous substances must be designed and used safely to prevent chemical spills, burns, or exposure risks.
PUWER requires employers to conduct risk assessments, implement control measures, and ensure regular inspections and maintenance to minimise these risks. Thorough training and proper supervision are also essential in ensuring that equipment is used safely and correctly.
How do you carry out a PUWER assessment?
Carrying out a PUWER assessment involves several steps:
1. Identify the equipment
The first step is to compile a comprehensive list of all the equipment and machinery in the workplace. This includes large machinery and smaller tools and portable equipment.
Equipment can be categorised based on:
- Type of equipment. Fixed machinery, portable tools, lifting equipment, etc.
- Location. Where the equipment is used within the facility.
- Frequency of use. Regularly used equipment versus rarely used items.
- Purpose. The specific tasks for which the equipment is used.
By creating a detailed inventory, you can ensure that no equipment is overlooked, and all are subject to assessment.
2. Identify hazards
Once the equipment has been identified, the next step is to examine each piece to identify potential hazards, such as:
- Mechanical hazards. Moving parts that could cause entanglement, crushing, or cutting.
- Electrical hazards. Risks of electric shock or malfunction due to faulty wiring or insufficient insulation.
- Operational hazards. Issues related to incorrect use, such as using equipment for a purpose it was not designed for.
- Environmental hazards. External factors that could affect the safe use of the equipment, such as poor lighting, excessive noise, or temperature extremes.
- Human factors. Operator fatigue, lack of training, or failure to follow safety procedures.
For each piece of equipment, consider scenarios where something could go wrong and the potential consequences. Use a PUWER risk assessment checklist to ensure all possible hazards are accounted for.
Engage with employees who use the equipment daily to gain their insights into potential hazards and practical control measures.
3. Evaluate the risks
After identifying the hazards, evaluate the risks associated with each one. This involves determining:
- Severity. How serious the harm could be if the hazard materialises (for example, minor injury, major injury, or fatality).
- Likelihood. The probability of the hazard occurring, based on factors like equipment condition, frequency of use, and operator competence.
- Risk level. Combining severity and likelihood to establish the overall risk level, often represented as high, medium, or low.
This step helps prioritise the hazards that need the most urgent attention. For example, a high-severity hazard with a high likelihood of occurrence should be addressed immediately.
4. Implement control measures
With the risks evaluated, the next step is to implement control measures to eliminate or reduce these risks to an acceptable level. Control measures can include:
- Engineering controls. Physical modifications to the equipment, such as guards, interlocks, or emergency stop devices.
- Administrative controls. Procedures and policies, such as safe operating procedures (SOPs) and lockout/tagout systems.
- Training and supervision. Ensuring that all equipment users have adequate training, and that supervision is in place for complex or high-risk tasks.
- Personal protective equipment (PPE). Providing appropriate PPE, such as gloves, eye protection, or hearing protection, as a last line of defence.
Each control measure should be practical, effective, and tailored to the specific risks identified.
5. Record the findings
Documenting the findings of the PUWER assessment is crucial for accountability and compliance.
- Record each piece of equipment and its associated hazards.
- Detail the risk evaluation and the control measures implemented.
- Note any actions taken and the person responsible for implementing them.
- Set deadlines for the completion of any corrective actions.
This documentation serves as a formal record of the assessment process and can be used for audits, training, and future reference.
6. Review and update
A PUWER risk assessment must be regularly reviewed and updated to ensure its ongoing relevance and effectiveness.
You should review the assessment at least annually or more frequently depending on the nature of the equipment and its use.
You should also renew the PUWER risk assessment:
- When there are significant changes to the equipment, its usage, or the working environment.
- Following any incidents, accidents, or near-misses involving the equipment.
- As new information or technology becomes available, or when a new risk is identified.
Regular reviews help maintain a proactive approach to managing equipment safety, ensuring that all potential risks are controlled effectively.
When should you do a PUWER assessment?
The frequency of PUWER assessments depends on several factors, including the type of equipment, how it is used, and the environment in which it operates. High-use or high-risk equipment may require more frequent checks, while less frequently used or lower-risk machinery may need assessments at longer intervals. Manufacturer guidelines, industry regulations, and workplace risk assessments also influence how often PUWER assessments should be carried out.
Generally, PUWER assessments should be reviewed at least annually or whenever there are changes to the equipment, how it is used, or the risks associated with its operation. Regular reviews help ensure compliance, prevent accidents, and maintain safe working conditions.
A PUWER assessment must be conducted in the following situations:
- Before new equipment is used for the first time โ to confirm it is suitable for the intended task and does not introduce new hazards.
- When equipment is moved to a new location โ to assess any risks related to its new environment or setup.
- After significant modifications or repairs โ to ensure changes have not introduced new hazards or affected the equipmentโs safety.
- When new risks are identified, or the use of equipment changes. If a risk assessment highlights new hazards or the way equipment is used is altered, a fresh PUWER assessment is required to maintain safety and compliance.
Fill out the form below to get access to our free checklist:
PUWER Training
Our IOSH Approved, CPD Certified PUWER training is designed for those responsible for selecting, using, or maintaining work equipment.
The course provides a comprehensive understanding of PUWER, covering mechanical and non-mechanical hazards, and maintenance and inspection requirements. It also highlights employer and employee responsibilities, ensuring that participants have the knowledge needed to manage risks effectively.
By completing PUWER training, individuals gain the skills to apply PUWER risk assessments, implement control measures, and support workplace compliance with PUWER regulations.
Find out more about PUWER training on our website, or contact our friendly team on 0203 011 4242/info@praxis42.com
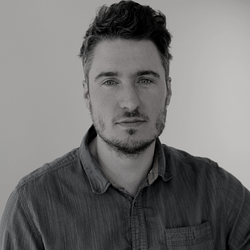
Adam Clarke
Managing Director (Consulting)