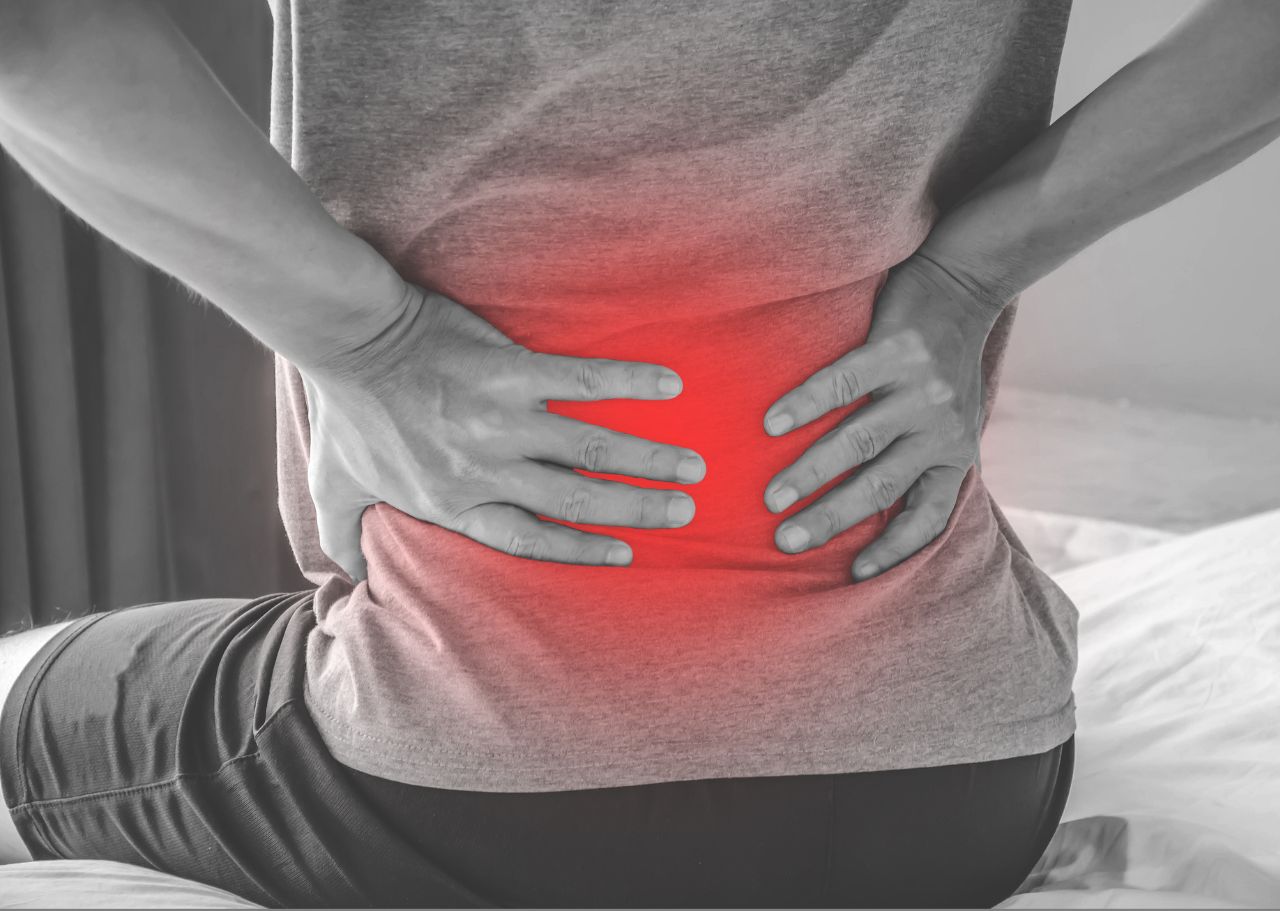
Manual handling is the cause of one in three accidents at work. If risks are not managed and controlled, the consequences of poor manual handling can severely impact the physical and mental health of employees, contractors and others.
With 17% of non-fatal injuries to employees in 2022/23 caused by handling, lifting or carrying tasks, it is essential to know the potential dangers and risks of poor manual handling. The most common cause of non-fatal injuries to employees are slips, trips and falls (32%) and poor manual handling is a contributory factor to this statistic too.
What is manual handling?
Manual handling covers a variety of activities, not just lifting. These tasks involve using physical force and limbs such as hands, and include:
- Twisting
- Pushing
- Lowering
- Pulling
- Carrying
While many activities can be automated using lifting equipment and machinery, some still involve manual exertion by an employee. Manual handling injuries can also happen when employees manually intervene with machinery or equipment, such as stacking boxes onto a conveyor belt.
Who is most at risk from manual handling injuries?
Manual handling injuries occur across all sectors, but employees most at risk work in the following industries:
- Agriculture, farming and fishing
- Cleaning services
- Construction and building trades
- Health and social care
- Hospitality and catering
- Manufacturing and warehousing
- Retail and wholesale trade
- Transport and logistics
- Waste management and recycling.
Common manual handling injuries
The consequences of poor manual handling include short-term and long-term illnesses and injuries.
Superficial injuries
Superficial injuries are short-term injuries caused by minor accidents.
These injuries can involve:
- Bruises
- Cuts
- Sprains and strains
- Tears
They can be caused by sudden, unexpected movements such as losing grip or focus or holding objects at awkward, uncomfortable angles. Superficial injuries comprise 21% of workplace injuries, with sprains and strains making up 28%.
Musculoskeletal disorders
Musculoskeletal disorders can be long-term conditions affecting the muscles, bones, joints, tendons, nerves and ligaments. These conditions typically occur over long periods, with slow wear and tear and repetitive injuries caused by excessive handling or strenuous activities.
The HSE reported that 486,000 employees had work-related musculoskeletal disorders in 2022/23 − with over 40% of the disorders affecting the upper limbs or neck.
Hernias
According to the NHS, a hernia occurs when an internal body part pushes through a weakness in the muscle or surrounding tissue wall. Hernias can happen when straining while lifting heavy loads. This type of injury is increasingly risky for older employees.
Hernias can cause pain and discomfort unless surgically treated.
Hand and foot injuries
Hand and foot injuries can result from poor manual handling. Whether carrying, lifting, pushing or pulling, the hands are often the primary point of contact with heavy loads. If not careful, dropping a load on your feet or fingers/hands can result in breaks, crushing, compression injuries, amputation, fractures and bruising.
Employees can lose grip and injure feet and hands if the load is an awkward shape to hold, too hot or too cold, or slippery. Employees could also cut themselves without care if the load has sharp edges or corners.
Back injuries
Manual handling often places stress on the back. Injury to the back is more likely and can become a long-term ailment without the correct lifting techniques and posture.
Injuries from incorrect handling techniques include slipped discs, lumbar strain and spinal injuries. If back pain goes untreated, it may result in chronic conditions which may impact the ability to work.
Employees should follow our TILE manual handling approach when lifting to minimise the risk of injuries and accidents.
Mental health impact
A potential consequence of poor manual handling may be mental health issues. While not directly a result of manual handling, the risk of injury and accident can negatively impact employee mental health.
Long-term conditions may become difficult to manage for the employee, affecting their mental health. The pain, symptoms and possible inability to perform specific tasks may result in stress, depression or anxiety.
Although physical injuries are more common and widely recognised, their effect on mental well-being should not be ignored. Depression is four times more likely in people experiencing constant pain.
The symptoms experienced with poor mental health, such as disturbed sleep, lack of motivation and low energy, can impact employees’ ability to complete their roles and tasks.
What does poor manual handling cost organisations?
- Compensation, insurance costs and legal fines. Businesses may face expenses related to employees’ compensation claims, which can include compensation for injured workers, legal fees, and increased insurance premiums. They may also face penalties for breaching health and safety regulations.
- Loss of productivity. When employees suffer injuries due to poor manual handling practices, they may need time off work for recovery. This results in lost productivity and increased workloads for other employees. Work related injuries cost UK employers £3.5 billion in 2021/22.
- Reputational damage. If an organisation has a reputation for not prioritising employee safety and health, it can deter potential employees and customers, leading to long-term financial consequences.
How to avoid poor manual handling consequences
As an employer, you must ensure employees, contractors, and others are safe at work, as outlined in the Health and Safety at Work Act 1974. You can do several things to help prevent the consequences of poor manual handling:
Provide training
Ensuring employees undertake manual handling training is the most effective way to reduce workplace injuries. Improved manual handling also leads to increased efficiency and productivity in day-to-day tasks. Safe manual handling is also covered in our comprehensive IOSH Working Safely course.
Complete risk assessments
Risk assessments should be conducted to assess manual handling hazards and appropriate actions taken to reduce these risks. Assessments also consider which safety precautions, such as PPE, should be provided to create a safer environment.
Compliance with regulations
Read our guide to what are the manual handling operations regulations 1992 to ensure your organisation complies with health and safety regulations. Compliance can help ensure you put the correct practices and measures in place.
Provide appropriate equipment
Provide machinery and equipment to help with heavy loading and strenuous tasks. Ensure employees are fully trained to use machinery correctly and safely. You should inspect and assess equipment regularly to maintain its safety.
Safe lifting techniques
To avoid manual handling injuries while lifting objects, it is essential to use proper lifting techniques. Manual handling training covers safe techniques to help employees reduce the risk of injuries.
- Plan your lift by following the TILE approach.
- Use teamwork. If the load is too heavy or bulky for one person, ask a colleague for help. Use teamwork to safely manage heavier items.
- Position your feet. Stand with your feet hip-width apart to maintain balance. Position one foot slightly ahead of the other to improve stability.
- Bend your knees, not your back. Bend your knees to lower yourself to the object, rather than bending your back. Keep your back as straight as possible throughout the lift.
- Get a good grip. Ensure you have a firm and secure grip on the object. Use your palms, not just your fingers, to distribute the load evenly.
- Keep the load close. Hold the object as close to your body as possible. This minimises the strain on your lower back and reduces the risk of injury.
- Engage your core muscles. Tighten your core muscles to provide additional support to your lower back and spine while lifting.
- Lift smoothly and slowly. Lift the load smoothly and slowly by straightening your legs, not your back. Use the power from your legs and hips to lift, keeping your back straight.
- Avoid twisting. Do not twist your body while lifting or carrying the load. Pivot your feet to change direction instead of twisting your torso.
- Take short steps. When carrying the load, take small, steady steps. Avoid rushing or walking too quickly, especially on uneven surfaces.
- Take breaks. If your job involves frequent lifting, take regular breaks to rest and stretch to prevent muscle fatigue and reduce the risk of injury.
- Set down carefully. To lower the load, bend your knees and hips while keeping your back straight. Place the load down gently and avoid dropping it.
Reduce the risk of injuries with Manual Handling training
Created by our experienced health and safety consultants, the Manual Handling training course ensures employees across all sectors have the knowledge and skills required to perform manual handling tasks safely. By focusing on the correct techniques for manual handling, this course lays the foundation for a safer working environment.
We also offer Manual Handling in the Office which raises awareness of manual handling hazards in the office and what steps can be taken to prevent musculoskeletal disorders.
With both courses, participants gain a deep understanding of the principles of manual handling so they can identify and assess potential risks and hazards associated with various activities and respond effectively.
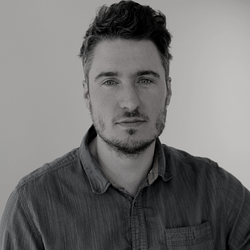
Adam Clarke
Managing Director (Consulting)