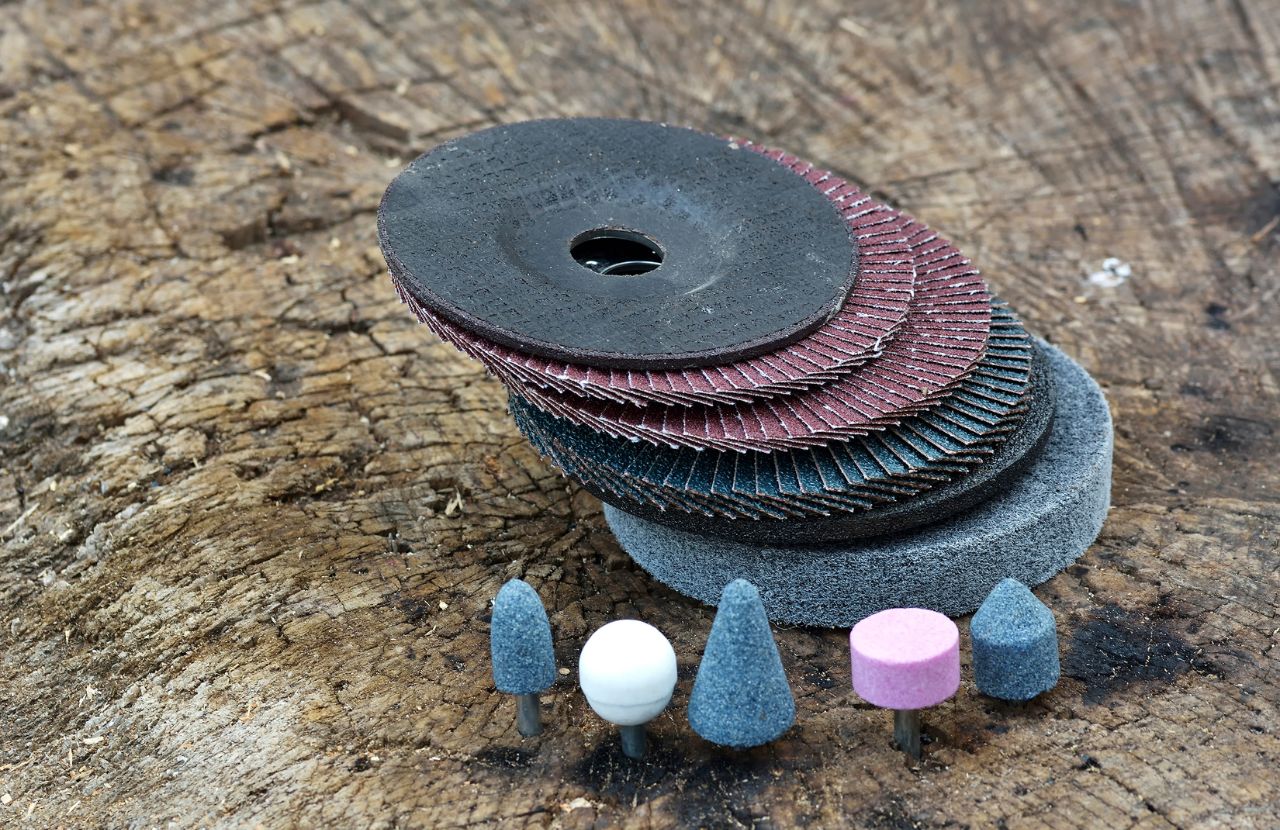
Abrasive wheels can pose a significant risk to employees. Angle grinders, for example, cause 5,400 injuries to people’s heads, eyes, and upper limbs every year.
Abrasive wheels regulations aim to prevent accidents and injuries by setting out specific requirements for the use, maintenance, inspection, and repair of abrasive wheels.
Here’s a quick guide to regulations that are relevant to abrasive wheels and what they mean for employers and employees in practice.
Abrasive wheels legislation
Health and Safety at Work Act 1974
The Health and Safety at Work etc. Act 1974 (HSWA) places a general duty on employers to ensure, as far as is reasonably practicable, the health, safety, and welfare of employees and others who may be affected by their work activities. This includes ensuring work equipment, such as abrasive wheels, is safe and used correctly.
The other legislation we talk about in this article builds on an employer’s responsibilities as set out in the HSWA 1974.
Employers’ responsibilities
Under the HSWA 1974 employers must:
Conduct risk assessments
Risk assessments must be conducted to identify potential hazards associated with machinery and equipment. Following a risk assessment, measures must be implemented to mitigate identified risks. This might involve installing safety devices or arranging additional training, for example.
Implement safe systems of work
Safe systems of work must be implemented. A safe system of work includes developing and enforcing procedures and protocols that workers must follow to operate machinery safely.
Provide information, instruction, training, and supervision
Employees must be provided with adequate information, instruction, training, and supervision to ensure they can use machinery and equipment safely. This includes training on how to operate the machinery, the risks involved, and what to do in case of an emergency.
Continuous training and updates are necessary, especially when new machinery is introduced or when there are changes in safety regulations.
Protect non-employees
Employers must ensure that their activities do not endanger non-employees (e.g., visitors, contractors, and the public). In practice this means:
- Ensuring that machinery and equipment are safely positioned and used in such a way that they do not pose a risk to non-employees.
- Implementing controls and measures to prevent unauthorised access to dangerous machinery.
Employees’ responsibilities
Employees have duties under the Act to take reasonable care of their own health and safety and that of others who may be affected by their actions. Therefore, they must:
- Use machinery and equipment in accordance with the training and instructions provided.
- Carry out a pre-use safety check before using machinery.
- Report any defects or concerns with machinery to their manager or employer immediately.
Management of Health & Safety at Work Regulations 1999
Under the Management of Health and Safety at Work Regulations 1999 all machinery and equipment provided to employees must be safe to use.
Employers must select appropriate machinery, maintain it properly, carry out regular inspections and tests and ensure it is suitable for intended tasks.
The regulations state that, ‘Any faults should be properly rectified as soon as possible. Action should be taken immediately to isolate and rectify the fault where there is a risk of serious or imminent harm.’
Provision and Use of Work Equipment Regulations 1998 (PUWER)
PUWER 1998 replaces the Abrasive Wheels Regulations 1970 and is the main legislation for work equipment.
PUWER requires that all work equipment is:
- Suitable for the intended use.
- Safe for use, maintained in a safe condition, and inspected to ensure it remains in a safe condition.
- Used only by people who have received adequate information, instruction, and training.
- Equipped with necessary safety features, such as guards, emergency stop buttons, and interlocks.
For more about an employer’s responsibilities under PUWER, please see Abrasive wheels safety – what you need to know.
Personal Protective Equipment Regulations 1992
The Personal Protective Equipment Regulations 1992 require employers to provide suitable personal protective equipment (PPE) to employees exposed to health and safety risks at work, where such risks cannot be adequately controlled by other means.
Employers must:
- Provide appropriate PPE such as eye protection, gloves, hearing protection, and respiratory protection to workers using abrasive wheels. The exact type of PPE must be determined through the risk assessment process (for example, not all eye protection will have a great enough impact resistance rating to stop a material ejecting at high speed).
- Ensure that PPE is properly maintained, cleaned, and replaced as necessary.
- Train workers on the correct use and limitations of the provided PPE.
Control of Substances Hazardous to Health (COSHH)
COSHH regulations require employers to control substances that can harm workers’ health, including dust and other particles generated by abrasive wheels.
Employers must:
- Conduct risk assessments to identify hazardous substances produced by abrasive wheels.
- Implement measures to control exposure, such as local exhaust ventilation (LEV) systems to capture dust at the source.
- Provide information, instruction, and training on the risks and control measures related to hazardous substances.
- Monitor exposure levels and ensure they are within safe limits.
Control of Noise at Work Regulations 2005
The Control of Noise at Work Regulations 2005 require employers to assess and control the risk of noise exposure to protect employees’ hearing by:
- Assessing noise levels generated by abrasive wheels.
- Implementing measures to reduce noise exposure, such as using quieter equipment, providing hearing protection, and establishing noise control zones.
- Providing information, instruction, and training on the risks of noise and the use of hearing protection.
- Monitoring noise levels and ensure compliance with legal exposure limits.
Markings on abrasive wheels
Abrasive wheels must have specific markings which provide essential information about the wheel’s specifications and appropriate usage. These markings must comply with British Standards: BS EN 12413 and BS ISO 525.
Markings help to ensure the correct wheel is used for a specific task and that it is operated within safe limits.
By following these markings, operators can ensure they use the correct wheel for the job, mount it properly, and operate it within safe limits, thereby minimising safety risks, and optimising performance.
Here is an explanation of each type of marking:
Trademark
The manufacturer’s name or logo which identifies the source of the wheel and ensures traceability back to the manufacturer.
Test record
A record indicating that the wheel has passed specific safety and performance tests.
Restriction of use
Specific limitations on how or where the wheel can be used. Indicates any special conditions or restrictions, such as ‘Not for wet grinding’ or ‘Use only with specific types of machinery’.
Expiry date
The date beyond which the wheel should not be used. Ensures that wheels are not used beyond their safe shelf life, as some materials (especially organic bonds) can degrade over time.
Speed stripe
A visual marking (often a coloured stripe) indicating the maximum safe operating speed. Provides a quick visual cue to ensure the wheel is not operated at speeds exceeding its design limits.
Dimensions in mm
The physical size of the wheel, typically given as diameter x thickness x bore (eg. 200mm x 25mm x 32mm). Ensures the wheel fits correctly on the machine and is suitable for the intended task.
Specification mark
A code that describes the wheel’s material and characteristics (eg. A24R5V):
A: Abrasive material (eg. aluminium oxide).
24: Grain size.
R: Grade (hardness).
5: Structure (density).
V: Bond type (eg. vitrified).
Provides detailed information about the wheel’s composition and intended use.
Code number
A unique identifier assigned by the manufacturer. Used for inventory control, ordering, and ensuring the correct wheel is selected for specific applications.
Maximum operating speed
The highest speed (in RPM in metres per second) at which the wheel can be safely used (eg. 6000 RPM or 80 m/s). Prevents over-speeding which can lead to wheel failure and accidents.
ISO Type Number (shape)
A standardised number indicating the wheel’s shape (e.g., ISO Type 1 for a flat wheel, ISO Type 27 for a depressed centre wheel). Ensures the correct wheel shape is used for the intended grinding or cutting task.
Mounting instructions
Specific guidance on how to correctly mount the wheel on the machine. Ensures safe and secure mounting, preventing improper installation that could lead to wheel breakage or detachment during use.
Abrasive wheels safety training
By following abrasive wheels regulations, employers and employees create a safer working environment minimising the risk of serious injuries.
Our Abrasive Wheels Training helps employees to understand how to apply regulations in practice, raises awareness of the hazards of abrasive wheels and enables them to assess and mitigate the risks.
This online training course is designed to complement and reinforce in-person training in the workplace on how to mount abrasive wheels safely.
To learn more about our Abrasive Wheels Training please visit the course webpage or contact our friendly team on 0203 011 4242/info@praxis42.com