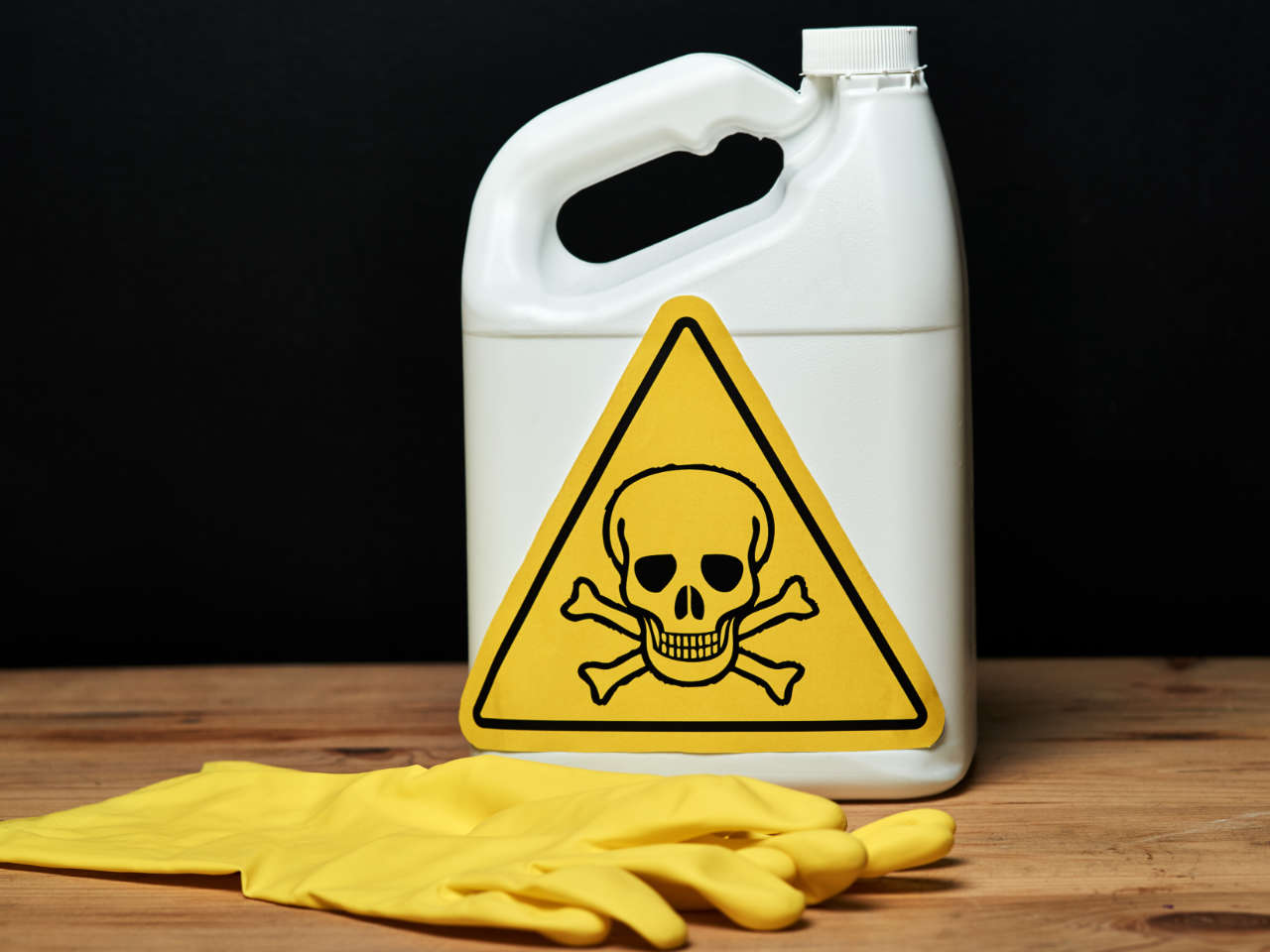
The Control of Substances Hazardous to Health (COSHH) Regulations protect employees from getting ill or injured when working with hazardous substances. This guide tackles the question of what is COSHH and outlines the responsibilities of employers and employees.
Exposure to liquids, fumes, dust, gases, vapours and other hazardous material in the workplace can cause serious damage to employees. Asthma, skin disease and lung cancer are common outcomes of exposure and failure to control the hazards can be fatal. An estimated 13,000 deaths each year are linked to past exposure at work to chemicals or dust, with lung disease from workplace exposure killing an estimated 12,000 people.
Such figures highlight the necessity to identify hazardous substances, where exposures may occur, and to whom and the controls that should be put in place to prevent harm.
What to learn what is COSHH and how to protect your employees from harm? Developed by specialist health and safety consultants, our IOSH Approved COSHH training course provides essential training on the risks associated with the presence and use of hazardous substances.
What is COSHH?
COSHH stands for Control of Substances Hazardous to Health, a law that as the title suggests, requires employers to control hazardous substances. The COSHH Regulations were first introduced in 1988. They have since had several major updates, in 1994, 1999 and 2002, but the framework of managing risk has remained similar.
Under the Control of Substances Hazardous to Health Regulations (COSHH, 2002), employers must prevent, reduce or control exposure to hazardous substances that could cause ill health to employees or anyone visiting the premises such as contractors and suppliers.
COSHH applies to almost every organisation and covers substances and preparations that have the potential to cause harm to health if they are ingested, inhaled, or are absorbed by, or come into contact with, the skin or other body membranes. A hazardous substance can take on many different states including vapours, fumes, dust, fibres, liquids, pastes, flora and fauna as well as being a pathogen such as a bacteria or virus such as Covid19.
Employers must identify the health hazards posed by substances and decide how to prevent them by undertaking a risk assessment. They must then put control measures in place using a hierarchy of control and provide COSHH training for managers and employees.
Employers that fail to properly control the use of hazardous substances could be prosecuted under section 33 of the Health and Safety at Work Act or more specifically the Control of Substances Hazardous to Health Regulations 2002 and face penalties of an unlimited fine or up to two years in prison and in addition to a civil claim for negligence by employees, such as for occupational asthma.
It is vital that employers understand what COSHH is as it is not only a legal requirement, but it will also help ensure wellbeing, a healthier workforce, reduce accidents, boost productivity and reduce costs from claims, work-related sick absence and ultimately by not having to replace valuable workers.
What does COSHH cover?
The COSHH Regulations cover substances that are hazardous to health and which may become harmful in the way they are used, such as by cutting and grinding materials or sprayed which creates dust that can be inhaled and cause harm. It includes:
- chemicals
- products containing chemicals
- dust
- fibres
- fumes
- mists
- vapours
- flora and fauna
- gases and asphyxiating gases
- nanotechnology
- biological agents and pathogens
- germs that cause diseases such as legionella and legionnairesโ disease
Many organisations use substances that could harm employees or visitors but certain industries and jobs are at higher risk due to the prevalence of hazardous substances and how they are used. They include:
- Agriculture
- Construction
- Manufacturing
- Welding
- Woodworking
- Catering and baking
- Agriculture and farming
- Printing and painting
- Engineering
- Cleaning
- Beauty and hairdressing
Examples of specific hazards are:
- Welders, woodworkers and quarry workers face a risk of lung disease from dusty or fume-laden air.
- The fungi and bacteria that can grow in fluids used in metalworking can cause asthma and dermatitis.
- Construction employees who regularly handle wet cement can develop chemical burns or sensitisation dermatitis.
- Employees working with flowers, bulbs, vegetables and fruit can develop dermatitis and fungal infections.
- Frequent contact with water, such as for catering and cleaning job roles, can cause contact dermatitis.
- Certain plants, foods and natural rubber latex gloves can cause dermatitis, asthma or and allergic reaction or anaphylactic shock which can be fatal.
- Natural rubber latex gloves can cause asthma.
- Cleaning products such as toilet cleaners, disinfectants and chlorine bleach can be harmful.
- Hairdressers and beauticians face various hazards from shampoos, conditioners, hair dye and hairspray.
- Prolonged exposure to pesticides increases the risk of developing leukaemia.
- Solvents and inks used in printing can irritate the skin and lead to dermatitis.
- Some substances have other dangerous properties. For example, solvent-based products can give off flammable vapour and dust from material such as wood or flour can explode.
Employer responsibilities for COSHH
COSHH requires employers to assess potential risks of hazardous substances and control exposure. A risk assessment should be carried out, including:
- Identify harmful substances. Look at what workers do, how they do it and what they use and see if there might be harmful exposures. Read product labels and safety data sheets or contact the supplier. Remember that in addition to substances labelled as hazardous, processes can also be hazardous, such as wood dust from sanding. There are nine key symbols used for COSHH which have meanings that are recognised internationally.
- Decide which employees are at risk of harm and how. The assessment should look at how a substance can enter the body such as whether it is inhaled, comes into contact with the skin or could be swallowed. Look at which employees are working directly with substances or those who could be exposed accidentally.
- Decide on precautions to control the risks. Think about how exposure can be prevented such as whether the substance can be replaced with a safer alternative or processes can be changed so the substance is not used. If thatโs not possible, measures must be taken to control exposure.
Such measures could include reducing the temperature of a process so the amount of vapour released is reduced, enclosing the process to contain the release, local exhaust ventilation (LEV), restricting the number of employees involved in the process, checking storage containers are correctly labelled and incompatible substances are separated and introducing dust-free cleaning methods.
Control of hazardous substances is defined as adequate when the risk of harm is โas low as is reasonably practicableโ. According to the Health and Safety Executive, this means:
- All control measures are in good working order.
- Exposures are below the Workplace Exposure Limit where one exists.
- Exposure to substances that cause cancer, asthma or genetic damage is reduced to as low a level as possible.
Employers are also required to provide information, instruction and training for employees. Look for an accredited Control of Substances Hazardous to Health (COSHH) training course to ensure employees are informed.
Employers must also plan for emergencies and accidents, and provide necessary monitoring and health surveillance of employees using hazardous substances.
Organisations with five or more employees must record a COSHH assessment. Although organisations with less than five staff employees do not have to record a COSHH risk assessment, the Health and Safety Executive says it is useful to do so.
The risk assessment should be regularly reviewed to ensure it is up to date and reflects the current workplace environment, guidance, reported accidents and incidents and the findings from any workplace inspections and health surveillance.
Employee responsibilities for COSHH
Employees have a role to play in ensuring a safe working environment when it comes to hazardous substances. This includes:
- following procedures for preventing harm and over-exposure.
- wearing the correct personal protective equipment (PPE) such as eye protection.
- ensuring PPE is inspected pre-use, correctly worn and stored.
- using cleaning and showering facilities provided by their employer.
- reporting and recording accidents, breakages and spillages.
- understanding the meanings of COSHH symbols used to identify hazardous materials.
- understanding what COSHH is by attending COSHH training courses provided by their employer.
Learn about COSHH and how to protect employees from harm with our IOSH Approved COSHH training, including hierarchy of control, how health is affected and harm is prevented, labelling and how to record and review risks to health.