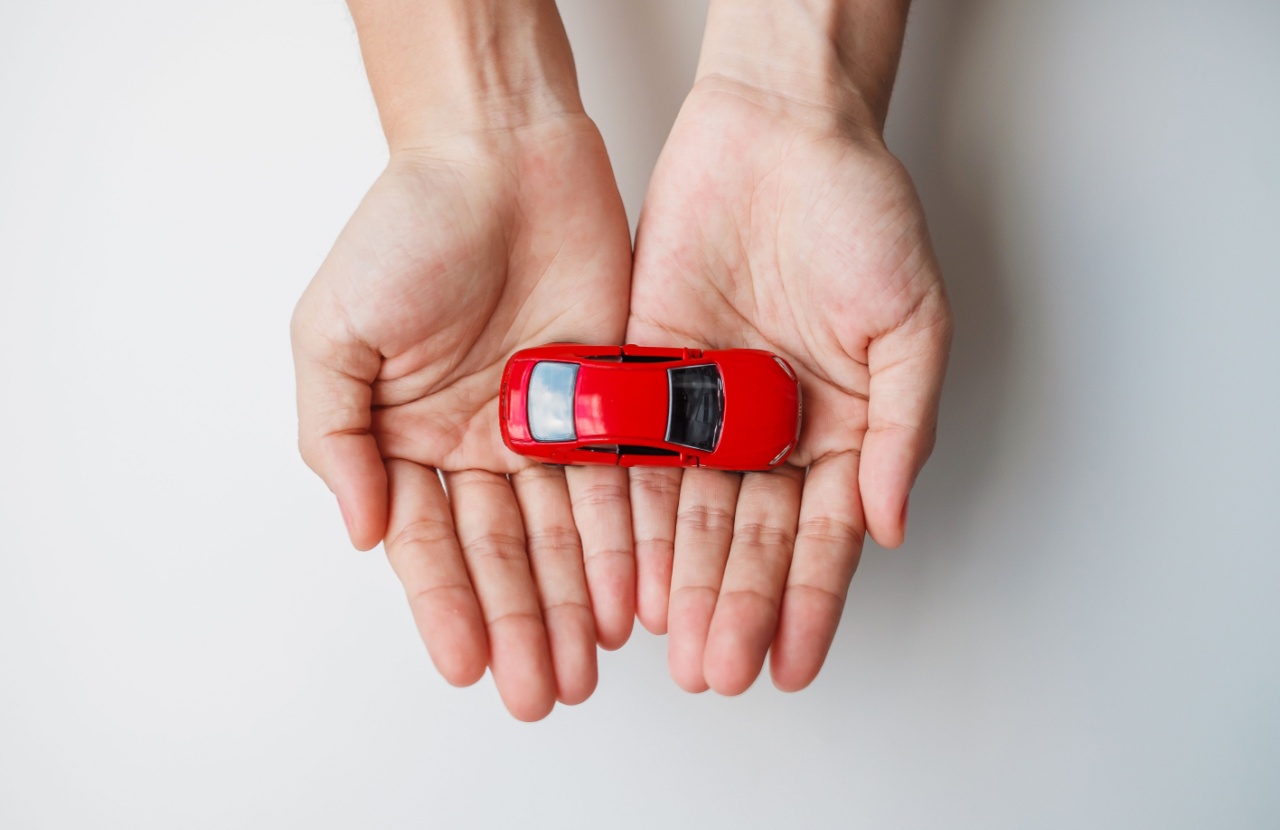
Every year more than 5000 people are injured by workplace transport and 50 people are killed, so the dangers are considerable. A workplace transport risk assessment enables employers to identify foreseeable risks and implement the most appropriate measures to eliminate or reduce them.
Here we talk about the hazards of workplace transport, an employer’s responsibilities and the practical steps that can be taken to keep employees and others safe.
What types of workplaces need a transport risk assessment?
A transport risk assessment is necessary for all workplaces where vehicles, machinery or equipment is used to transport goods or people, including (but not limited to):
- Agricultural and farming operations
- Airports
- Construction sites
- Hospitals and healthcare facilities
- Logistics and transport companies
- Manufacturing plants
- Offices
- Ports and docks
- Retail and wholesale premises
- Utility companies (when maintaining and installing infrastructure)
- Warehouses and distribution centres.
For large office car parks, a workplace transport risk assessment is essential to mitigate the risks to pedestrians as vehicles manoeuvre and are loaded and unloaded. A comprehensive risk assessment identifies the measures that must be implemented to ensure parking areas are safe, orderly, and conducive to the needs of all users.
What are an employer’s legal responsibilities?
There is a wealth of legislation that protects employees and others from health and safety hazards, including transport hazards.
The Health and Safety at Work etc. Act 1974
Under Section 2 of the Health and Safety at Work Act 1974, employers must ensure ‘so far as is reasonably practicable’ the health, safety and welfare of employees at work. They must also protect the safety of those who are affected by their workplace activities, including passers-by and visitors.
Driving vehicles is a high-risk activity, and not all these risks are under an employer’s control, but employers are expected to take every reasonable step to manage risks.
Under the Act, all organisations must have a health and safety policy. Where five or more people are employed, the policy must be in writing. However, it is advisable for organisations of every size to have a written policy.
A written policy supports legal compliance and helps employees to understand their health and safety responsibilities and the employer’s responsibilities for their safety.
The Management of Health and Safety at Work Regulations 1999
Employers are required to carry out a risk assessment under the Management of Health and Safety at Work Regulations 1999. A risk assessment is the foundation for designing safe systems of work to eliminate or reduce the risk from vehicles and pedestrians interacting.
Employers have a legal duty to plan, organise, control, and monitor the risks identified in the risk assessment (See ‘How should risks be managed and monitored?’ below).
If an organisation employs five or more people, the risk assessment must be recorded. However, as with a health and safety policy (see above) it is advisable for all organisations to document risk assessments.
The Workplace (Health, Safety and Welfare) Regulations 1992
Under the Workplace (Health, Safety and Welfare) Regulations 1992 employers must make sure their workplace is ‘organised in such a way that pedestrians and vehicles can circulate in a safe manner’ and that ‘all traffic routes are suitably indicated where necessary for reasons of health or safety’.
Consideration must be given to:
- Lighting. The workplace should be properly lit so work can be carried out safely.
- Traffic routes. This means routes where pedestrians and vehicles move. It includes doorways, ramps, ladders, stairs, and gateways. Enough routes must be provided for the volume of traffic, and routes must be safe and clear. It is recommended that pedestrians and vehicles have separate routes.
- Gates and doors. There should be a clear view from either side of a gate or door. Gates and doors should swing both ways or have a transparent viewing panel. Power-operated doors must be designed so people cannot become trapped.
The Provision and Use of Work Equipment Regulations 1998 (PUWER)
These regulations require that work equipment is fit for purpose and safe to use. It must be properly maintained, and workers must be trained to use it. Please read our article, What is PUWER? to find out how to comply with regulations.
The Lifting Operations and Lifting Equipment Regulations (LOLER) 1998
LOLER covers the risks of using lifting equipment. Equipment must be used by a ‘competent person’ – someone who has the training, knowledge, and experience to operate it safely. Work must be carried out under direct supervision if there are potentially hazardous conditions.
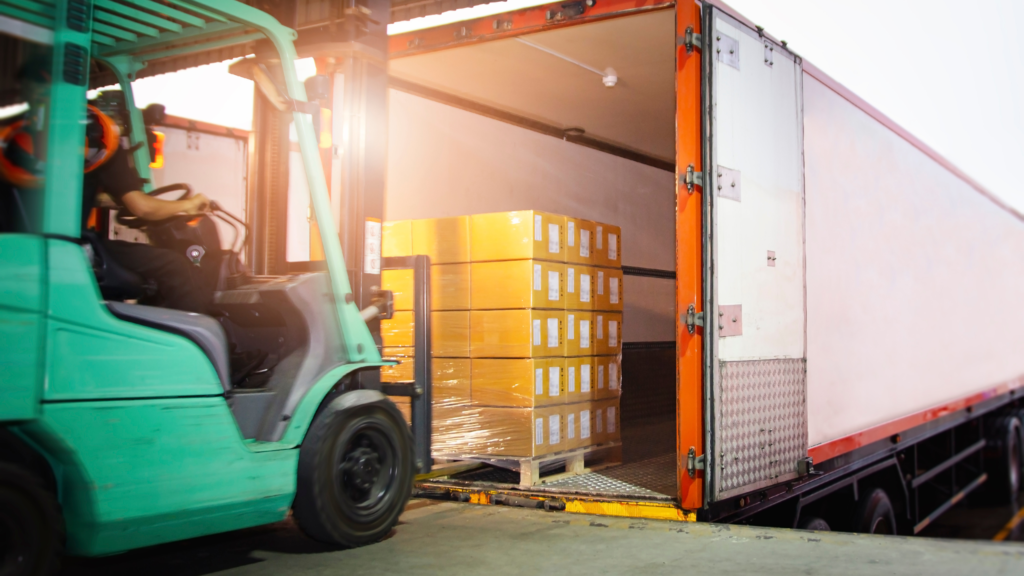
Health and Safety (Safety Signs and Signals) Regulations 1996
The Health and Safety (Safety Signs and Signals) Regulations require employers to install the necessary safety signs to warn employees and others of potential hazards. Signs must be clear, easily understood and prominently displayed. They must be updated as necessary and maintained to ensure they continue to be visible, relevant, and effective.
The Personal Protective Equipment at Work Regulations 2022
The Personal Protective Equipment at Work Regulations require employers to provide employees with personal protective equipment (PPE) when risks cannot be adequately controlled. Employees must not be expected to pay for PPE and must be trained how to use it.
What should you consider when carrying out a transport risk assessment?
A workplace transport risk assessment is a tool to identify risks so employers can do ‘everything reasonably practicable’ to protect people from harm. This means weighing up the level of risk against the cost, effort, and time it would take to control the risks.
The Health and Safety Executive (HSE) highlight three main areas of focus for carrying out a workplace transport risk assessment:
- Safe sites. This includes assessing the design, physical characteristics and activities undertaken at the workplace.
- Safe vehicles. Evaluating the suitability of vehicles used in operations, ensuring they are well-maintained and equipped with safety features. Regular maintenance is essential.
- Safe drivers. Drivers must be competent and have had adequate training. Effective monitoring systems are vital to ensure safe driving standards.
When carrying out or reviewing risk assessments employees should be consulted. Employees who are working with vehicles and machines every day are likely to notice important hazards and have useful, practical ideas about controlling risks.
What are the hazards of workplace transport?
Common hazards that might be considered in a workplace transport risk assessment are:
- Collision with pedestrians. Vehicles like forklift trucks, delivery vans and cranes can collide with pedestrians.
- Vehicles overturning. Forklift trucks, trucks and other heavy machines can overturn due to uneven terrain, excessive speed, or improper loading.
- Falling loads. Improperly secured or stacked loads on vehicles can fall during transport endangering people and property.
- Crushing hazards. People can be crushed between vehicles and fixed structures such as walls, racks, or other vehicles, especially in tight spaces or blind spots.
- Limited visibility. Some vehicles have limited visibility for operators, causing blind spots where pedestrians and other vehicles may not be seen.
- Unsafe reversing. Reversing vehicles pose a significant risk, as operators have limited visibility, and pedestrians may not be aware of the vehicle’s movements.
- Inadequate training. Insufficient training for vehicle operators can lead to errors in operation, increasing the likelihood of accidents.
- Poor maintenance. Vehicles that are not properly maintained can have mechanical failures, such as brake failure or steering issues.
- Restricted spaces. Working in restricted spaces like warehouses or loading bays increases the risk of collisions and crush injuries due to limited manoeuvring space.
- Lack of pedestrian awareness. Pedestrians may not be aware of vehicle movements or may not follow designated routes, increasing the risk of accidents.
How should risks be managed and monitored?
The HSE recommend following the ‘Plan, Do, Check, Act’ approach to health and safety management as a way to make sure risks are identified and controlled consistently to protect people from harm and comply with legislation.
Do you need a workplace transport risk assessment?
Our health and safety consultants have experience across a broad range of industries. We can work closely with you on-site to carry out a workplace transport risk assessment, advising you on the most practical ways to reduce risks.
We have the expertise to help you keep your employees and visitors safe, and to comply with legislation and current Health and Safety Executive (HSE) guidance.
To discuss how we can support you, please call our friendly advisors on 0203 011 4242 or email info@praxis42.com