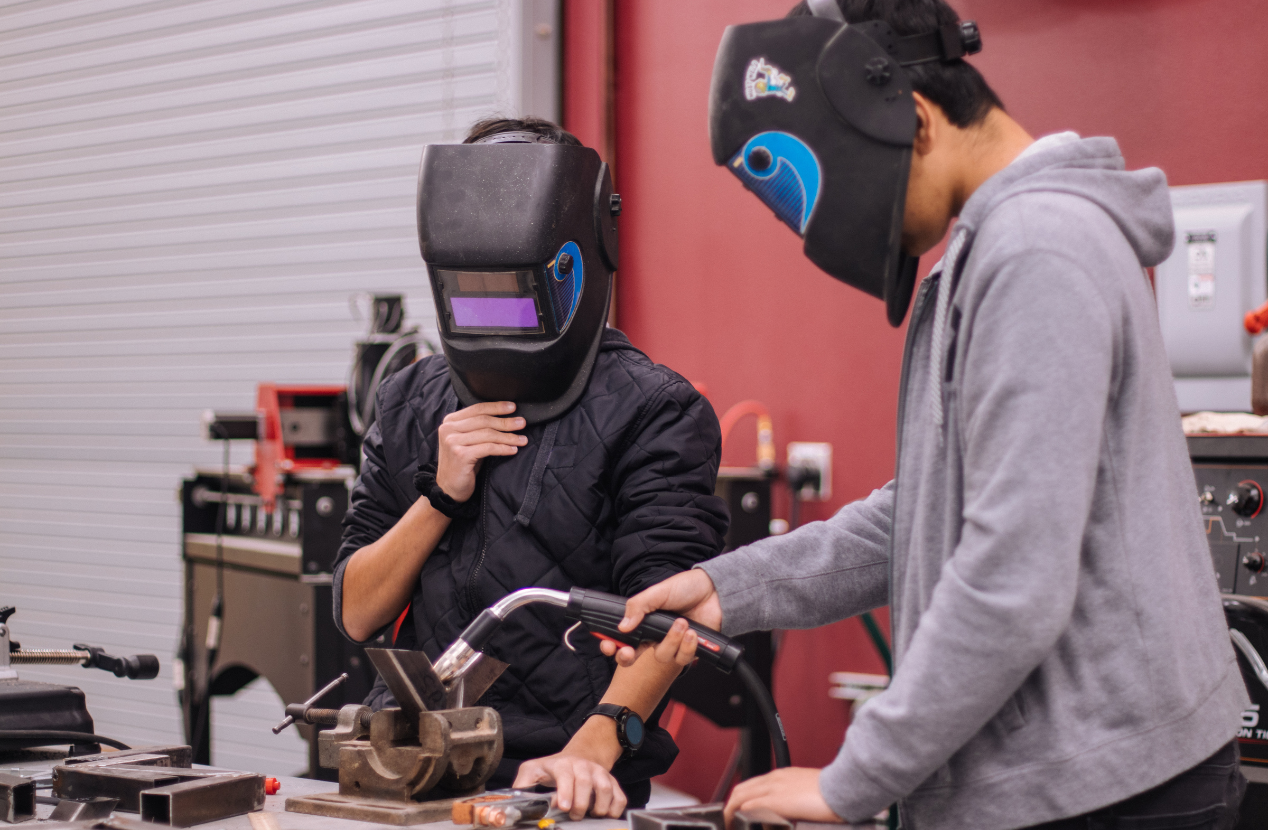
Meeting PUWER training requirements is essential for workplace safety and compliance. The Provision and Use of Work Equipment Regulations 1998 (PUWER) mandate that employees must be trained to use, inspect, and maintain work equipment safely and effectively.
These regulations ensure that all workplace equipment is fit for purpose, properly maintained, and operated by competent individuals to prevent accidents and injuries.
Why is PUWER training important?
Here are the reasons why it is essential employees receive PUWER training:
Prevention of workplace accidents and injuries
Improper use of work machinery is a significant contributor to workplace accidents. The Health and Safety Executive (HSE) highlight that many serious and sometimes fatal accidents occur due to poorly guarded work equipment or improper use.
In the United States, data from the Occupational Safety and Health Administration (OSHA) indicates that contact with objects and equipment is a leading cause of work-related fatalities and injuries. In 2023, there were 5,283 fatal work injuries, with a significant portion resulting from improper machinery use.
In 2021, a 22-year-old worker was fatally crushed while moving machinery. The investigation revealed that he had not received adequate training for the task, and the company was prosecuted and fined ยฃ80,000. This tragic case illustrates how horrific the consequences can be, particularly for young people (see โWho needs PUWER training?โ below).
Legal compliance
Under PUWER Regulation 9, employers must ensure that anyone who uses work equipment receives adequate training, including instruction on the equipmentโs correct use, risks, and safety precautions. Failure to comply can result in legal action, fines, or prosecution, particularly if inadequate training leads to an incident โ see above.
Employers must be able to demonstrate compliance with PUWER by keeping records of training. The Health and Safety Executiveโs Health and Safety Training: A Brief Guide advises that organisations document all training activities to show that reasonable steps have been taken to ensure employee competence.
In the event of an HSE inspection or workplace accident, training records can provide evidence that legal obligations have been fulfilled.
Increased workplace efficiency and reduced downtime
Effective PUWER training prevents accidents, and it improves operational efficiency. Employees who understand how to use and maintain equipment correctly are less likely to misuse it, which reduces equipment breakdowns, costly repairs, and downtime.
Training also ensures that workers can identify faults early and report them before they lead to hazardous failures. For example, in manufacturing environments, where heavy machinery is used daily, trained employees can spot wear and tear on moving parts before they become a critical issue, reducing the likelihood of sudden failures that could halt operations.
Who needs PUWER training?
PUWER training is essential for various people in a workplace, including:
Workers, managers and supervisors
PUWER Regulation 9 mandates that employers ensure all individuals using work equipment receive adequate health and safety training. This includes understanding the methods of using the equipment, associated risks, and necessary precautions.
Employers are also required to provide adequate training to employees who supervise or manage the use of work equipment. This training should cover safe usage methods, potential risks, and preventive measures.
Maintenance personnel
Regulation 7 specifies that tasks such as repairs, modifications, maintenance, or servicing of work equipment must only be performed by individuals specifically designated for these operations. These designated persons must receive adequate training related to their specific tasks to ensure safety.
Young people
Training and proper supervision of young people is particularly important due to their relative immaturity and lack of familiarity with the working environment. Induction training is crucial, as young workers often have little or no prior experience to draw upon.
Although PUWER does not specify age-related training, Regulation 19 of the Management of Health and Safety at Work Regulations 1999 advises employers to take special care when assigning young people to tasks involving machinery. Employers should ensure that young workers receive appropriate instruction, supervision, and gradual exposure to tasks involving work equipment.
More details can be found in the HSE’s Safe Use of Work Equipment guidance.
What should a PUWER training course cover?
To meet PUWER training requirements a PUWER course should cover:
Legal responsibilities
A PUWER training course should cover the employerโs duty to ensure that employees receive instruction on the safe use of work equipment, as well as employeesโ responsibility to follow these safety measures.
Employees should be informed of the legal implications of non-compliance, including potential enforcement actions and fines.
Equipment safety
Employees must learn to identify hazards associated with different types of work equipment and conduct risk assessments before use.
Training should include the correct use of protective devices, safety guards, and emergency stops to prevent workplace accidents. Workers should understand safe operating procedures for different machines, including load limits and correct handling techniques.
Inspection and maintenance
Training should provide step-by-step instructions on conducting pre-use inspections to identify faults, damage, or wear.
Employees must be trained to recognise unsafe conditions and report defects promptly to prevent accidents. Maintenance personnel must understand scheduled servicing requirements and their role in ensuring work equipment remains in safe working condition.
Control measures
Safe working practices, including standard operating procedures for start-up, operation, and shutdown of machinery, must be covered.
Employees must be trained on emergency response protocols, including what to do in case of equipment failure or hazardous incident. Training should include lockout-tagout (LOTO) procedures, so workers understand how to isolate equipment from energy sources before maintenance or servicing.
When should PUWER training be undertaken?
PUWER does not prescribe specific intervals for training. However, the Health and Safety Executive (HSE) advise that training is refreshed at suitable intervals to make sure workers remain competent.
Training should take place:
- At induction. New employees should receive PUWER training as part of their onboarding process if they will be using work equipment. This ensures they understand the risks and safe operational procedures before beginning work.
- When new equipment is introduced. Whenever new machinery or tools are brought into the workplace, employees must be trained on how to operate them safely, including any specific risks and control measures.
- Following incidents or near misses. If an accident or near-miss occurs involving work equipment, refresher training should be conducted to reinforce safety practices and prevent recurrence.
- When significant workplace changes occur. If there are changes in processes, working environments, or regulations affecting equipment use, additional training should be provided to maintain compliance and safety.
- At regular intervals. Periodic refresher training should be provided to reinforce knowledge, address any changes in regulations, and ensure employees remain competent in using work equipment.
How can PUWER training be delivered?
PUWER training can be delivered in several ways:
eLearning
Online training is increasingly recognised as one of the most effective methods, as it provides flexibility, accessibility, and consistency across an organisation. It enables employees to complete training at their own pace, ensuring they fully understand PUWER requirements before applying them in practice.
Our PUWER training online course incorporates interactive elements such as quizzes, scenario-based learning, and multimedia content. When learners are engaged, they are more likely to understand and retain knowledge. Importantly, online training provides a digital record of completion to support compliance with PUWER training requirements.
Online training is a valuable complement to on-the-job training (see below).
On-the job training
On-the-job training is an essential component of PUWER compliance. Employees receive practical, real-world instruction on using specific equipment safely, tailored to their exact working environment. This method ensures that training is directly relevant to the machinery and risks present in the workplace. On-the-job training is particularly important for high-risk industries where direct supervision is necessary until an employee has demonstrated full competence.
A blended approach, combining online learning with practical on-the-job instruction, is usually the most effective way to meet PUWER training requirements. Online training provides the theoretical foundation, ensuring employees understand key principles before applying them in practice.
Classroom training
In a structured environment, employees can engage in face-to-face discussions, ask questions, and receive expert guidance from health and safety professionals. However, classroom training can be time-consuming and costly, particularly for businesses operating across multiple locations.
eLearning to support PUWER training requirements
Meeting PUWER training requirements is fundamental to workplace safety. Every employer must take proactive steps to implement a structured training programme to safeguard employees and business operations.
Our IOSH Approved, CPD Certified PUWER training online provides essential knowledge for managers, supervisors, and employees across a broad range of industries. It covers the identification and mitigation of mechanical and non-mechanical hazards, safe operation practices, and the importance of regular maintenance, inspections, and compliance with safety standards.
Find out more about PUWER training on our website or talk to our friendly team on 0203 011 4242/info@praxis42.com. Please note that we can also tailor training to your organisation and exact industry requirements.
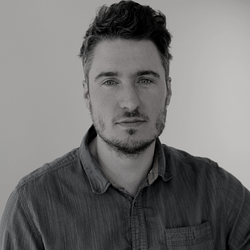
Adam Clarke
Managing Director (Consulting)