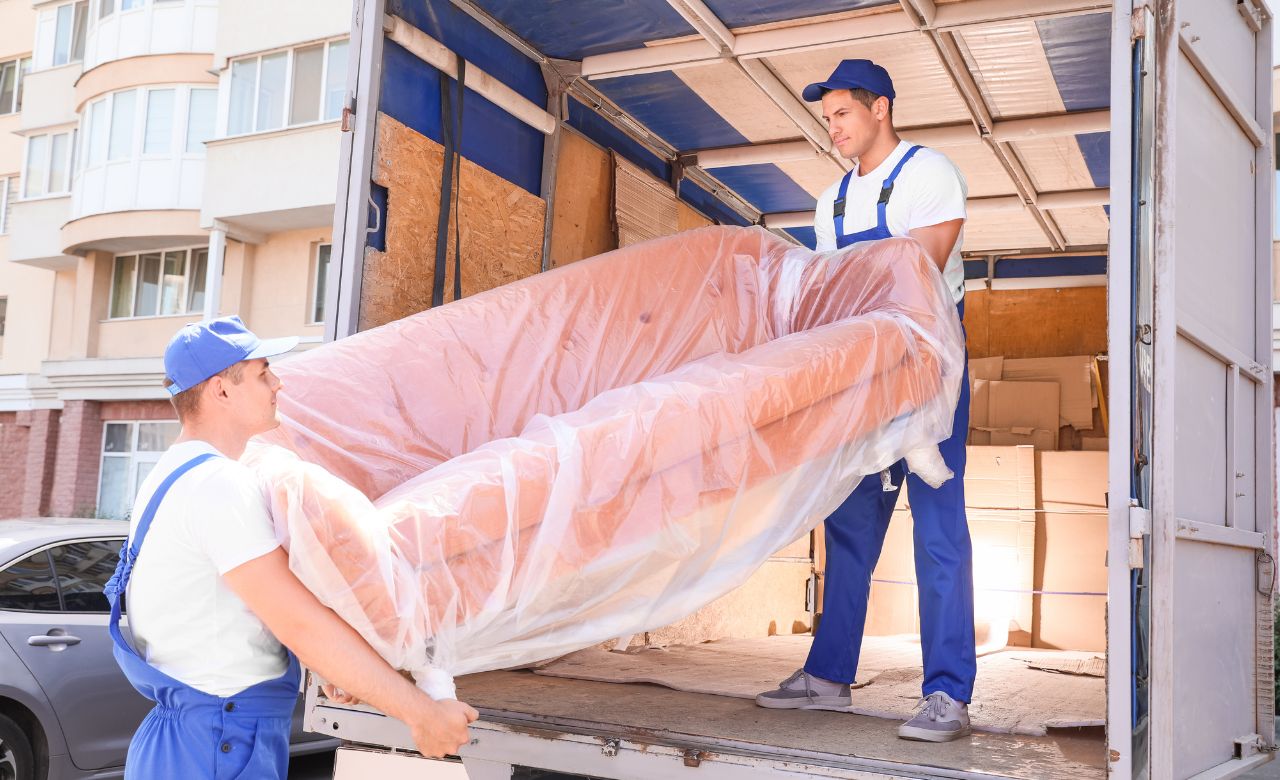
Knowing manual handling weight limits is crucial for preventing workplace injuries. According to Unison, over a third of workplace accidents are cause by improper manual handling.
It is vital that employers ensure there are manual handling health and safety policies and guidelines in place and that they are followed, as per theย Manual Handling Operations Regulations 1992.
What the law says for employers
The Health and Safety at Work etc Act 1974ย states that all employers, regardless of industry, have a duty to protect the โhealth, safety, and welfareโ of their employees and anyone else on the premises, including visitors and members of the public.
A primary way for employers to abide by the Act is to conduct risk assessments. It is recommended that these are carried out at least once a year andย when new procedures or equipmentย are introduced.
As well as risk assessments, employers must provide easily accessible information about any workplace risks to health and safety, consult employees on health and safety policies, provide adequate training, such as a manual handling course, and have a risk-reporting system in place.
Why is safe manual handling essential?
Employees should understand the consequences of poor manual handling and be able to employ safe lifting techniques, as well as know their safe manual handling weight limit.
The most common manual handling injuries occur in the lower back, knees and hands โ all parts of the body involved in the lifting process. Injuries can range from muscle strains to ligament tears. An incorrect lifting form over long periods can result inย musculoskeletal disordersย (MSD), such as tendonitis or arthritis.
Other consequences of manual handling incorrectly can include damaging the workplace environment or the object being carried, as well as potentially harming other employees.ย
What are safe manual handling weight limits?
How much weight is safe for an employee to lift depends on several factors:
- Task โ how far does the load need to be carried and for how long? How strenuous is the work? Is there any twisting or reaching involved? Can the person stop to rest?
- Individual โ is the person physically able to lift or carry the load without straining themselves? Body type, age and disabilities are factors to consider. There is a difference between what somebody is physically able to lift and what they can safely lift.
- Load โ how heavy is the object? Is it easy to grasp or is it bulky and slippery?
- Environment –ย is the floor flat or bumpy? Is there an incline or decline? Are there any potential obstacles?
These factors are known as TILE โ task, individual, load, environment.
While there are is no legal weight limit for manual handling in the UK, the CPDโsย suggested safe maximum weight limits for men and women is 25kg and 16kg, respectively. However, this manual handling weight limit can change depending on the factors above.
For men, the HSE’s suggested manual handling weight limits are:
Height object is lifted
Maximum weight held close to body
Maximum weight at arm’s length
Head height
Shoulder height
Elbow height
Knuckle height
Mid-lower leg height
10kg
20kg
25kg
20kg
10kg
5kg
10kg
15kg
10kg
5kg
For women, the suggested manual handling weight limits are slightly different:
Height object is lifted
Maximum weight held close to body
Maximum weight at arm’s length
Head height
Shoulder height
Elbow height
Knuckle height
Mid-lower leg height
7kg
13kg
16kg
13kg
7kg
3kg
7kg
10kg
7kg
3kg

Tips for safe manual handling
Plan ahead
Before doing any manual handling, encourage employees to plan.
Have them assess the load they need to carry, where they will be carrying it to, and if there are any potential obstructions (refer to TILE above).
Will they need help? Will they need to stop mid-way to rest their load and adjust their grip?
Ensure a good grip
To avoid damage to the item being carried or themselves, ensure that employees have a good grip on the load before attempting to lift or carry it.
If possible, have employees โhugโ the load to their body to provide additional stability. To mitigate the risk of injury, consider providing gloves.
Wear the correct footwear
When lifting and carrying, employees must have complete contact with the floor. This is so they can maintain the correct posture and stay balanced.
Slip-resistant footwear with some form of ankle support and a flat sole, such as work boots and some styles of trainers, is an excellent choice for avoiding accidents and injuries.
Grip and ankle support can become worn over time, so ensure employees regularly check the condition of their footwear.
Have the correct posture
Having the correct posture is vital for avoiding injury when lifting an item.
Ensure employees are trained in proper lifting techniques โ back straight, shoulders back, knees bent, and looking straight ahead โ especially those who undertake a regular amount of this activity as a part of their role.
When carrying, ensure your employees adopt a stable position, with one foot in front of the other. They should keep their load close to their midsections as they move and look ahead to avoid obstacles.
Employees should lift what is safe, not what they can
There is a difference between what an employee can lift and what an employee can safely lift. Encourage employees to only lift what they safely can to avoid potential injuries and overexerting themselves.
Manual Handling Awareness Training
Created by experienced health and safety consultants, our IOSH Approved manual handling training course helps employees across all sectors to identify hazards so they can proactively mitigate risks. They will learn how to handle loads safely by employing correct lifting techniques and they will know when to use equipment or seek help.
We also offer Manual Handling in the Office which raises awareness of manual handling hazards in the office and what steps can be taken to prevent musculoskeletal disorders.
By comprehensively covering both employees’ and employers’ legal responsibilities, the courses ensure that participants understand their roles in maintaining a safe, legally compliant workplace environment.