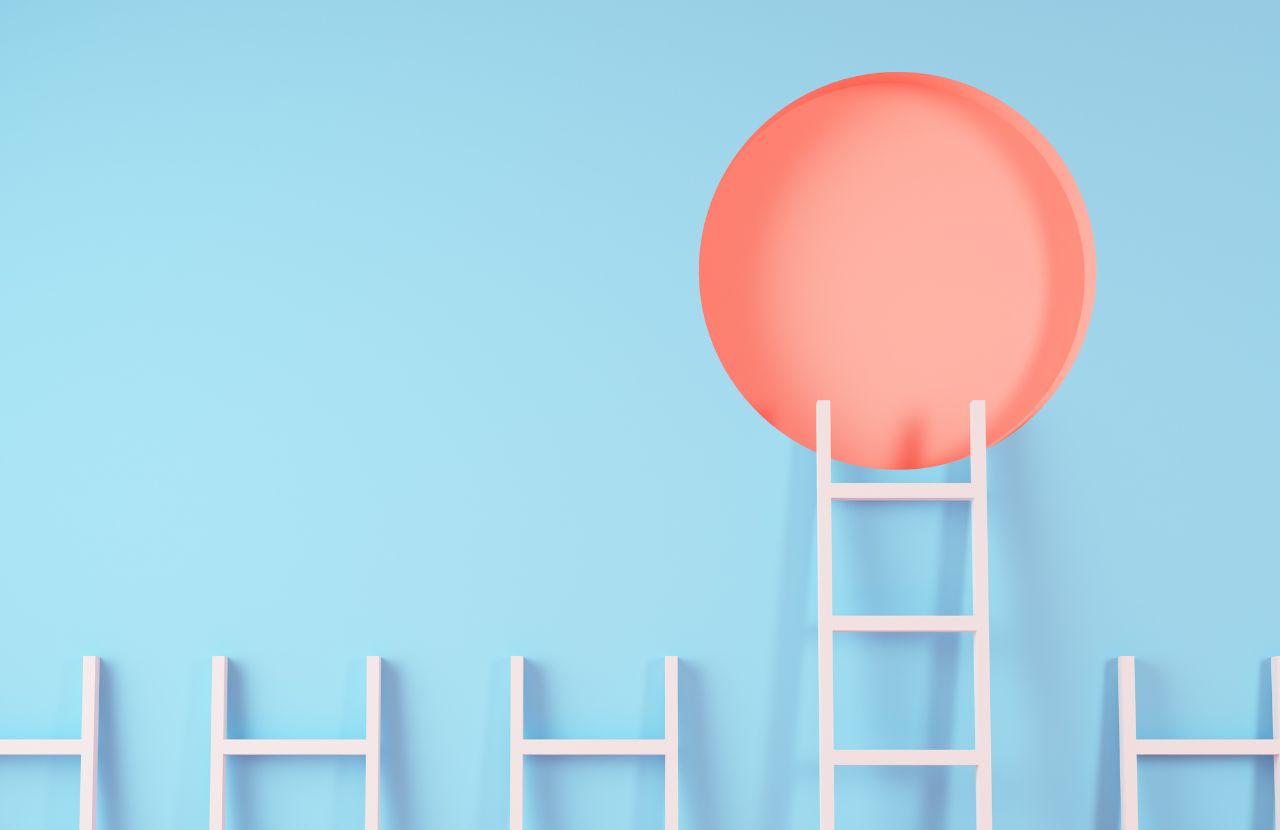
Ladders must be regularly inspected to protect employees’ health and safety and comply with legislation, such as the Work at Height Regulations 2005. In this article we talk about what UK ladder regulations mean for employers and employees. We also answer some frequently asked questions about ladder health and safety.
What are the UK regulations for ladders?
The main legislation for ladder safety is the Work at Height Regulations 2005.
The Management of Health and Safety at Work Regulations 1999 and The Provision and Use of Work Equipment Regulations 1998 (PUWER) are also applicable.
Work at Height Regulations 2005
Section 6 of the Work at Height Regulations 2005 covers the safe use of ladders and stepladders in the workplace.
The regulations emphasize the importance of:
- Selecting the right type of ladder for the task. Ladders must be suitable for the specific work being undertaken, considering factors such as height, weight capacity, and stability.
- Proper maintenance and inspection of ladders. Employers are responsible for ensuring that ladders are kept in good condition and regularly inspected for any defects or signs of wear and tear.
- Proper training for employees who use ladders as part of their work. Workers must be trained in the safe use of ladders, including how to set them up correctly, climb and descend safely, carry out ladder checks and recognise hazards.
- Supervising employees to ensure they follow correct procedures and adhere to safety protocols when using ladders, reducing the risk of accidents caused by human error.
- Conducting risk assessments before using ladders. Employers must assess the risks associated with working at height and implement control measures to mitigate these risks. This may involve considering alternative access methods or implementing additional safety measures, such as using fall protection equipment.
Management of Health and Safety at Work Regulations 1999
Under the Management of Health and Safety at Work Regulations 1999 employers are required to conduct risk assessments to identify potential hazards in the workplace, including those related to working at height.
The regulations also require employers to provide adequate information, instruction, training, and supervision to employees to ensure their health and safety while working at height.
In addition, a duty is placed on employers to consult with employees on matters relating to health and safety. By involving employees in the decision-making process, employers can benefit from their knowledge and experience, ultimately leading to more effective risk management strategies.
The Provision and Use of Work Equipment Regulations 1998 (PUWER)
PUWER focuses on the safety of work equipment which includes equipment used for working at height, such as ladders, scaffolding and access platforms.
Under PUWER, employers have a duty to ensure that work equipment provided for use at height is suitable for the intended purpose and is maintained in a safe condition. This means ensuring that ladders, scaffolding, and other equipment is maintained and inspected regularly to identify any defects that could compromise safety.
PUWER also requires employers to provide adequate information, instruction and training to employees who use work equipment. This training should cover topics such as the safe use of ladders and scaffolding, as well as how to recognise and report any defects or hazards associated with equipment.
Employers must take measures to prevent access to dangerous parts of machinery and equipment. This may involve implementing guarding or other safety measures to protect workers from falls and other hazards associated with working at height.
Why do we need ladder inspections?
Ladder inspections are critically important. Most fatal accidents at work are caused by falling from height (40%). In the food and drinks industry a staggering 40% of falls from height are from ladders.
In March 2023, Sellafield Ltd was fined £400,000 after a worker fell from a scaffolding ladder and sustained lifechanging injuries. An investigation by the Office of Nuclear Regulation (ONR) found that risks were not adequately controlled and that there were failures in the risk assessment.
These are sobering facts that bring the real-world consequences of poor ladder safety into sharp focus.
By conducting regular ladder inspections and implementing effective health and safety measures, employers can protect employees from serious injuries that may have a significant, long-term impact on their lives and the future of the organisation.
Ladder safety checklist
Our free ladder safety checklist helps you to make sure all the components of your ladder are safe before use.
What is the maximum height you can work from a ladder?
There is no legal maximum height for working from a ladder. However, the Health and Safety Executive (HSE) recommend that when working at a height of 9 metres or more, landing areas or rest platforms are provided at suitable intervals. This recommendation aims to reduce the risk of falling from height because of fatigue.
It is essential for employers and workers to assess the risks associated with working at height and ensure that appropriate measures are in place to manage those risks effectively. This may include considering alternative access methods, such as scaffolding or mobile elevated work platforms (MEWPs) for tasks at significant heights or for prolonged periods.
How long can you legally work on a ladder?
There is not a specific legal time limit for how long someone can work on a ladder. However, the Health and Safety Executive (HSE) recommends that alternative equipment is used for tasks that are likely to last longer than 30 minutes.
When can you use a ladder?
Ultimately, the safety of workers is priority, and decisions about ladder use should be based on the following:
Risk assessment
Employers must assess the risks associated with working at height, considering factors such as the height of the task, the stability of the surface, and the duration of work.
The risk assessment should inform decisions about whether a ladder is the most appropriate equipment for the job and how long it can be safely used.
Low risk and short duration
If the task is low risk and of short duration, a ladder may be suitable for use. However, this should not be the sole determining factor. Even for short-duration tasks, it is essential to ensure that a ladder is used safely, and appropriate precautions are taken to prevent accidents.
Stability
Ladders should only be used when it is safe to do so, when the surface is level and stable, and the ladder can be securely positioned. It is crucial to ensure that a ladder is correctly set up, secured, and used in accordance with safety guidelines and the manufacturer’s instructions.
Alternatives to ladders
When working at height for long periods or in high-risk situations, it is advisable to use alternative equipment, such as mobile tower scaffolds, scaffolding or mobile elevated work platforms (MEWPs).
The decision to use a ladder must be justified by the specific circumstances of the task.
Who should check a ladder before it is used?
Under Section 6 of the Work at Height Regulations 2005, employers are required to ensure that ladders and stepladders are inspected regularly by a competent person. This includes carrying out both formal and informal ladder safety checks.
A competent person for ladder inspections is someone who has the necessary technical expertise, knowledge, experience, and training in ladder safety.
Formal checks involve a comprehensive examination of the ladder’s condition (see the ladder inspection checklist below). These checks must be recorded and carried out at regular, pre-planned intervals.
Informal pre-use checks are carried out by the user before climbing the ladder and do not need to be recorded.
How often should ladders be inspected?
Pre-use checks
A pre-use check should be carried out by the user before each use of the ladder.
These checks are intended to identify any visible defects or damage that could affect the ladder’s safety. This involves visually inspecting the ladder for signs of damage, ensuring that all components are in good working order, and verifying that the ladder is stable and securely positioned.
Pre-use checks do not need to be recorded, but any defects or issues identified must be reported to the manager or employer immediately.
Regular visual inspections
UK ladder regulations require that, in addition to pre-use checks, ladders should undergo regular visual inspections. These inspections must be conducted by a competent person following the manufacturer’s instructions.
Checks must be conducted at planned, regular intervals, depending on the frequency of ladder use and the level of risk involved in the tasks being undertaken. Ladder checks should also be conducted after any changes that could affect the ladder’s condition, such as being dropped or transported to a new location.
Any defects or damage identified during these inspections must be recorded and addressed promptly.
Ladders as part of scaffold
If ladders are part of a scaffold structure, they must be inspected every 7 days by a competent person. This ensures that the entire scaffold system, including the ladders, remain in a safe and stable condition.
Ladder Safety Training
Developed by experienced health and safety consultants, our Ladder Safety Training course equips employees with essential knowledge for using ladders and stepladders safely and supports compliance with UK ladder regulations.
Participants learn how to recognise and mitigate the risks of working on a ladder to protect their own health and safety and that of others. This IOSH Approved, CPD certified course has been created by experienced health and safety professionals. It can be completed at the learner’s own pace and no previous experience is required.