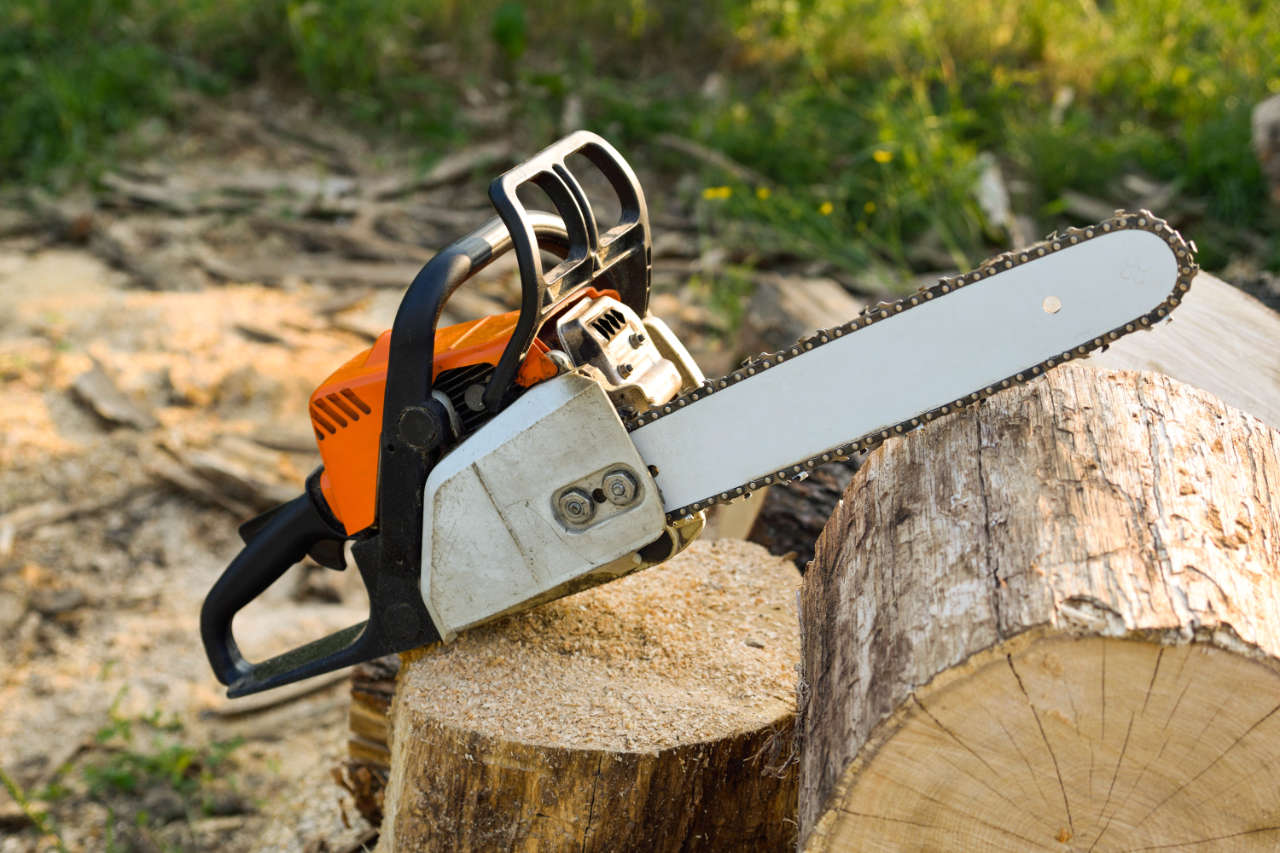
The Provision and Use of Work Equipment Regulations 1998 (PUWER) โ known as the PUWER regulations โ are essential for ensuring the safety and suitability of equipment used in workplaces.
These regulations place responsibilities on employers, the self-employed, and anyone in control of work equipment to ensure it is safe, appropriate for use, and properly maintained.
In this guide, we discuss what equipment is covered by PUWER, how often equipment should be checked, and other key considerations to help you comply with PUWER regulations.
Why are PUWER regulations necessary?
Contact with machinery and being hit by vehicles are among theย most common causes of injury and death in UK workplaces. Between 2023 and 2024, being struck by a moving vehicle was the cause of 25% of reported fatalities at work, with 8% the result of contact with moving machinery.
In 2023-24, there were 561,000ย non-fatal workplace injuriesย with 11% due to being struck by a moving object.
Accidents with machinery and equipment can happen in any organisation, but it is particularly common in the construction, manufacturing and agriculture sectors where the use of heavy machinery is more likely.
If machines are not properly guarded or there is insufficient safety equipment, this can lead to body parts being caught or moving parts and flying objects hitting people. The resulting injuries include severed and crushed limbs as well as blindness.
Similarly, insufficient safety procedures for using vehicles can cause people to be struck or run over, hit by objects falling from the vehicle, or crushed by an overturned vehicle.
PUWER was introduced to minimise such incidents.
For more information about PUWER regulations, please read our guide, What is PUWER?
What equipment is covered by PUWER?
The scope of PUWER is broad. It applies to any work equipment and includes any machinery, appliance, apparatus, tool, or installation used at work.
Theย Health and Safety Executiveย describes it as โany activity involving work equipment and includes starting, stopping, programming, setting, transporting, repairing, modifying, maintaining, servicing and cleaningโ.
Both stationary and mobile equipment are covered. The regulations apply whether the equipment is new or old, and whether the organisation owns or hires the equipment from another organisation or business. The PUWER regulations also cover equipment owned by employees that their employer permits them to use for work.
Some equipment must also comply with other regulations as well as PUWER. For example, lifting equipment is covered by theย Lifting Operations and Lifting Equipment Regulations 1998ย (LOLER), personal protective equipment is covered byย PPE legislation, and pressure equipment must comply with theย Pressure Systems Safety Regulations.
PUWER does not apply to equipment used by members of the public. That is covered by theย Health and Safety at Work etc Act 1974.
PUWER equipment list
Examples of what equipment is covered by PUWER in specific sectors and types of organisations include:
- Offices: computers, printers, shredders, kitchen appliances and building systems (fire, security, heating, plumbing etc.).
- Leisure and entertainment business: fairground rides, bowling alleys. arcade machines and sound / lighting equipment.
- Medical organisations and laboratories: machines, defibrillators and lighting.
- Workshops: hand tools, glue guns, angle grinders and drills.
- Factories and warehouses: trucks, ladders, cherry pickers and roll containers.
- Agriculture: irrigation systems, tractors, machinery and hand tools.
- Construction: cranes, cement mixers, bulldozers, trucks and hand tools.
- Hospitality and food processing: kitchen appliances, ovens, fryers and machines.
Does PUWER apply to hire equipment?
PUWER applies to equipment hired or leased for use at work.
Both the hiring company and the hirer have responsibilities under PUWER to ensure that the equipment is safe and suitable for its intended use.
The hirer must ensure that the equipment is inspected and maintained according to PUWER requirements before and during use.
How often is equipment checked under PUWER?
The frequency of equipment checks under PUWER depends on several factors, including the type of equipment, its usage, and the environment in which it is operated.
PUWER requires:
- Initial inspection. Equipment must be inspected before it is used for the first time.
- Routine checks. Regular visual inspections by the user may suffice for low-risk equipment.
- Formal inspections. High-risk equipment may require thorough inspections by a competent person, which could involve dismantling and checking according to manufacturer instructions.
- Post-modification inspections. Equipment must be inspected after significant repairs, modifications, or changes in usage.
- Environmental factors. Equipment used in harsh conditions, such as outdoors in adverse weather, may need more frequent inspections.
PUWER maintenance and inspections
PUWER requires that equipment is maintained and that inspections are carried out to ensure that all equipment can be operated safely and remains in a safe state to be used. It will also highlight any damage or defects that need to be addressed.
The frequency and detail of maintenance and inspection depends on the type of equipment, how often it is used, and what environments it is used in, such as a construction site or outdoors.
For some equipment, a basic visual inspection by the user prior to use might be sufficient. For equipment that poses significant health and safety risks a detailed and formal inspection, such as dismantling the equipment and inspecting certain parts according to the manufacturerโs instructions, might be required to be undertaken by an authorised and competent person.
Equipment should be inspected when installed and used for the first time, and a check should be carried out every time it is used. Inspections will also be necessary when equipment is used in conditions that could cause it to deteriorate, such as outside in adverse weather conditions, when equipment receives significant modifications and repairs, or there are changes to the way it is used.
Inspections and maintenance must be carried out by a competent person with the necessary skills, knowledge and experience.
PUWER training
Work equipment must be used and maintained correctly to reduce the risk of injury, mechanical failures, and costly disruptions to business activities. PUWER training ensures that employees, supervisors, and managers understand their responsibilities, including equipment inspections, risk assessments, and safe operating procedures.
Whether you need standard PUWER training, or customised content tailored to your industry, our IOSH Approved, CPD Certified course can be adapted to suit your organisationโs specific equipment, work environment, and operational needs. Our training covers key aspects of PUWER compliance, such as identifying hazards, implementing control measures, and ensuring equipment is fit for purpose.
Find out more about PUWER training on our website, or contact our friendly team today on 0203 011 4242/info@praxis42.com
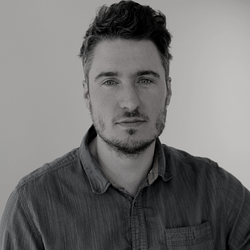
Adam Clarke
Managing Director (Consulting)