
Workplace noise can be more than just a nuisance as it poses serious health risks if not managed effectively. Understanding noise exposure limits UK standards is critical to ensure a safe and compliant working environment.
In this comprehensive guide we explore safe and unsafe noise levels at work and how to effectively measure, monitor and manage noise risks.
What are noise exposure limits in the UK?
In the UK, noise exposure in the workplace is regulated by the Control of Noise at Work Regulations 2005, which set out legal requirements for protecting workers from the risks of excessive noise.
The regulations establish the following noise exposure limits:
Lower Exposure Action Value
This is a daily or weekly average of 80 dB(A), or a peak sound pressure of 135 dB(C).
Here are some real-life examples of low exposure levels:
- Daily or weekly average of 80 dB(A). The noise level in a busy office or a quiet factory floor with machinery operating at low levels. While this is not immediately harmful, sustained exposure can still contribute to hearing fatigue over time.
- Peak sound pressure of 135 dB(C). A brief noise spike from a pneumatic drill being switched on or a sudden clang of metal objects dropping in a workshop. Hearing protection is not legally required but should be considered.
Upper Exposure Action Value
This is a daily or weekly average of 85 dB(A), or a peak sound pressure of 137 dB(C).
These are examples of upper exposure levels:
- Daily or weekly average of 85 dB(A). Continuous operation of machinery like a forklift or conveyor belt in a warehouse. At this level, employers must take steps to reduce exposure, such as offering hearing protection or implementing noise control measures.
- Peak sound pressure of 137 dB(C). A loud bang from a piece of heavy equipment being dropped or an air compressor venting unexpectedly. Employees must use hearing protection if these levels are reached.
Exposure Limit Value
Maximum noise levels at work must not exceed 87 dB(A), considering the protection provided by hearing protection.
An example of exposure limit value is a construction worker operating a pneumatic drill or a factory employee working near industrial presses.
If the noise exceeds this level, even with hearing protection in place, the employer must immediately intervene by stopping work and addressing the noise hazard.
Why are noise levels at work a concern?
Exposure to excessive noise can lead to noise-induced hearing loss (NIHL), tinnitus, and even stress-related conditions. Exposure to excessive noise can lead to noise-induced hearing loss (NIHL), tinnitus, and even stress-related conditions. When employees are subjected to too much noise at work, it not only affects their hearing but can also impact their concentration and overall wellbeing.
Common scenarios where noise hazards arise include:
- Operating machinery in factories or construction sites.
- Working in loud entertainment venues.
- Using power tools or heavy equipment.
The maximum noise level at work should never exceed safe limits, as this could lead to long-term, irreversible damage. Monitoring tools and risk assessments help ensure compliance with maximum noise exposure limits.
Providing health surveillance
Health surveillance is a vital component of managing noise risks in the workplace, particularly for employees exposed to high noise levels over the long term. It involves monitoring workers’ hearing to detect early signs of damage, ensuring timely intervention to prevent further harm.
Employers are required to implement health surveillance under the Control of Noise at Work Regulations 2005 if workers are exposed to noise levels at or above the upper exposure action value (see above).
A health surveillance programme should include regular hearing tests (audiometry), conducted by qualified professionals, to establish a baseline and track changes in workersโ hearing over time. These tests enable employers to identify patterns of noise-induced hearing loss (NIHL) early, enabling adjustments to workplace controls or processes. Workers must be informed about the results and provided with advice on protecting their hearing.
Conducting a noise at work risk assessment
A noise at work risk assessment is a critical process for ensuring compliance with health and safety regulations and protecting employees from the harmful effects of excessive noise.
The process involves several key steps:
1.ย ย ย ย Measuring noise levels
Use a sound level meter for spot measurements in specific locations or during specific processes. For continuous monitoring, use dosimeters that employees wear during their shifts to capture exposure over time.
Conduct measurements during peak working hours when machinery and equipment are in full operation to capture accurate readings. Record data systematically, noting the location, time, type of activity, and noise level in decibels (dB).
It is important to ensure those using the measuring equipment are trained in its proper use and can interpret results accurately. If internal expertise is unavailable, engage an external specialist.
2. Identifying areas or processes where noise exceeds action levels
Compare the recorded noise levels with the HSE action values. The HSE action values are the same as those in the Control of Noise at Work Regulations 2005 (see above), but the HSE provide more practical examples to help employers to comply with regulations.
- Map out areas where noise exceeds these values and identify the specific machinery, tools, or processes responsible.
- Create a noise map of the workplace to visually highlight high-risk areas.
- Conduct a walkthrough of the premises with the noise map and involve employees to gather feedback on where they feel noise is most problematic.
3.ย ย ย ย Evaluating the duration and frequency of exposure
Analyse dosimeter data to determine how long employees are exposed to occupational noise exposure limits.
- Categorise employees based on their roles, noting those who are in high-risk zones for extended periods.
- Use time-logging tools or observational studies to measure how often tasks involving high noise are performed.
- Engage employees in completing a noise exposure diary to understand how their tasks contribute to cumulative exposure over a typical workday.
4. Assessing whether existing measures adequately control risks
Assess the adequacy of existing control measures by:
- Regularly reviewing current control measures such as engineering solutions, administrative processes, and use of PPE to make sure they are effective.
- Reassessing controls whenever new equipment or processes are introduced.
- Conducting fit-testing for hearing protection devices (earplugs, earmuffs) to ensure they provide the necessary attenuation.
- Inspecting noise-reducing equipment like silencers, acoustic panels, or machine enclosures for wear and tear or inefficiency.
- Performing a gap analysis comparing existing measures against industry best practices or standards. Engage employees to discuss whether they find current PPE and controls practical and effective.
Deciding what noise control measures to implement
Controlling noise at work requires a combination of engineering controls, administrative measures, and personal protective equipment (PPE), applied in a hierarchical order. Employers should consult employees when selecting controls, as they can provide insights into the practicality and effectiveness of measures.
The hierarchy of controls for managing noise levels at work prioritises eliminating noise hazards at the source and progressively moves to less effective measures if elimination is not feasible.
At the top of the hierarchy, elimination involves removing the noise source entirely, such as replacing noisy processes with quieter alternatives.
If elimination is impractical, engineering controls aim to reduce noise at the source, using quieter machinery, soundproofing, or barriers. Maintaining equipment regularly can also help to minimise noise because worn-out parts can increase noise levels. Regularly lubricate moving parts and replace defective components.
Next, administrative controls manage employee exposure through strategies like rotating shifts, restricting access to noisy areas, or scheduling high-noise activities during less populated times.
At the bottom of the hierarchy, personal protective equipment (PPE), such as earplugs or earmuffs, serves as the last line of defence when other controls cannot sufficiently reduce noise. This approach ensures the most effective measures are prioritised to protect employees from noise-induced harm.
Employees must be trained in the correct use, care, and maintenance of hearing protection, and PPE should be regularly inspected, cleaned, and replaced as needed to ensure effectiveness. Employees must report any defective equipment.
Creating a noise at work policy
A robust noise at work policy sets the foundation for managing noise risks effectively.
The policy should clearly state the organisationโs objectives, emphasising the prevention of noise-induced hearing loss and the implementation of control measures at the source. It should also define the scope of the policy, detailing the workplaces, roles, or activities it covers, and assign responsibilities to key stakeholders such as line managers, safety officers, and employees.
The policy should also include:
- Clear procedures for conducting noise risk assessments. It should specify how often assessments will be carried out, such as annually or when introducing new equipment or processes.
- Methods for measuring noise. The policy should require that all assessment results, including identified hazards, noise levels, and recommended controls, are documented and retained.
- Actions the organisation will take to manage noise risks, including implementing engineering controls like quieter machinery or soundproofing and administrative controls such as rotating staff or restricting access to noisy areas.
- Circumstances under which personal protective equipment (PPE) will be provided and enforced, stating that it is a last resort after other control measures have been applied.
- The organisationโs approach to providing PPE, ensuring it is fit-tested, well-maintained, and replaced as needed.
- Reference to training, specifying the training employees will receive, including information on the health risks associated with excessive noise exposure, the proper use and maintenance of hearing protection, and an understanding of noise zones.
- Health surveillance for employees exposed to high noise levels, explaining how regular hearing checks will be conducted to monitor and detect early signs of hearing damage.
Finally, the noise at work policy should commit to regular review and updates, ensuring it remains aligned with any changes in workplace conditions, equipment, or legal requirements.
As with any policy, a noise at work policy is only effective if it is read and understood by all employees.
Noise Awareness Training
Understanding and managing noise exposure limits UK standards is essential for safeguarding your employeesโ health and ensuring compliance with regulations.
Our Noise Awareness Course provides employees and managers with the knowledge to identify, assess, and control noise hazards effectively. From learning about HSE noise exposure limits and safe noise levels at work to understanding the importance of a robust noise at work policy, this course is your comprehensive solution for managing noise risks.
Find out more about Noise Awareness Training on our website or talk to our friendly team about how we can tailor the course to your organisation on 0203 011 4242/info@praxis42.com
Help ensure employees are trained in reducing their exposure to noise and how to maintain personal hearing protection equipment with our IOSH Approved and CPD Certified Noise Awareness Course.
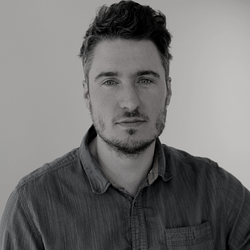
Adam Clarke
Managing Director (Consulting)