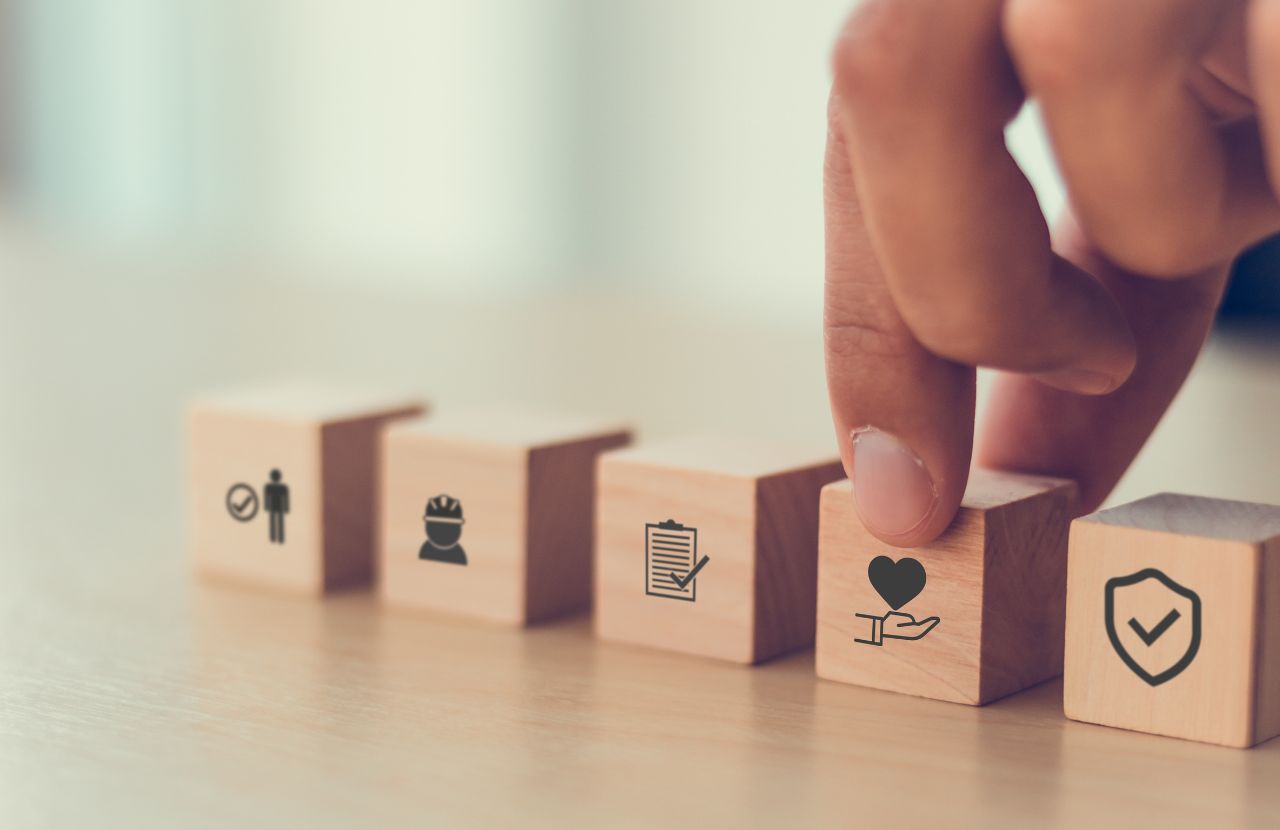
In this guide we discuss how to report an accident at work and consider how you might implement an accident reporting and investigation process that supports your organisation.
Listen to our episode of ‘Safety Made Simple’ relating to accidents in the workplace:
An effective reporting process provides you with a comprehensive record that enables you to prevent incidents reoccurring in future.
Why is it important to report accidents at work?
The aim of reporting accidents at work is to prevent them from happening again. In 2023/24 138 people lost their lives due to an accident at work.
An employer has a moral duty of care to employees and any other person who could be affected by business activities. If an accident happens, it is vital that efforts are made to prevent a reoccurrence. If an accident happens and there are no serious consequences this should be taken as a warning and an opportunity to put preventative measures in place.
Employers also have a legal duty to report certain accidents under RIDDOR (the Reporting of Incidents, Diseases and Dangerous Occurrence Regulations).
When there is an accident, the health of the injured party is paramount and you cannot put a monetary value on a life, but the commercial costs of accident should be examined too. These costs include:
- Repairs (replacing damaged equipment, carrying out repairs to premises).
- Insurance costs (compensation payouts to injured employees, higher insurance premiums).
- Sick pay to employees who are unable to work.
- Legal advice and costs.
- Lost time (when staff involved in investigation compile evidence and prepare reports).
- Wages of temporary staff hired to cover for injured employees.
- Damage to business reputation which can lead to decreased customer trust and reduced revenue.
- Fines from enforcement action (the HSE and other regulatory bodies may impose fines).
- Loss of productivity (workplace accidents can disrupt workflow).
In 2023/24 33.7 million working days were lost due to accidents and injuries at work, costing the UK economy billions. Most of that cost was borne by employers, and the employees themselves through loss of pay.
What types of accident at work cause fatalities?
Fatal accidents at work are most often caused by:
- Falls from height.
- Being struck by vehicles.
- Being trapped by something collapsing or overturning.
- Contact with machinery.
These accidents do not just happen in high-risk industries or with high-risk activities. In fact, 11 fatalities in 2020/21 occurred in the admin and support sector.
Falls from height can easily be overlooked as there is not a full understanding of when people are working at height. It is assumed that working from height only happens in construction and maintenance, but if someone is standing on a desk in an office putting up Christmas decorations, they are working at height.
The 2022/23 reports from the HSE and RIDDOR (Reporting of Diseases and Dangerous Occurrence Regulations) show that these are the most common workplace accidents:
Slips, trips and falls
Slips, trips and falls accounted for 32% of accidents. A person may slip on something or trip over an item or object which then results in a fall. We need to identify what the causes are and then put controls in place.
For slips you might consider:
- Cleaning (when and how is cleaning carried out?)
- Higher risk areas like toilets or kitchens where fluids could get spilt on the floor.
- Water ingress into a building (on a rainy day).
- Whether staff are wearing practical shoes.
- The impact of extreme weather conditions.
- Floor surfaces (are materials anti-slip?)
For trips you could look at:
- Maintained walkways (are they level and even?)
- Design of walkways (are they wide enough?)
- Obstructions (think about good housekeeping and clear floors).
- Layout of the workplace (are there trailing cables?)
- Condition of stairs/steps (are steps highlighted? Are there grips? Are stairs in good condition?)
Factors such as these need to be actively monitored at regular intervals. You may introduce a workplace inspection so you can identify issues first hand. Alternatively, a reporting system could be implemented so staff can report issues and action can be taken.
Handling, carrying and lifting
Handling, carrying, and lifting makes up 17% of injuries and encompasses:
- Carrying
- Holding
- Lifting
- Pushing
- Pulling
To reduce the risk, we need to:
- Have a full understanding of what jobs need to be done as part of daily activities. For example, is it pushing/pulling stack cages in a supermarket, or is it taking delivery of office supplies?
- Understand and appreciate the capabilities of the individual doing the task and not just assume they can do it.
- Look at what items are going to lifted or moved and how to do that (is it team lift? Do you need some equipment like a trolley?)
- And lastly, the environment in which the lifting is taking place should be considered. Is there enough space and lighting, for example?
Struck by moving object
11% of accidents in the workplace are people being struck by moving objects. It is easier to spot these hazards in high-risk environments involving vehicles and machinery, but the risk is also present in offices and shops.
Cars hitting pedestrians is the most obvious risk. Workplace transport risk assessments can be carried out to identify specific hazards and mitigate risks. You might think about how to prevent vehicles and pedestrian mixing. Can deliveries be organised out of hours when pedestrians are not present?
We must also look at how are items stored so they don’t fall on people. Also, if items need to be moved around the workplace, how is this work carried out? What equipment is used? Is the equipment suitable and does it allow the person pushing it clear visibility?
Violence
8% of injuries at work are caused by violence. This includes verbal abuse and threats as well as physical violence. Employees in customer-facing businesses are more exposed than others, but disputes can occur in any work environment.
With that in mind, we need to have processes in place to deal with disputes, or train staff to spot early signs of disputes before they escalate. In the hospitality or entertainment industry, security guards might be hired, or staff might be given panic buttons to summon help quickly.
Falls from height
Falls from height account for 8% of workplace injuries. In industries such as construction where this is an obvious risk, work is usually properly assessed and planned.
However, in other work environments working at height is often a secondary task to main work. For instance, in an accountancy firm the primary task is to manage accounts, but what if items need to be retrieved from a high shelf? We need to take a broader view of all the jobs that need to be completed, not just the primary work of a business.
So how can work at height be carried out safely? Firstly, try to avoid it altogether. Window cleaners are a prime example. Nowadays you usually see a window cleaner working with an extendable pole from the ground rather than using a ladder.
If working at height cannot be avoided, it is important to train staff to complete work safely and ensure they can use equipment correctly. The correct equipment must be supplied to do a job so people do not climb on desks or chairs, and equipment must be properly maintained.
What accidents and incidents should be reported?
It is essential to report accidents and events that have the potential to cause injury. Accidents are incidents that directly result in injury or ill health. Incidents also include events that have not resulted in injury or ill health but have the potential to do so.
Incidents include:
- Near misses or close calls where harm was narrowly avoided.
- Unsafe conditions or practices that could lead to accidents.
- Equipment malfunctions or failures that did not cause harm but could have.
- Any situation where an unexpected event or breakdown in procedures could have resulted in injury or ill health.
We also have an episode of accident reporting and investigation:
Why do we need a reporting and investigation process?
The reporting and investigation process is an information gathering exercise which looks at who, where, why and how?
If we can gather comprehensive information about an incident, we can cross reference it against existing risk assessments and safe systems of work to identify potential shortcomings.
Any accident or near miss should automatically trigger a review of a relevant risk assessment.
Once you have identified where improvements could be made you might:
- Make changes to the work process itself.
- Organise staff training.
- Introduce new equipment.
- Add further control measures.
All these measures will help prevent a reoccurrence.
(Hyperlink to new blog, ‘How to write a risk assessment’)
What prevents employees reporting incidents?
At the end of the day no matter what systems we implement mistakes will happen that cause accidents. It is how we manage accidents that matters. Accident reporting and investigation plays a vital role in helping to improve any health and safety management system.
Employees don’t report accidents for several reasons:
- People don’t find it easy to admit they made a mistake. An employee might not want to admit they weren’t working as they should, or management might not want to investigate an incident because they are concerned about revealing shortcomings in health and safety management.
- Reporting systems are not in place or employees don’t understand the system for reporting accidents at work.
- Health and safety is not seen as a priority. People don’t believe accidents can happen to them.
- Employees are afraid of reporting accidents for fear they will be penalised.
How do we encourage reporting accidents at work?
Firstly, we need a straightforward but comprehensive reporting system that gathers all the required information in a way that is easy to use and understand and train employees to use it.
For people to admit they have made a mistake they need to feel comfortable to do so, and they need to understand why it is important to report an accident at work. It comes down to having a positive health and safety culture, where people reporting accidents and near misses is welcomed and seen as a positive, rather than an exercise of assigning blame.
One industry that has a positive culture when things go wrong is the aviation industry. All commercial planes are fitted with black box recorders that can record exactly what was said or done by the crew along with all the technical information regarding the plane.
So, if they have an accident, they have all the information they need to determine what went wrong and how to prevent it happening again.
What information needs to be gathered following an accident?
When there is an accident, the following information should be gathered:
- Date and time of accident.
- Type of accident (collision, impact, fall from height, manual handling, laceration).
- Details of the injured party (name, address, contact details).
- Details of witnesses present.
- What work was being completed at the time.
- Statement of events (from the injured party if possible).
- Witness statements.
- What first aid treatment was given.
- You may want to reference any risk assessments related to the task being completed.
- Details of the person completing the form (position, signature, and date).
Who should investigate an accident?
It is preferable that a team of people with collective knowledge, experience and perspectives investigate an accident rather than just one person.
The team may include:
- The manager or supervisor responsible for the work or department where the accident took place.
- A member of the safety team or designated health and safety representative in the business.
- Experienced staff who work in the area where the accident took place or carry out the work task that was being completed at the time.
- An outside expert. This could be a health and safety consultant or an industry expert.
- A union representative, if applicable to your organisation.
How might you investigate an accident?
- Look at the accident scene. In some serious cases this will have had to be preserved to maintain evidence. You may identify physical reasons why it happened (poorly maintained workspace etc.).
- Examine any equipment that was being used. Is equipment properly maintained? Was the user properly trained?
- Take a statement from the injured party.
- Take witness statements.
- Examine the risk assessments associated with the work being undertaken at the time.
You can cross reference the injured party’s statements with those from the witnesses. You can also see how work was being completed or equipment was being used and reference that against what is recorded in risk assessments and safe systems of work.
How do you identify the cause of an accident?
There are three types of causes:
- Primary cause – what directly caused the accident.
- Secondary causes – these could be conditions or behaviours that caused the accident.
- Underlying cause – this often sits with the management of a task.
For example, in an office if someone trips over a damaged carpet and is injured, the primary cause is the damaged carpet. The carpet is damaged because the workplace is poorly maintained, so that’s the secondary cause. The underlying cause could be a lack of risk assessment. A risk assessment could have identified the trip hazard and then measures could have been put in place to repair the carpet.
To reduce the chance of an accident happening again, gather all the necessary information for a balanced conclusion to be drawn by analysing the primary, secondary, and underlying causes.
What positive changes might follow an investigation?
The information gathered in an investigation enables you to:
- Review and update risk assessments and safe working procedures to ensure they are more comprehensive.
- Identify further training staff may need to enable them to have a better knowledge of work equipment or work processes.
- Make changes to equipment so it is safer to use, such as better guarding or further failsafe mechanisms.
- Make changes to the workplace, such as better maintenance programmes to repairs issues promptly.
It is important to act on information by making the changes necessary to prevent the same incident happening again.
At Praxis42 our team of health and safety consultants can provide step by step guidance on how to report an accident at work and offer you all the support you need with the accident investigation process.