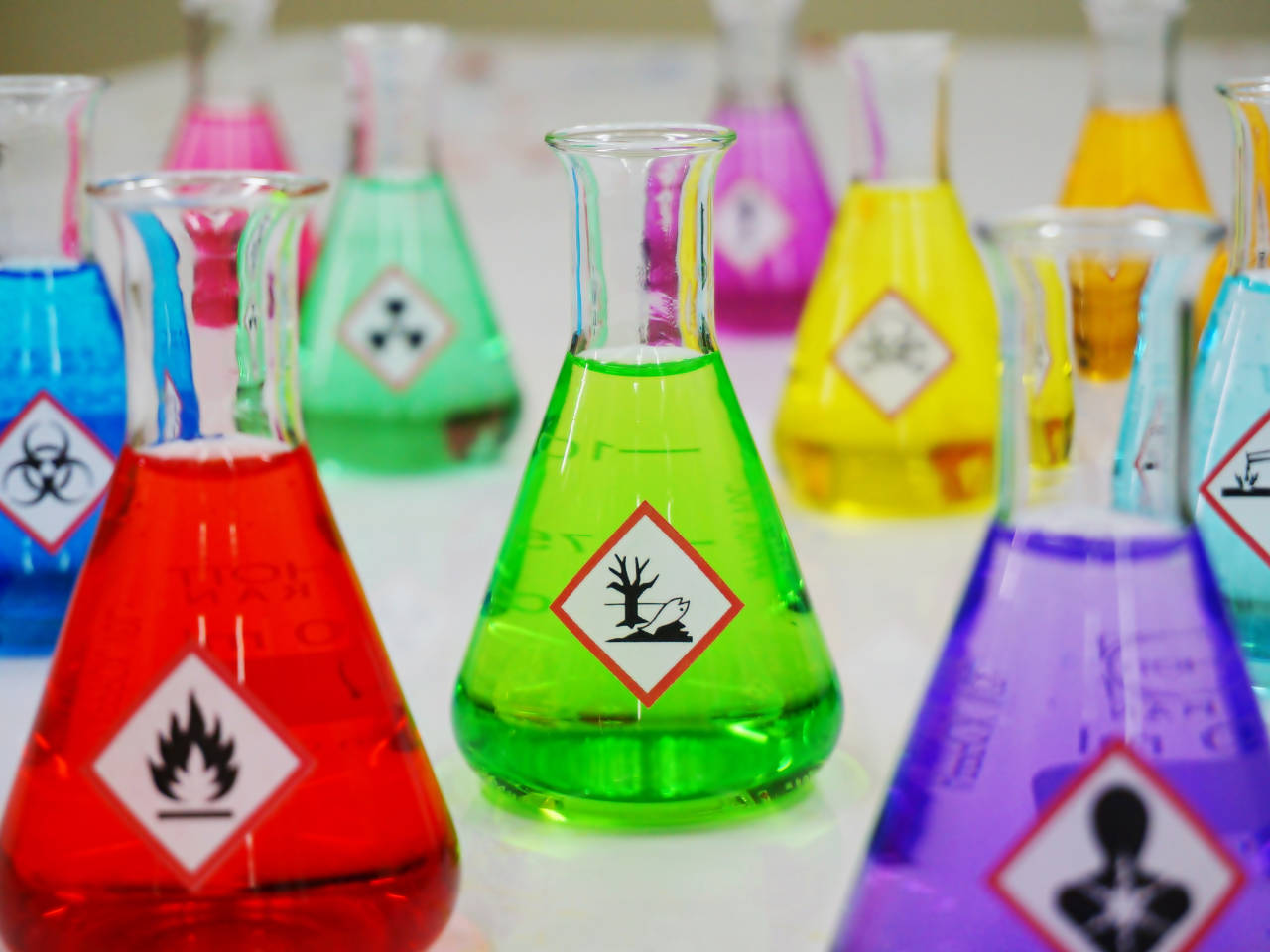
Employers, managers and employees must be trained in how to safely handle and use hazardous substances at work to prevent acute or chronic illnesses. This guide outlines how to deal with dangerous materials and why the Control of Substances Hazardous to Health (COSHH) legislation is important.
Hazardous substances at work can pose a serious risk to employees and others such as contractors. Exposure to liquids, dust, gases, fumes and liquids can lead to serious conditions such as asthma, dermatitis and lung cancer, and failure to control hazardous materials can even be fatal.
Officials figures from the Health and Safety Executive (HSE) show that an estimated 13,000 deaths a year are linked to past workplace exposure to chemicals or dust. Around 12,000 people die each year from lung cancer linked to past exposure to hazardous substances at work.
The Control of Substances Hazardous to Health (COSHH) regulations is the main legislation that covers hazardous materials in the workplace. It places legal duties on employers to prevent, reduce or control exposure among employees and others. Responsibilities include risk assessments and appropriate COSHH training for employees.
Developed by specialist health and safety consultants, our COSHH training course helps you understand your responsibilities under Control of Substances Hazardous to Health (COSHH) regulations. The course supports you to maintain health and safety standards when handling hazardous substances.
Employers’ responsibilities for hazardous substances
All employers must understand and comply with the COSHH regulations and know their responsibilities when it comes to handling and use of hazardous materials.
Those duties begin with the need to carry out a risk assessment that identifies hazards, which employees and others could be harmed and develop controls for the prevention of harm or reduction of risk from hazardous substances, materials and processes.
Employers must also provide information, instruction, supervision and training in the handling and use of hazardous substances, safe systems of work and the means of avoiding exposure. They are also required to plan for emergencies, incidents and accidents, report accidents and ill health appropriately and provide monitoring and health surveillance of employees using hazardous substances where the risk assessment shows that is required.
Basic rules for handling hazardous substances at work
Risk assessments
A risk assessment is one of the employers’ key responsibilities under COSHH. It should identify harmful substances and processes that are present in the workplace, decide which employees or other who are at risk of harm and how, and formulate a plan of precautions for preventing exposure or controlling the risks. This is referred to as the hierarchy of control.
The best control is to eliminate the need to use a hazardous substance or avoid exposure. Precautionary measures could include local exhaust ventilation, reducing temperatures so the amount of vapour released during a particular activity is removed, restricting the number of employees involved in a process and ensuring containers storing hazardous substances are correctly labelled.
Control of hazardous substances is defined as adequate if the risk of harm is “as low as is reasonably practicable”. This is when all control measures are in good working order, exposures are below the Workplace Exposure Limit where one exists, and the use of substances that cause cancer, asthma or genetic damage is avoided, prohibited or highly controlled and managed.
Organisations with five or more employees are legally required to record a COSHH assessment. Those with under five employees do not have to record the assessment, but the HSE says it is useful to do so and it makes sense to write down the assessment to help with ensuring that the controls are understood and implemented.
The risk assessment should be regularly reviewed to ensure it reflects the current workplace environment and in the event of any accidents, incidents, reports of ill health, results of health surveillance, audits and inspections.
Storing hazardous materials
All hazardous substances should be properly stored. Flammable materials must be kept in closed containers inside fire resistant cabinets or bins that are designed to retain spillages. The cabinets and bins must be in well-ventilated rooms, and flammable substances should be stored separately from other dangerous materials.
The Health and Safety Executive says: “It is recommended that the maximum quantities that may be stored in cabinets and bins are no more than 50 litres for extremely, highly flammable and those flammable liquids with a flashpoint below the maximum ambient temperature of the workroom/working area; and no more than 250 litres for other flammable liquids with a higher flashpoint of up to 55°C.”
Labelling hazardous materials
All hazardous substances should be appropriately labelled with details about what the substance is, how to use it safely and warnings such as ‘avoid contact with skin’.
There are nine key internationally recognised hazardous symbols that let employees and others easily identify hazardous materials and the risks they pose. For example, if the symbol is a dripping test tube on a hand and material it is corrosive and therefore presents a risk to exposed skin; an exclamation mark indicates it’s a health hazard such as an irritant to the eyes; and a skull and crossbones to indicate acute toxicity that may be hazardous through inhalation.
Many hazardous substances are not labelled, as in their normal state they pose no risk as is the case with hardwood which only becomes hazardous when sawn or machined and creates respirable dusts that are carcinogenic.
Planning for emergencies
Employers should prepare for how to respond to an accident or incident and protect the emergency services that may come to assist. Employees must understand emergency procedures such as evacuating the premises, cleaning up spillages, stopping processes and dealing with fires. Emergency equipment, including eye washing stations, should always be available, kept clean and regularly inspected. Employees should receive appropriate first aid training with specific first-aiders on hand to respond to an accident or incident.
Hazardous substances training
Training employees on the risks and what to do if they are exposed to hazardous materials is a legal requirement for organisations whose employees work with substances hazardous to health. Look for an accredited Control of Substances Hazardous to Health (COSHH) training course to provide employees with the knowledge that they need and topped up with training in the organisations safe systems of work, arrangements and controls.
Health surveillance
Health surveillance is a measure that helps employers understand if the controls of exposure they have implemented are working or not . It is necessary when there is a disease associated with the substance being used, such as asthma, cancer and dermatitis. A good example of health surveillance would be examining the hands of cleaners to ensure that the skin is in good condition, free from visible signs of irritation or reddening or is overly dry.
Suitable tests, questionnaires or examinations should be carried out, the results should be interpreted, and actions should be taken to review the controls, eliminate or control exposure.
Reporting accidents and incidents
All accidents, incidents, dangerous occurrences and work-related ill health in the workplace should be reported and recorded under the Reporting of Injuries, Diseases and Dangerous Occurrences Regulations 2013 (RIDDOR). Employers, the self-employed and people in control at premises must also report certain serious workplace incidents, occupational diseases and specified near misses to the Health and Safety Executive (or HSE NI in Northern Ireland).
For dangerous materials, reportable accidents or incidents include exposure to carcinogens, mutagens and biological agents, as well as incidents involving gas.
Personal protection equipment (PPE)
Employers should ensure employees working with hazardous substances are provided with appropriate PPE such as eye protection and gloves where a risk assessment shows that they are an acceptable control measure. The equipment must be properly maintained and regularly inspected to check for any damage or defects and replaced when necessary. Employees must be trained in the safe use, storage, inspection and cleaning of the equipment and understand what to do in the event that the equipment needs replacing.
Ensure your employees are trained in the safe handling of hazardous substances – our COSHH training course teaches you your responsibilities under Control of Substances Hazardous to Health (COSHH) regulations with guidance on handling hazardous substances.