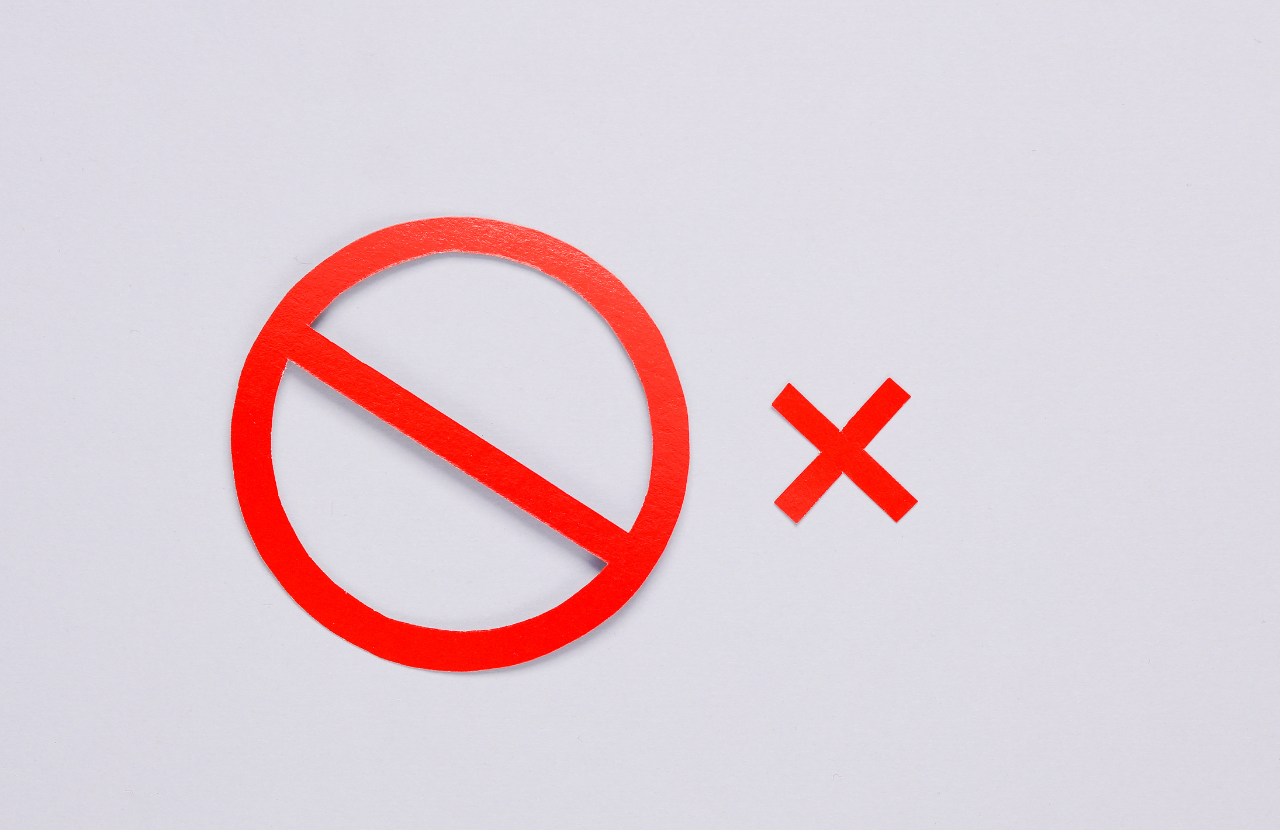
A health and safety prohibition notice is a formal document issued by an inspector employed by the Health and Safety Executive (HSE) or the local authority.
The purpose of a prohibition notice is to stop a specific work activity that poses an imminent risk to the health and safety of workers or the public. It serves as an enforcement tool under the Health and Safety at Work etc. Act 1974, which is designed to protect individuals from harm in workplaces.
Prohibition notices play a vital role in ensuring that health and safety risks are dealt with swiftly and effectively. They protect workers and in some cases the public from immediate harm.
Here we discuss what a prohibition notice is and the circumstances that can lead to a prohibition notice being issued.
What is a prohibition notice? Key features
A prohibition notice requires an employer to stop a particular activity immediately.
The activity can only be resumed after appropriate safety measures have been implemented to eliminate or reduce the risk to an acceptable level. A risk is considered acceptable if the probability of harm occurring and the severity of harm if an incident did occur are as low as reasonably practicable.
The prohibition notice will clearly specify what activity must cease and what steps need to be taken for the activity to become safe.
This immediate requirement is crucial in high-risk environments like construction sites, where hazards such as falling from heights or exposure to dangerous substances like asbestos can lead to severe injuries or fatalities.
Legal obligation
A prohibition notice creates a binding legal obligation on the employer or any person in control of the hazardous activity. This means that failure to comply with the notice is not just a breach of health and safety regulations but a criminal offence.
The consequences of ignoring or failing to act on a prohibition notice can be severe. The organisation or individuals responsible for the activity may face prosecution in court, where they could be subject to significant fines or even imprisonment if the breach is deemed severe enough.
For businesses, non-compliance can also result in reputational damage, financial losses, and the potential for a temporary or permanent cessation of operations if the necessary safety improvements are not made.
In cases where work continues despite a prohibition notice, the HSE has the authority to take escalating enforcement actions, including prosecuting individuals such as directors or managers who are responsible for health and safety in the workplace.
Broad application
The scope of a prohibition notice is wide, and it can be applied across all industries and types of work activities. Prohibition notices are issued in industries such as construction, manufacturing, healthcare, hospitality, transport, and public services.
For example, in construction, a prohibition notice might be issued to stop the use of dangerous scaffolding or inadequately secured machinery. In a manufacturing setting, it could halt work involving unsafe handling of hazardous chemicals.
Who can issue a prohibition notice?
A prohibition notice can only be issued by authorised inspectors from the Health and Safety Executive (HSE) or local authority environmental health departments. Inspectors are experienced professionals trained to identify hazards and assess the risks posed by certain activities.
Inspectors issue prohibition notices during routine inspections, following workplace incidents that highlight unsafe practices, when concerned parties report directly to them.
When issuing a notice, the inspector must believe that there is a significant risk of serious personal injury or ill health if the activity continues. The inspector will explain the specific reasons for the prohibition in the notice, detailing the risk and the unsafe activity in question. This provides a clear directive to the employer or duty holder on what needs to stop and why.
In cases where employers dispute the issuance of a prohibition notice, they can appeal the decision. However, this appeal process does not suspend the notice, meaning the work activity must remain stopped until a final decision is made.
Under what circumstances may a prohibition notice be issued?
A prohibition notice may be issued when there is an imminent risk of serious injury or harm to health.
Here are some common circumstances under which a prohibition notice might be issued:
- Dangerous work at height because proper safety precautions have not been taken e.g. missing guardrails
- Unsafe use of machinery. For example, equipment may be poorly maintained, lacking guarding or dangerously operated.
- Unsafe removal or disturbance of asbestos.
- Exposure to dangerous chemicals without proper safety controls in place. e.g. local exhaust ventilation
- Unsafe electrical practices such as working on live equipment, or unsuitable permit to work system
- Structural instability or unsafe working conditions. For example, if there is a risk of a building collapsing.
- Risk of explosion or fire because flammable materials are improperly stored
- Working in confined spaces such as silos, tanks or underground chambers without proper safety measures in place, e.g. gas detection
- If a serious incident or accident has occurred due to unsafe procedures or practices.
- Unsafe working practices in high-risk environments such as agriculture, construction or mining.
What happens after a prohibition notice is issued?
Once the activity is halted, the organisation must conduct a thorough risk assessment to understand the full extent of the issue. This will involve reviewing the working environment, the equipment being used, and the procedures followed by employees.
The risk assessment should focus on the risk that led to the notice and determine how it can be eliminated or significantly reduced.
External health and safety consultants may be required to support this evaluation, depending on the complexity of the issue.
Corrective actions will vary depending on the nature of the hazard that triggered the prohibition notice. Here are a few common types of actions:
Implementing new safety protocols
In some cases, the organisation may need to introduce new or updated safety protocols. This could include revising risk assessments, creating safer working methods, or enhancing supervision.
For example, if a notice is issued for unsafe work at height, new protocols might be needed to ensure proper use of fall arrest systems.
Introducing protective measures
Another common corrective action is the introduction of personal protective equipment (PPE) or other physical safeguards.
For instance, if workers are exposed to hazardous chemicals without appropriate protection, the employer will need to provide adequate PPE such as gloves, respirators, or protective clothing.
Also, physical barriers or guards may need to be installed around dangerous machinery to prevent accidents.
Repairing or replacing faulty equipment
If the hazard relates to faulty or poorly maintained equipment, such as a defective machine or scaffolding, the equipment may need to be repaired or replaced entirely.
Providing additional training
In many cases, unsafe practices identified are linked to a lack of proper health and safety training.
Employees may need to be retrained on safe working procedures, particularly in high-risk environments like construction or manufacturing.
For example, if the prohibition notice was issued because workers were using machinery incorrectly, additional training on safe machine operation may be required before the activity can resume.
How can you ensure your workplace practices are safe?

Our IOSH Managing Safely course empowers managers with the knowledge and tools necessary to ensure your organisation complies with health and safety laws.
Managers significantly influence safety culture, and the course helps them understand their responsibilities in fostering safe behaviours, complying with legal obligations, and preventing accidents.
By ensuring managers understand the human, legal, and financial consequences of incidents, the course emphasises the importance of prioritising health and safety to protect youโre your employees and organisation.
For a course summary, please visit our IOSH Managing Safely webpage, or contact our friendly team today on 0203 011 4242 or info@praxis42.com.
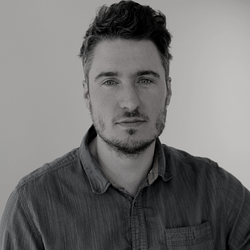
Adam Clarke
Managing Director (Consulting)